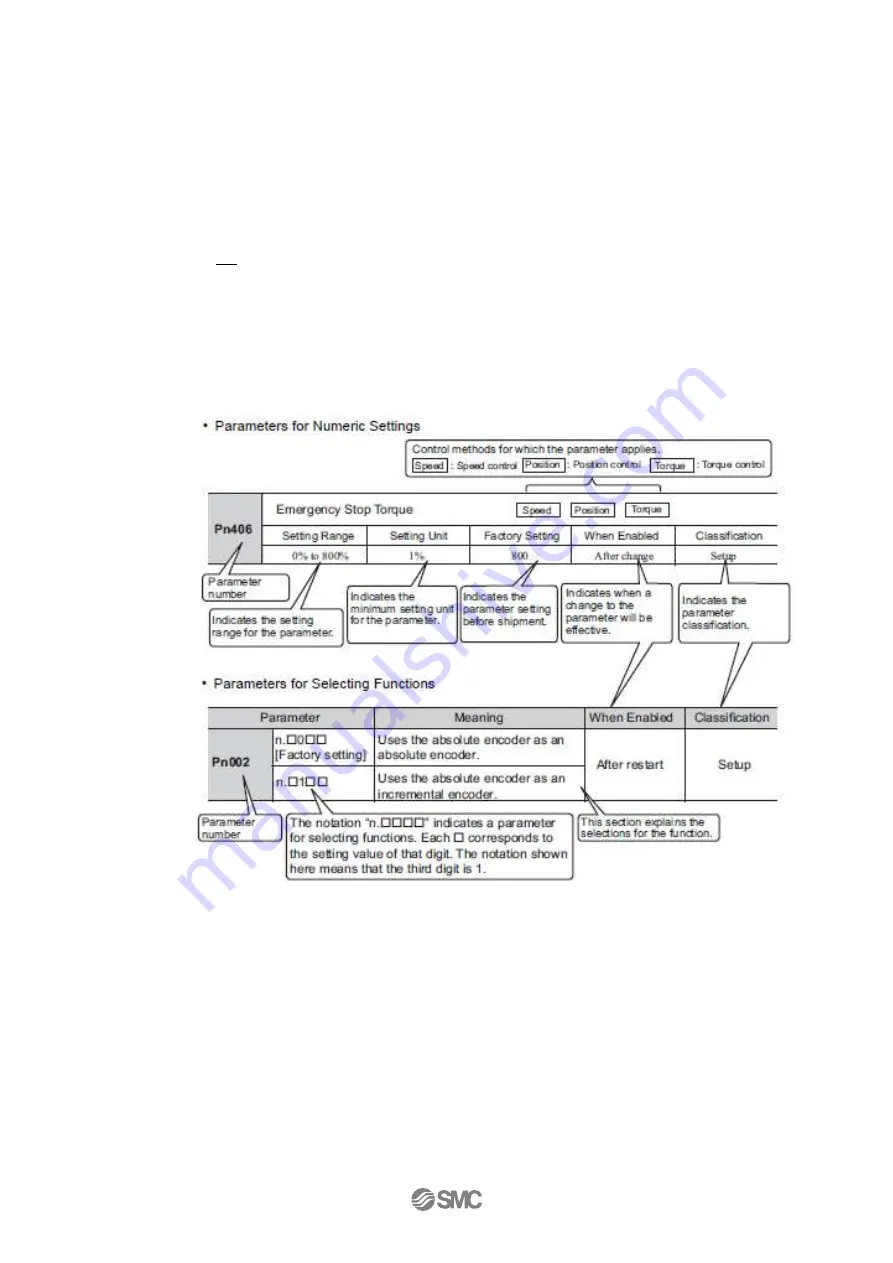
2
•
Notation Used in this Manual
•
Notation for Reverse Signals
The names of reverse signals (i.e., ones that are valid when low) are written with a
forward slash (/) before the signal name.
Notation Example
BK = /BK
•
Notation for Parameters
The notation depends on whether the parameter requires a value setting (parameter
for numeric settings) or requires the selection of a function (parameter for selecting
functions).
Summary of Contents for LECYU Series
Page 30: ...1 Outline 1 9 1 4 3 Three phase 200 V LECYU2 V9 Models ...
Page 65: ...3 Wiring and Connection 3 11 3 Wiring Example with DC Power Supply Input DRIVER ...
Page 92: ...3 Wiring and Connection 3 38 External Dimensions Units mm 1 FN Type by Schaffner EMC Inc ...
Page 93: ...3 Wiring and Connection 3 39 2 FN Type ...
Page 143: ...4 Operation 4 44 ...