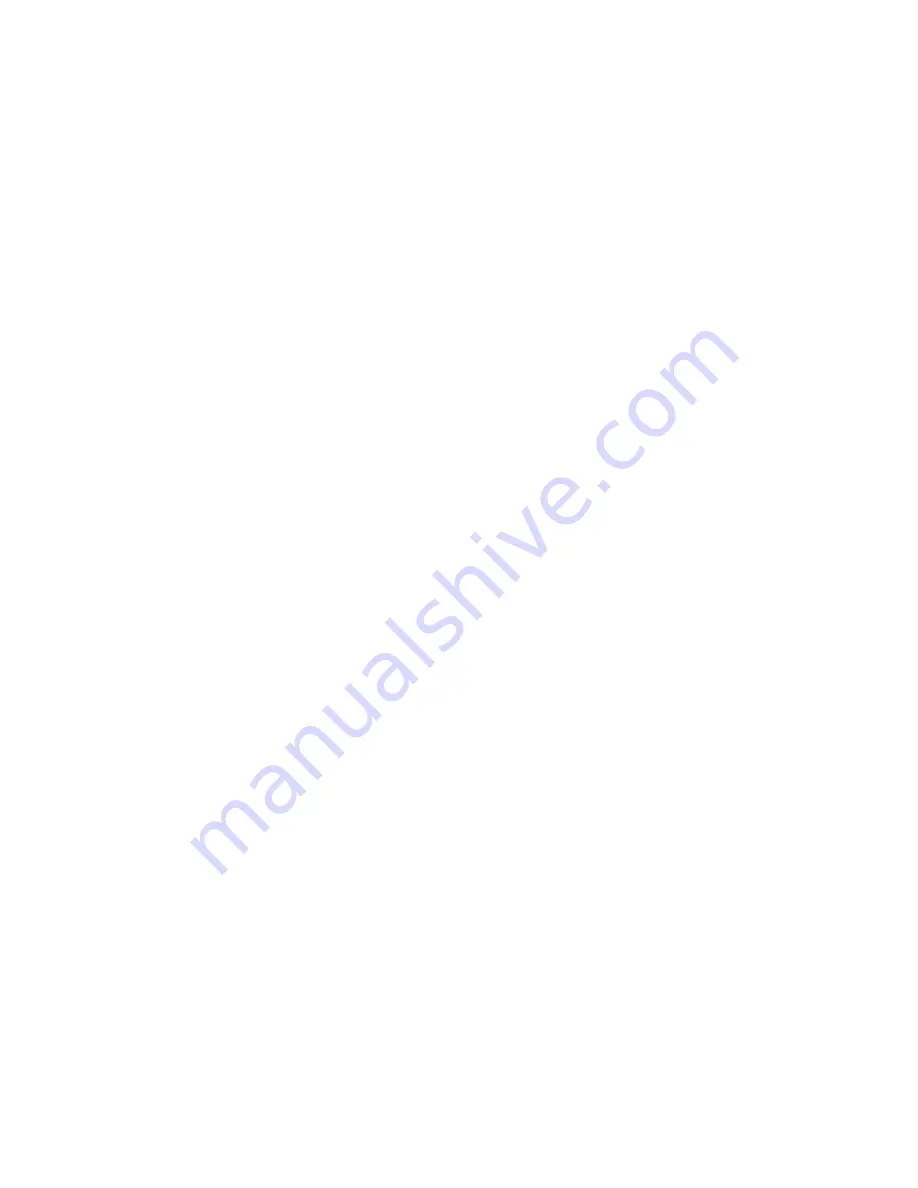
Theory of Operation: (High Speed)
Pressure sensitive tape is applied to the corrugated box as it passes by the
cartridge. The box will contact the front arm roller which has pressure sensitive
tape adhesive side facing outward towards the oncoming box. The front leading
side of the box will contact the front roller arm and the tape will adhere to the
box. As the box continues to move forward the front roller arm and knife arm will
be rotated into the frame of the cartridge. The amount of force exerted on the
box as tape is being applied is adjustable by changing the position of the main
spring. The front arm initial application force can be set to accommodate the
strength of the box as well as the sturdiness of the contents in the box.
As the front arm application roller transitions from the leading panel of the box
to the top major flaps a separate wipe down spring is engaged. The sole
purpose of this spring is to add speed to the rear wipe roller actuation to insure
the rear tape tab is completely wiped to the rear trailing panel of the box. At this
time the knife arm is retracted into the cartridge and the knife blade guard is
fully retracted uncovering the blade. As the knife arm rotated into the cartridge
the knife activation spring extends, generating cut force.
As the box proceeds pass the cartridge the front arm roller will no longer
contact the major flaps of the box, but the rear wipe roller will still contact the
major flaps. Eventually as the box travels the knife arm will completely stop
contacting the major flaps of the box. This will allow the knife arm to travel back
towards its home position allowing the knife blade to puncture and cut through
the tape. As the box continues move the rear wipe arm roller will no longer
contact the major flaps of the box. This will allow the wipe arm roller to spring
out of the cartridge and contact the rear tab length of tape and press against the
trailing panel of the box. The rear wipe arm roller booster spring starts the wipe
and the main cartridge spring finishes the wipe sequence.
The box travelling pass the cartridge is the vehicle which pulls the tape through
the cartridge. The cartridge is design to run most pressure sensitive tapes with
no required adjustments. However in some cases it may be necessary to adjust
tape tensions. The cartridge will operate at speeds up to 170 feet/minute.
Summary of Contents for Little David LD16AE 2.0
Page 1: ...Little David Case Sealer LD16AE 2 0 Automatic Random Case Sealer Operator sManual ...
Page 17: ...Page 13 Limit switches and Solenoid valve locations ...
Page 33: ...Page 29 MECHANICAL DRAWINGS AND SCHEMATICS Chapter 10 ...
Page 41: ......
Page 47: ......
Page 48: ...ALTER BOX FOR MIRROR IMAGE FOR FRESHLY OREDER ...
Page 49: ......
Page 50: ......
Page 51: ......
Page 52: ......
Page 53: ......
Page 54: ......
Page 55: ......
Page 56: ......
Page 57: ......
Page 74: ...Knife guard is shown open in both figures Figure 12B Blade release bar ...
Page 83: ...1 N401 359 COMPACT CYLINDER 1 N401 349B CYLINDER x 4 W CUSHION 2 CAC60 0047 3 BRONZE BUSHING ...
Page 106: ......