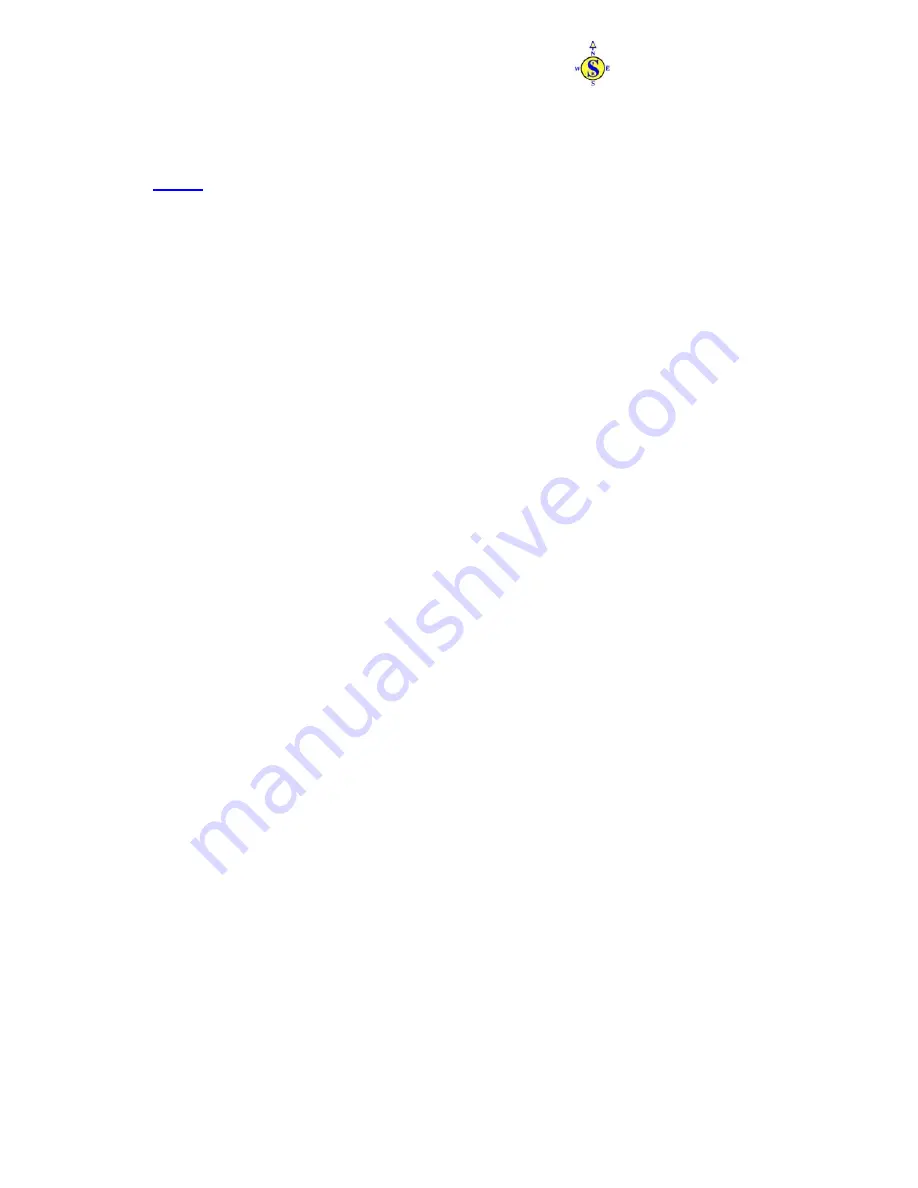
SIRS NAVIGATION LTD
COMPONENT MAINTENANCE MANUAL
C Storage Conditions and Storage Life
NOTE: See publication SAV/OH/SPR, available from SIRS Navigation Ltd.
i) Storage Conditions
1. The compass must be stored in its primary package
2. The compass must be kept away from all magnetic sources.
3. The compass can be stored up to 5 years before being re-certified.
4. After re-certification, the compass can be stored for a further 5 years.
5. After 10 years of storage the compass must be overhauled to replace the
Silicone fluid and rubber gaskets.
ii) Storage Life Tests
a) Remove unit from packing.
b) Examine unit visually for signs of corrosion or damage.
c) Do the serviceability tests detailed in Page Block 1001 TESTING.
d) Pack in accordance with paragraph. B.
PAGE 15002
APR 10/03
34-25-21
The document reference is online, please check the correspondence between the online documentation and the printed version.