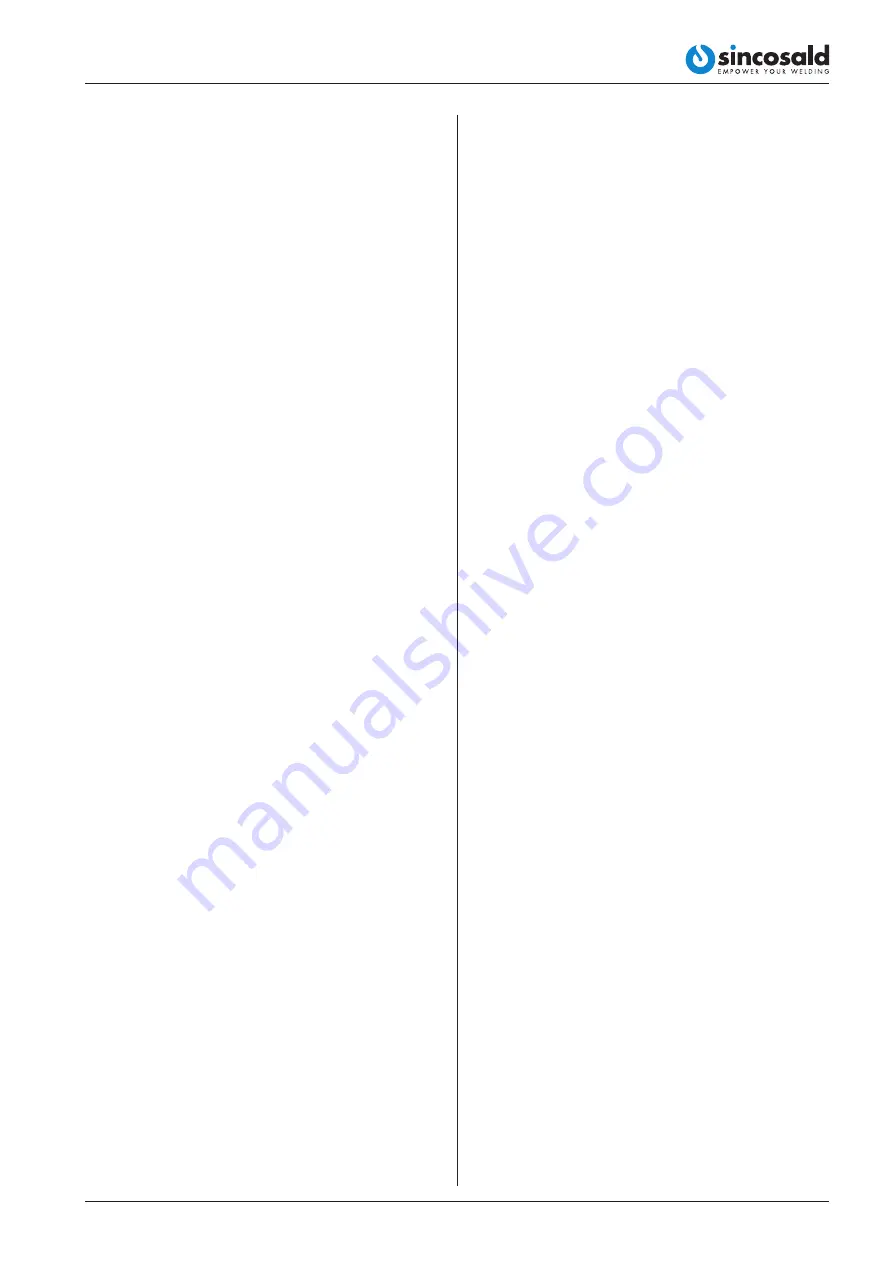
duty cycle) is detected and protection is activated.
When protection is activated, welding output will be
disabled until the safety system senses the overload
has reduced sufficiently and indicator lamp goes out.
May also trigger if machine experiences an internal
power circuit failure.
Water Cooling System Error Indicator (30)
When using the integrated water cooler, the system
is equipped with a pressure sensor. If the coolant
pressure is insufficient, this indicator will light and
the welding output will not be able to be active, in
order to protect the torch and cooling system.
6.2. POWER SUPPLY INPUT
CONNECTION
The TIG series of welding machines is designed to
operate on a 380V AC power supply.
When the power supply voltage is over the safe work
voltage, there are over voltage and under voltage
protection inside the welder, the alarm light will on,
at the same time, the current output will be cut off.
If the power supply voltage continually goes beyond
the safe work voltage range, it will shorten the welder
life-span. The below measures can be used:
•
Change the power supply input net. Such as,
connect the welder with the stable power supply
voltage of distributor;
•
Induce the machines using power supply in the
same time;
•
Set the voltage stabilization device in the front of
power cable input.
pulse mode is that the base current should be suf-
ficient to maintain the existing molten weld pool,
while the peak current is sufficient to melt new metal
in order to move/ expand the molten weld pool. In-
creased pulse frequency will have the effect of mak-
ing the arc more tightly focused which is useful for
fine stainless work and similar. Pulsing can also be
used to help move the weld pool, this technique is
useful for welding out of position or with materials
that have higher viscosity weld pool. Higher pulse
duty setting will give greater heat input, while lower
pulse duty will have the opposite effect.
MMA Parameter Setting
Hot start (25)
Hot start provides extra power when the weld starts
to counteract the high resistance of the electrode and
workpiece as the arc is started. setting range (0-10).
Arc force (23)
An MMA welding power source is designed to pro-
duce constant output current (DC).This means with
different types of electrode and arc length; the weld-
ing voltage varies to keep the current constant. This
can cause instability in some welding conditions as
MMA welding electrodes will have a minimum volt-
age they can operate with and still have a stable arc.
Arc Force control boosts the welding power if its sens-
es the welding voltage is getting too low. The higher
the arc force adjustment, the higher the minimum
voltage that the power source will allow. This effect
will also cause the welding current to increase. 0 is
Arc Force off, 10 is maximum Arc Force. This is prac-
tically useful for electrode types that have a higher
operating voltage requirement or joint types that re-
quire a short arc length such as out of position welds.
Water / Air Cooling Selection Button (28)
When using the integrated water cooling system
with a water cooled torch, select the ‘water’ option
(26). This will activate the water cooler power (the
water cooler must also be switched on the rear panel)
and the water cooling protection system. If using air
cooled torch, select ‘Air’ option (27).
Note the welding machine comes standard with
a water cooled torch system. Operating a water
cooled torch without water cooling will quickly
cause serious damage to the torch. Damage to torch
or components due to lack of water is not covered
under machine warranty.
Alarm Indicator (29)
Lights when over voltage, over current, input phase
loss or electrical overheating (due to exceeding
23
1.995.229 EN - Rev. 1.1
NOVATIG 403 DC PULSE