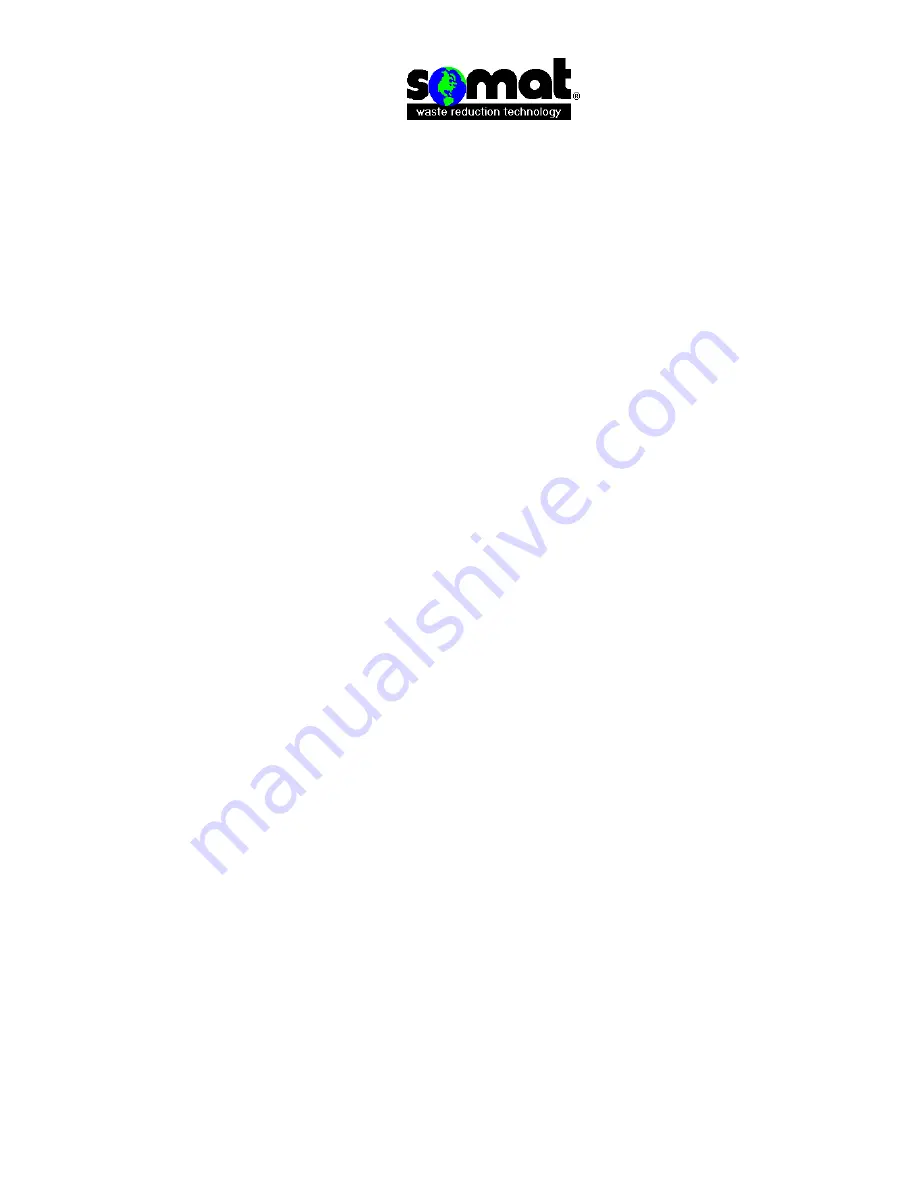
SOMAT COMPANY
LIMITED WARRANTY
SOMAT COMPANY warrants each new product manufactured by it to be free from defects in
material and workmanship under normal use and service, which does not include normal wear
of parts, ("normal use and service", with respect to Pulpers, Presses, water Hydra-Extractors,
Waste Handling and Processing Systems, shall mean the handling only of waste items of the
types listed in the SOMAT
®
Quotation or Sales Order therefore and within the
LIMITATIONS
THEREIN
set forth), its obligation under this warranty being limited to repairing or replacing any
part or parts thereof, free of charge
INCLUSIVE
of labor to remove and replace, f.o.b. factory from
which shipped, which shall, within one year from initial start-up of the SOMAT
®
System or from
date of original installation of the product if not a system be returned to SOMAT
®
at the factory
from which shipped, with transportation charges prepaid, and which SOMAT's examination shall
disclose to its satisfaction to have been thus defective. This warranty shall not apply to any
product or part which shall have been repaired or altered by any person not employed or
retained by SOMAT
®
, so as in the judgment of SOMAT
®
to affect its operation and reliability, nor
which has been installed, operated, or maintained contrary to SOMAT
®
OPERATION or
PREVENTIVE MAINTENANCE INSTRUCTION MANUALS or to other written instructions or
drawings approved by SOMAT
®
, nor which has been subject to misuse, negligence, or accident.
This warranty shall not apply should the SOMAT
®
System be initially started up without a duly
authorized SOMAT
®
representative present.
EXCEPT AS HEREIN EXPRESSLY STATED, NO WARRANTY, EXPRESS, IMPLIED OR BY LAW,
(INCLUDING BUT NOT LIMITED TO ANY IMPLIED WARRANTY OF MERCHANTABILITY OR
FITNESS FOR A PARTICULAR PURPOSE), IS MADE BY SOMAT; AND IN ANY EVENT SOMAT’S
LIABILITY, WHETHER IN CONTRACT, TORT, STRICT LIABILITY, OR UNDER ANY WARRANTY, OR
OTHERWISE, SHALL NOT EXCEED THE PURCHASE PRICE RECEIVED BY IT AND SHALL IN NO
EVENT INCLUDE ANY CONSEQUENTIAL, INCIDENTAL, PUNITIVE OR OTHER SPECIAL
DAMAGES.
NO CHANGE IN THIS WARRANTY AND LIMITATION OF LIABILITY AND NO SUBSTITUTE
THEREFORE (WHETHER INCORPORATED IN A PURCHASE ORDER OR OTHERWISE) SHALL BE
EFFECTIVE UNLESS SPECIFICALLY SET FORTH IN A WRITTEN INSTRUMENT SIGNED BY AN
OFFICER OF SOMAT
®
.
Rev. 02/10
Summary of Contents for SPC-75S
Page 12: ...Installation ...
Page 16: ...MOUNTING DETAIL OF TROUGH ...
Page 21: ...FOR REFERENCE ONLY ...
Page 22: ...Start Up ...
Page 26: ...Operation ...
Page 32: ...CLEANING YOUR SYSTEM ...
Page 38: ...MAINTENANCE ...
Page 49: ...TROUBLESHOOTING ...
Page 56: ...REPLACEMENT PARTS EXPLODED VIEWS ...
Page 57: ......
Page 60: ......
Page 62: ......