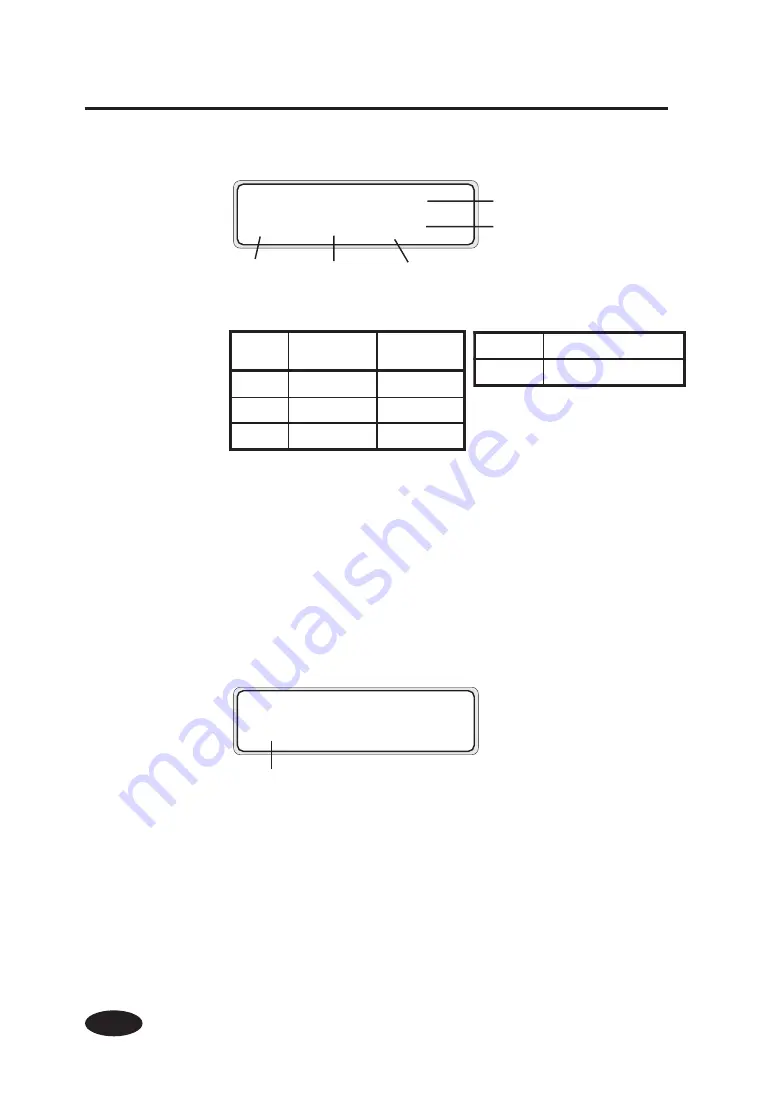
4-4
LCD Display
(1) Display in normal mode
Display: (AAA to CCC, YYY to ZZZ)
Temperature unit: (U)
• Preset temperature display
When using fahrenheit display, the temperature is displayed by
three digits.
(99 fahrenheit or less temperature is displayed with space ;plus
2 digits.)
• Display renewal period
The temperature is measured at every 5 second and renewed.
AAAU BBBU CCCU
XXXU YYYU ZZZU
Heater
Setup
temperature
Current
temperature
FRONT
AAA
XXX
BBB
YYY
REA
CCC
ZZZ
C
Celsius
F
Fahrenheit
Preset temperature
Current temperature
Front heater
Print heater
Rear heater
(2) Display at heater ON
When each heater is heated, “+” is displayed in place of the unit of
each heater current temperature on the second line. The unit display is
restored at the completion of heating. In the display example shown
above, the front heater is heated.
AAAU BBBU CCCU
XXX+ YYYU ZZZU
Heater ON
Summary of Contents for IP-6600
Page 4: ......