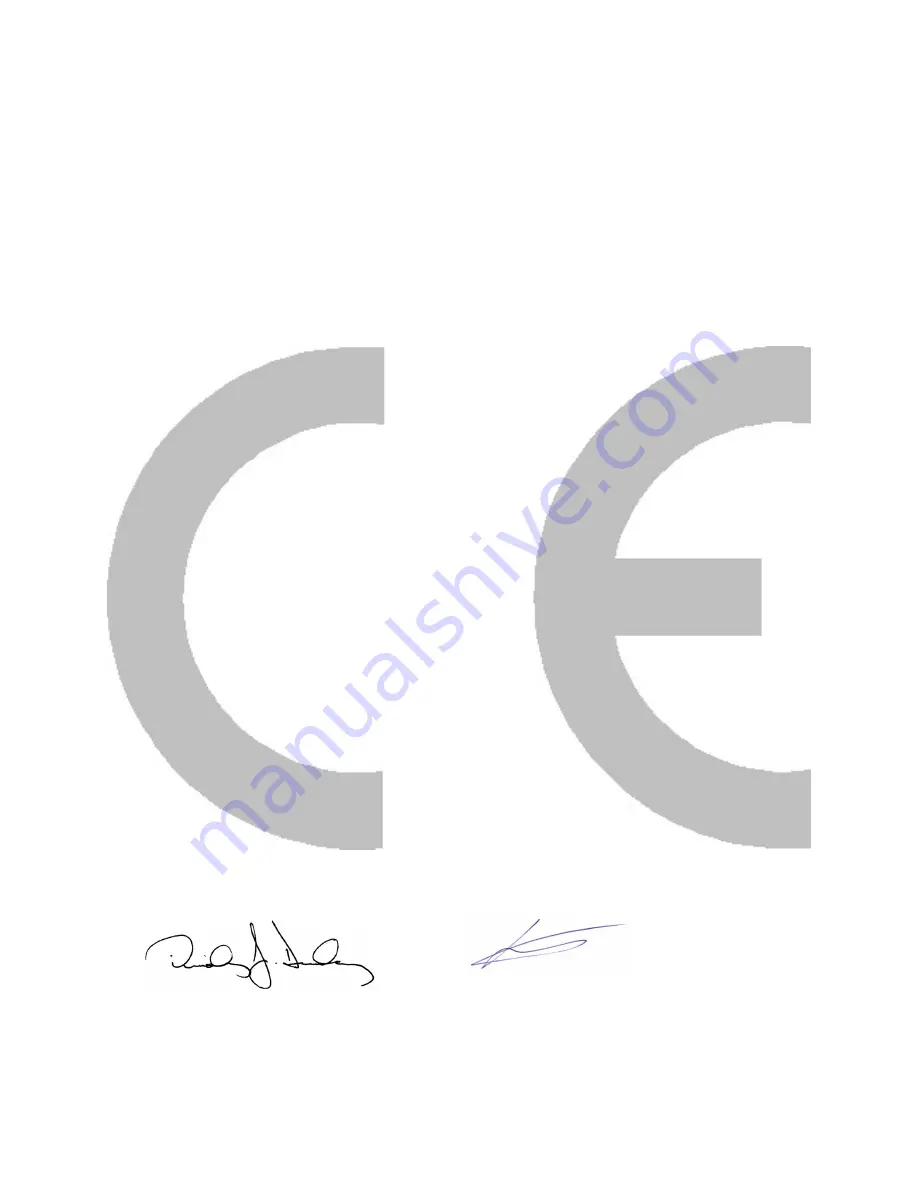
EU Declaration of Conformity
The Supply of Machinery (Safety) Regulations
1992 (S.I. 1992/3073)
It is hereby declared that the undermentioned machinery has been designed and
constructed to comply with the health and safety requirements defined in EC Directives
2006/42/EC, 2006/95/EC and 2004/108/EC.
Machine Supplier:
Signode
3700 West Lake Avenue
Glenview, IL 60026 U.S.A.
Place of Declaration:
U.S.A.
Declaration Date:
1 March, 2013
Machine Description:
Grippack
Machine Type:
Battery Powered Hand Tool
Provisions with which machinery complies:
2006/42/EC
2006/95/EC
2004/108/EC
Harmonized EuroNorms with which machinery complies:
EN 60734-1:2009
EN 60745-2-18:2009
EN ISO 12100:2010
EN 60204-1:2006
EN 13849-1
Technical Standards with which machine complies:
NA
EC Authorized Representatives:
Tim Dunlavy
G. S. Leine
Manufacturing Manager
Product Support Manager
Signode
Signode Europe
3700 West Lake Avenue
Westring 13, 40721
Glenview, IL 60026 U.S.A.
Hilden Germany
Phone 800-323-2464
Phone 49-2103-96067-0
27