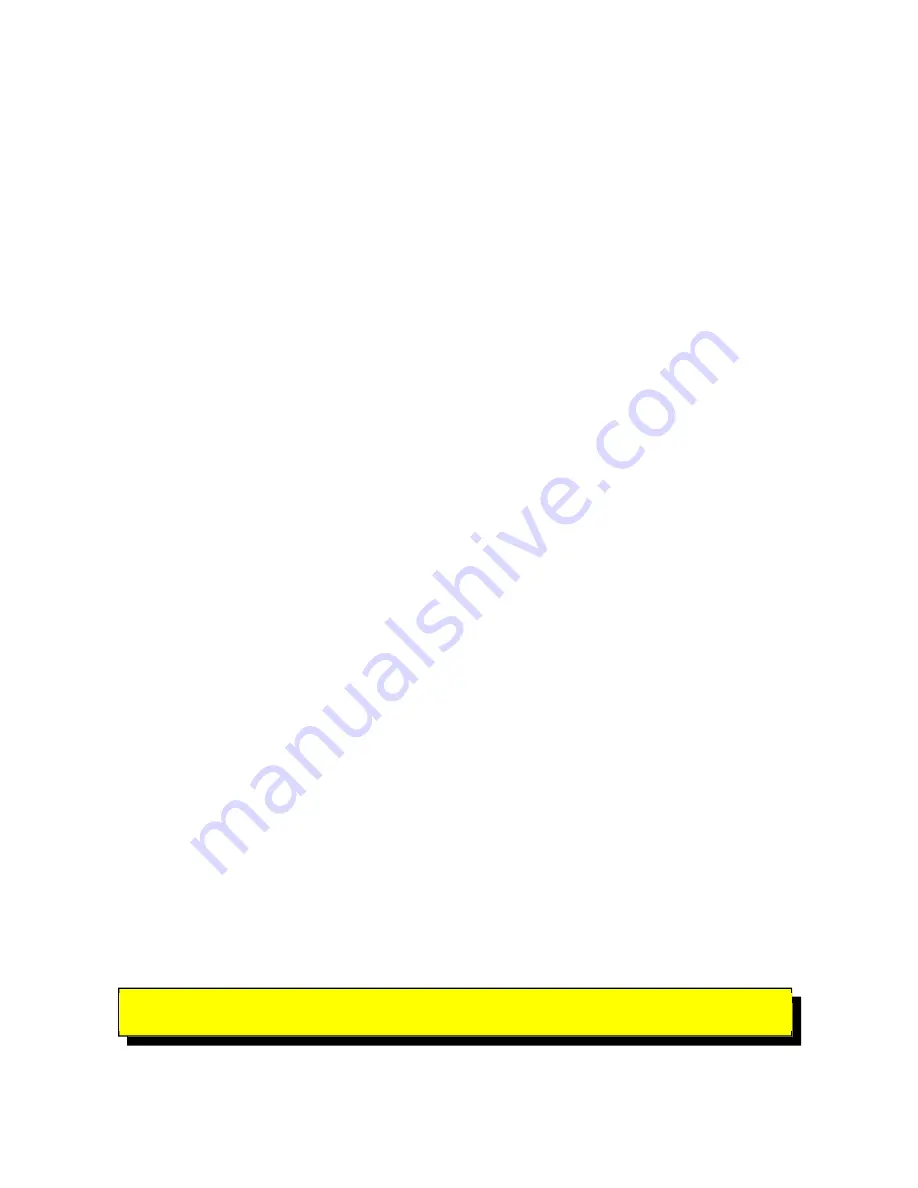
January 2019
Page 11
Body Harness
Harnesses must comply with the latest edition of ANSI A10.14.
Position a body harness D-ring in the center of the back rib cage.
Follow the safety equipment manufacturer’s instructions.
Lanyards
Lanyards must meet or exceed OSHA standards.
Lanyards must be 4 feet long (or less with double snap locks).
Minimum tensile strength is 5,000 lbs.
PLATFORMS
Follow the platform load specification.
Check stirrup bolts daily for soundness and tightness.
Use toeboards, handrails and mid-rails on all open sides.
Acids can destroy aluminum platforms. Replace platform immediately if exposed to acids or corrosive
materials.
Operate platform in level position only.
Work from deck of platform only. Do not stand on guardrails, toeboards, platform/work cage
supported objects or lean out from ends of the platform. Do not use ladders etc. to get at higher
elevations.
Do not bridge from one platform to another, nor to any structure or other equipment.
Do not horizontally transfer a work platform while it is suspended in the air. Perform all transfer
operations ONLY with the platform resting on a safe surface.
Bosun chairs should carry only the operator. Do not hang loads from the seat or attach any device or
support to seat or seat back.
WELDING
Use the following precautions when welding to prevent the possibility of electric shock
to personnel and/or the possibility of welding current passing through the wire rope.
Attach each wire rope to its suspension point with a suitable insulated thimble. Insulate extra rope
stored on the roof to prevent grounding, or terminate the suspension rope at the insulated thimble.
Cover the supporting wire rope with insulating material above and below the Sky Climber® Hoist.
Use a length of split rubber tube taped in place around the cable as follows:
Extend above the Sky Lock brake for 4 to 5 feet (more if required by local codes).
Extend below the Sky Climber® Hoist, far enough to insulate the tail line from the
platform. Guide and/or retain the portion of the tail line below the platform so that it
does not become grounded.
Cover each Sky Climber Hoist, Sky Lock Brake, and Wire Winder with protective covers
made from insulating material.
Connect a grounding conductor from the platform to the work piece. The size of this
conductor must be equal to or greater than the size of the stinger lead.
NOTE:
This must be a secondary conductor and must not be in series with the primary conductor
between the welder and the work piece.
Summary of Contents for Compact 1000
Page 22: ...January 2019 Page 22 GAST AIR MOTOR COMPACT SERIES HOISTS ...
Page 23: ...January 2019 Page 23 ...
Page 24: ...January 2019 Page 24 ...
Page 25: ...January 2019 Page 25 ...