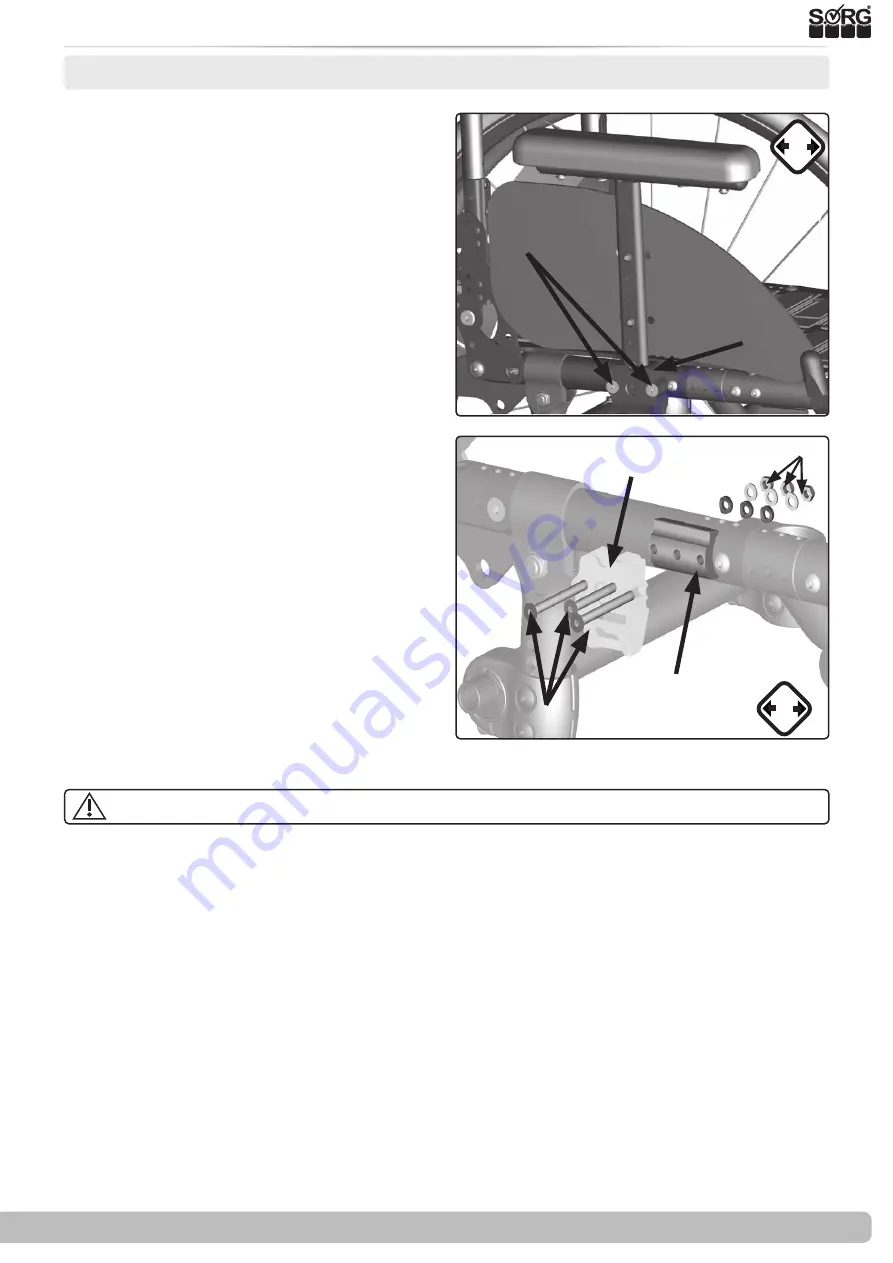
service record Airon
15 von 36
2021-06-10
Plug-in side panel
(4)
(5)
(B)
(B)
(D)
Remove the drive wheels. Now remove the
mounting of the plug-in side part
(4A)
by loo-
sening the screws
(4B)
.
Attach the widening
(5A)
to the frame and fas-
ten it with the screws
(5B)
, the mount for the
plug-in side part
(5C)
and the nuts including
washers and saddle washers
(5D)
.
Do the same on both sides.
Insert the side panels again.
(A)
(A)
(C)
Now also adjust the new position of the drive
wheels (see 3.1.6.) In order to mount the drive
wheels further outwards.
Reinstall the drive wheels.
Be sure to check the functionality of the knee lever brake and the wheels.
2x
2x
2x
2x