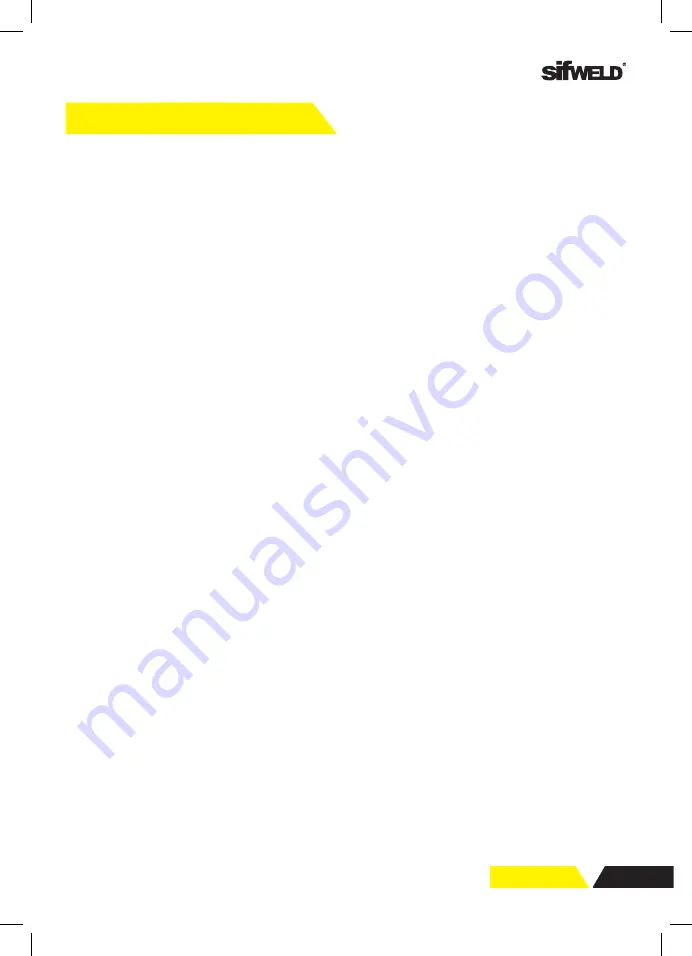
33
3.4 Wire Feed Roller
The importance of smooth consistent wire feeding during MIG welding cannot be emphasized enough.
Simply put the smoother the wire feed then the better the weld.
Feed rollers or drive rollers are used to feed the wire mechanically through the length of the welding
gun cable. Feed rollers are designed to be used for certain types of welding wire and they have different
types of grooves machined in them to accommodate the different types of wire. The wire is held in the
groove by the top roller of the wire drive unit and is referred to as the pressure roller, pressure is applied
by a tension arm that can be adjusted to increase or decrease the pressure as required. The type of wire
will determine how much pressure can be applied and what type of drive roller is best suited to obtain
optimum wire feed.
Solid Hard Wire
- Such as steel, stainless steel requires a drive roller with a “V” shape groove for optimum
grip and drive capability. Solid wires can have more tension applied to the wire from the top pressure
roller that holds the wire in the groove and the “V” shape groove is more suited for this. Solid wires are
more forgiving to feed due to their higher cross-sectional column strength, they are stiffer and don’t
deflect so easily.
Soft Wire
– Such as aluminum, require a “U” shape groove. Aluminum wire has a lot less column
strength, can bend easily and is therefore more difficult to feed. Soft wires can easily buckle at the wire
feeder where the wire is fed into inlet guide tube of the torch. The U-shaped roller offers more surface
area grip and traction to help feed the softer wire. Softer wires also require less tension from the top
pressure roller to avoid deforming the shape of the wire, too much tension will push the wire out of
shape and cause it to catch in the contact tip.
Flux Core / Gasless Wire
- These wires are made up of a thin metal sheath that has flux and metal
compounds layered onto the surface and then rolled into a cylinder to form the finished wire. The wire
cannot take too much pressure from the top roller as it can be crushed and deformed if too much pres-
sure is applied. A knurled-V drive roller has been developed and it has small serrations in the groove, the
serrations grip the wire and assist to drive it without too much pressure from the top roller. The down
side to the knurled wire feed roller on flux cored wire is it will slowly over time bit by bit eat away at the
surface of the welding wire, and these small pieces will eventually go down into the liner. This will cause
clogging in the liner and added friction that will lead to welding wire feed problems. A U groove wire
can also be used for flux core wire without the wire particles coming off the wire surface. However, it is
considered that the knurled roller will give a more positive feed of flux core wire without any deforma-
tion of the wire shape.
Summary of Contents for Evolution MTS500 DP
Page 44: ...44 Notes ...
Page 45: ...45 Notes ...