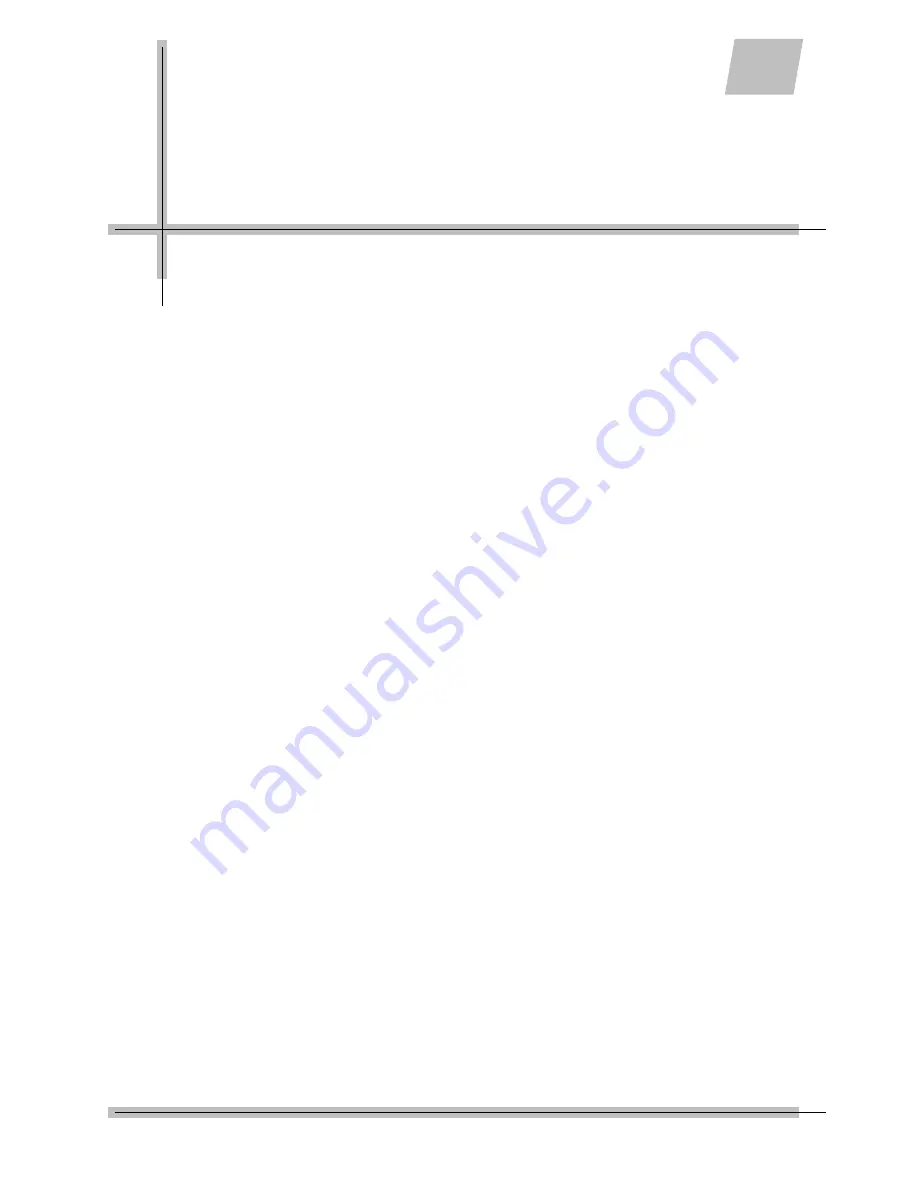
3-1
M
Maaiinntteennaannccee
3
Use this chapter to maintain
D
Duuaall
33441122
:
• Master filter,
• Pump, and
• When stored for prolonged periods.
Troubleshooting information and a list of parts and accessories
are also included.
Equipment Tips
p
A stable scale weight reading, with the refrigerant not moving
around in the recovery tank, is needed at the beginning and
end of a recycle or charge program. Do not lean on or move
the unit at these times.
p
Never attempt to change the recovery tank during unit
operation.
p
Always evacuate service hoses before disconnecting from
D
Duuaall
33441122
or manifold gauge set. For additional information
refer to
Chapter 2Evacuating Service Hoses.
p
Never drop a recovery tank onto scale. This may damage
scale assembly.
p
Always oil seals before connection to any tank, filter or fitting.
A leaky connection or no-flow condition may result if
connection is assembled dry.
p
Always close all tank valves–clockwise–on both recovery
tanks when
D
Duuaall
33441122
is not in use.
p
Non-condensable gasses must be purged from the recovery
tank. For additional information refer to
Chapter 2Purging
Non-condensable Gas
.
Summary of Contents for Dual 3412
Page 2: ...ii T Ta ab bl le e o of f C Co on nt te en nt ts s ...
Page 8: ...viii U Us si in ng g t th hi is s M Ma an nu ua al l ...
Page 14: ...VI S Sa af fe et ty y I In nf fo or rm ma at ti io on n ...
Page 26: ...1 12 I In nt tr ro od du uc ct ti io on n ...