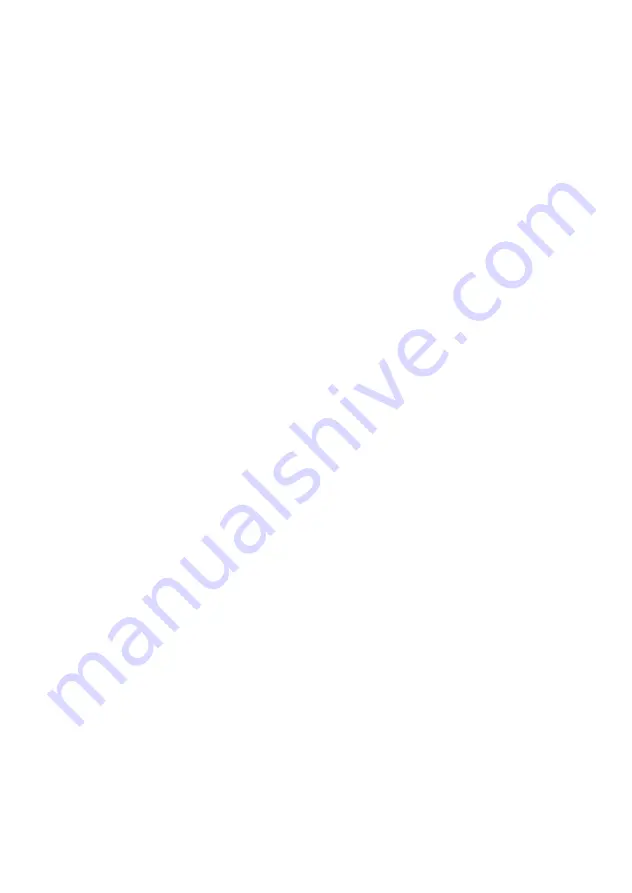
91
Warranty, the purchase invoice of the same or another document demonstrating its
acquisition. In any case, the document proving the acquisition of the Product must
contain the identification of the Product (as mentioned in point 2 above) and its
date of acquisition. Alternatively, and in order to validate the Product Warranty, the
PSR - document certifying the commissioning of the machine (when applicable)).
3.9
The Product will have to be installed by a qualified professional for the
purpose, in accordance with the regulations in force in each geographical area, for
the installation of these Products and complying with all the regulations in force,
especially regarding chimneys, as well as other applicable regulations for aspects
such as water supply, electricity and / or other related to the equipment or sector
and as described in the instruction manual.
A product installation that does not conform to the manufacturer's specifications
and / or does not comply with the legal regulations on this subject will not give rise
to the application of this Warranty. Whenever a product is installed outdoors, it
must be protected against weather effects such as rain and wind. In these cases, it
may be necessary to protect the appliance by means of a cabinet, or a properly
ventilated protective case Appliances should not be installed in places that contain
chemicals in their atmosphere, in saline or high humidity environments, as mixing
them with air may produce rapid corrosion in the combustion chamber. In this type
of environment, it is especially recommended that the appliance be protected with
anti-corrosion products for this purpose, especially during times of operation. As a
suggestion it is indicated the application of graphite greases indicated for high
temperatures with function of lubrication and anti-corrosion protection. 3.10
In
equipment belonging to the pellet family, in addition to the daily and weekly
maintenance contained in the instruction manual, it is also obligatory to carry out
the cleaning inside and in the respective chimney for the evacuation of fumes.
These tasks should be carried out every 600-800 kg of pellets consumed, in the
case of stoves (air and water) and compact boilers, and every 2000-3000 kg of
pellets consumed in the case of automatic boilers. In the event that these
quantities are not consumed, at least one systematic preventive maintenance must
be carried out annually.
3.11
It is the Buyer's responsibility to ensure that periodic maintenance is
carried out, as indicated in the instruction and handling manuals accompanying the
Summary of Contents for Atlantic
Page 77: ...76 ...
Page 78: ...77 ...
Page 79: ...78 ...
Page 85: ...84 20 Electrical Diagram of the Fire Unit Figure 68 Electrical diagram ...
Page 100: ...99 25 2 Flow chart Flow chart 1 Lighting ...
Page 101: ...100 ...
Page 102: ...101 Flow chart 2 Disabling Note The circulator pump off below 40 C water temperature ...