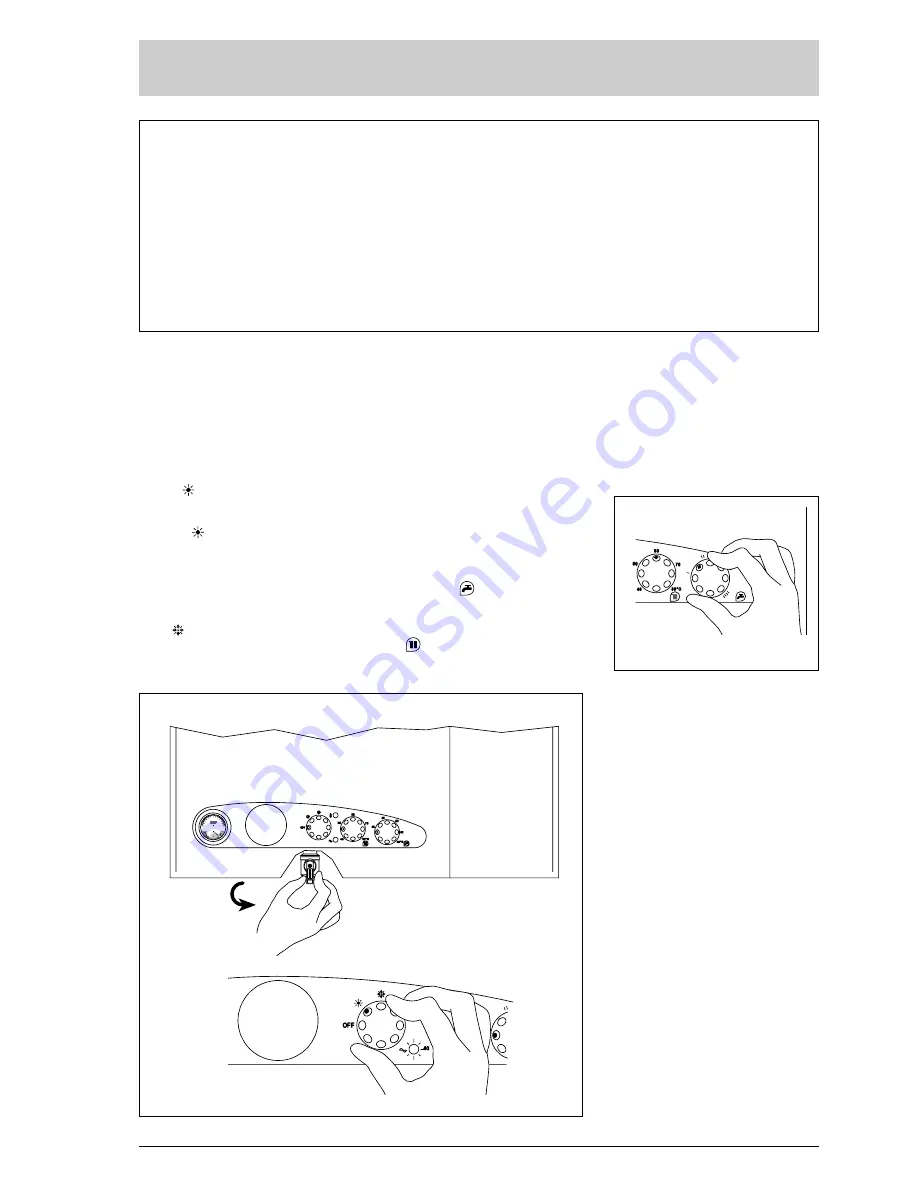
92
USER INSTRUCTIONS
WARNINGS
–In case of fault and/or incorrect equipment operation, deactivate it, without making any repairs or taking any direct
action. Contact the authorised technical staff.
–The installation of the boiler and any servicing or maintenance job must be carried out by qualified personnel. Under
no circumstances, the devices sealed by the manufacturer can be tampered with.
–It is absolutely prohibited to block the intake grilles and the aeration opening of the room where the equipment is
installed.
LIGHTING AND OPERATION
BOILER IGNITION
(fig. 1)
Open the gas valve and light the appliance
by turning the rotary switch to summer
position
. The green led indicates that
electricity is being supplied to the appliance.
– With the rotary switch in the summer
position
, the boiler will start-up upon
demand for domestic hot water, and run
at full power to reach the selected tempe-
rature. The gas feeding pressure will then
automatically vary to ensure that the
required temperature is kept constant.
–With the rotary switch in the winter posi-
tion
, once the boiler has reached the
value set on the heating potentiometer, it
will start to modulate in automatically in
order to supply the required power out-
put to the system.
The operation of the boiler will be stop-
ped through the intervention of the ther-
mostat or timer.
TEMPERATURES ADJUSTMENT
(fig. 2)
–The D.H.W. temperature can be adju-
sted by turning the knob of the D.H.W.
potentiometer
which has a range of
between 40 to 60°C (fig. 2).
–The C.H. temperature can be adjusted by
turning the knob of the C.H. potentiome-
ter
which has a range of between 40
to 80°C. To ensure optimal boiler effi-
ciency at all times, we recommend not to
drop below a minimum working tempera-
ture of 50°C.
TURNING THE BOILER OFF
(fig. 1)
To turn the boiler off place the rotary switch
on the
OFF
position. If the boiler is not going
to be used for a lengthy period it is advised
to turn off the electricity supply, close the
gas cock, and if low temperatures are fore-
seen, empty the boiler and the hydraulic
system to avoid breakage in the tubes due
to the freezing of the water.
GAS CONVERSION
Should it be necessar y t o conver t the
appliance to a different gas from the one
for which the boiler has been equipped,
approach the technical staff.
CLEANING AND MAINTENANCE
Preventive maintenance and checking of
the efficient operation of the equipment
and safety devices must be carried out
exclusively by the authorized technical
staff. The boiler is supplied with an elec-
tric cable. Should this require replace-
ment, contact exclusively an authorised
technical staff.
APRE
0
30
60
90
120
bar
°
C
0
3
4
1
Fig. 1
Fig. 2
OPEN