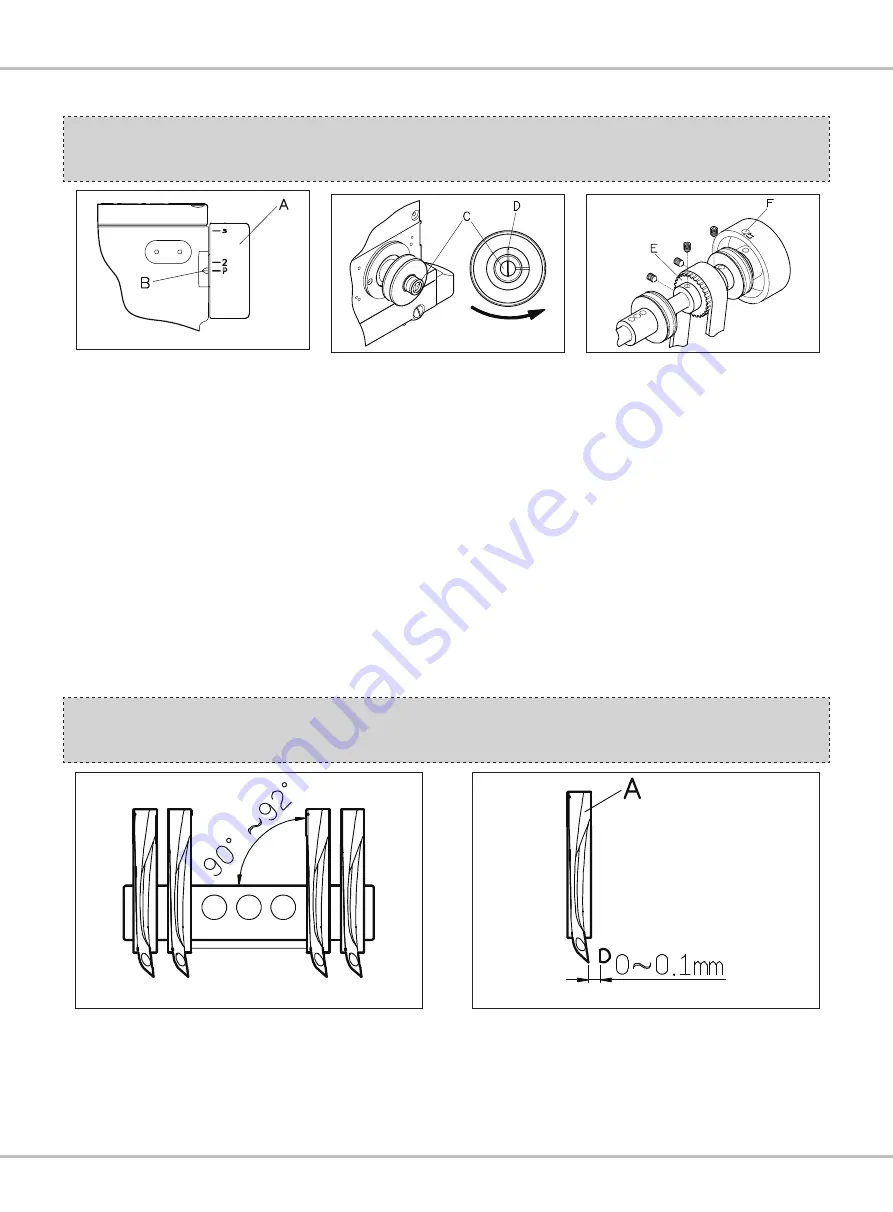
1.
勾針和勾針座的角度
90
度
~92
度。
(
圖
14)
2.
左右移動勾針座,使勾針
(A)
的尖點與針的
凹槽處間隙為
0~0.1mm
。
(
圖
15)
圖
14/Fig 14
圖
15/Fig 15
1.
轉動手輪
(A)
,把手刻度
P
對準記號
(B)
,此
時針棒位於上死點。
(
圖
11)
2.
此時,下軸
(C)
的端面線是垂直的,請確認
皮帶輪
(D)
逆時針方向的第一顆螺絲向上。
(
圖
12)
3.
調整時,上軸皮帶輪
(E)
的
4
顆螺絲鬆開,
轉動手輪
(F)
使手輪的刻度
LT
洞口與下軸
(C)
端面線垂直後,將上軸皮帶輪
(E)
的螺絲鎖
緊。
(
圖
13)
調整勾針與針的同步
TIMING OF THE LOOPER TO THE
NEEDLES
1.Turn the hand pulley (A) and align mark B
on the hand wheel mark P. The needle bar
position would be at the top of its stroke.
(Fig 11)
2.In this case, the lower shaft (C) should be
vertical. And make sure if the first screw
of the turning direction is above the V-belt
pulley (D) or not.(Fig 12)
3.If not, loosen screw (4pcs) on the timing
pulley (E) of the upper shaft to be adjusted
to the above-mentioned position.
Make sure of tightening screw (G) (4pcs) again
after adjustment.(Fig 13)
1.The angle between the needle and the
looper is 90~92 degrees.(Fig 14)
2.The clearance between the looper and the
needle when the point of looper passes the
scarf of the needle should be 0~0.1mm.
(Fig 15)
調整上軸與下軸的同步
TO ADJUST THE TIMING BETWEEN
THE UPPER AND THE LOWER SHAFT
圖
11/Fig 11
圖
13/Fig 13
圖
12/Fig 12
P12
Introduction
Summary of Contents for NC008
Page 1: ...NC008 INSTRUCTIONS BOOK PARTS LIST...
Page 27: ...P24...
Page 28: ...P25...
Page 29: ...P26...
Page 30: ...P27...
Page 31: ...P28...
Page 32: ...P29...
Page 33: ...P30...
Page 34: ...P31...
Page 35: ...P32...
Page 36: ...P33...
Page 37: ...P34...
Page 38: ...P35...
Page 39: ...P36...
Page 40: ...P37...
Page 41: ...P38...
Page 42: ...P39...
Page 43: ...P40...
Page 44: ...P41...