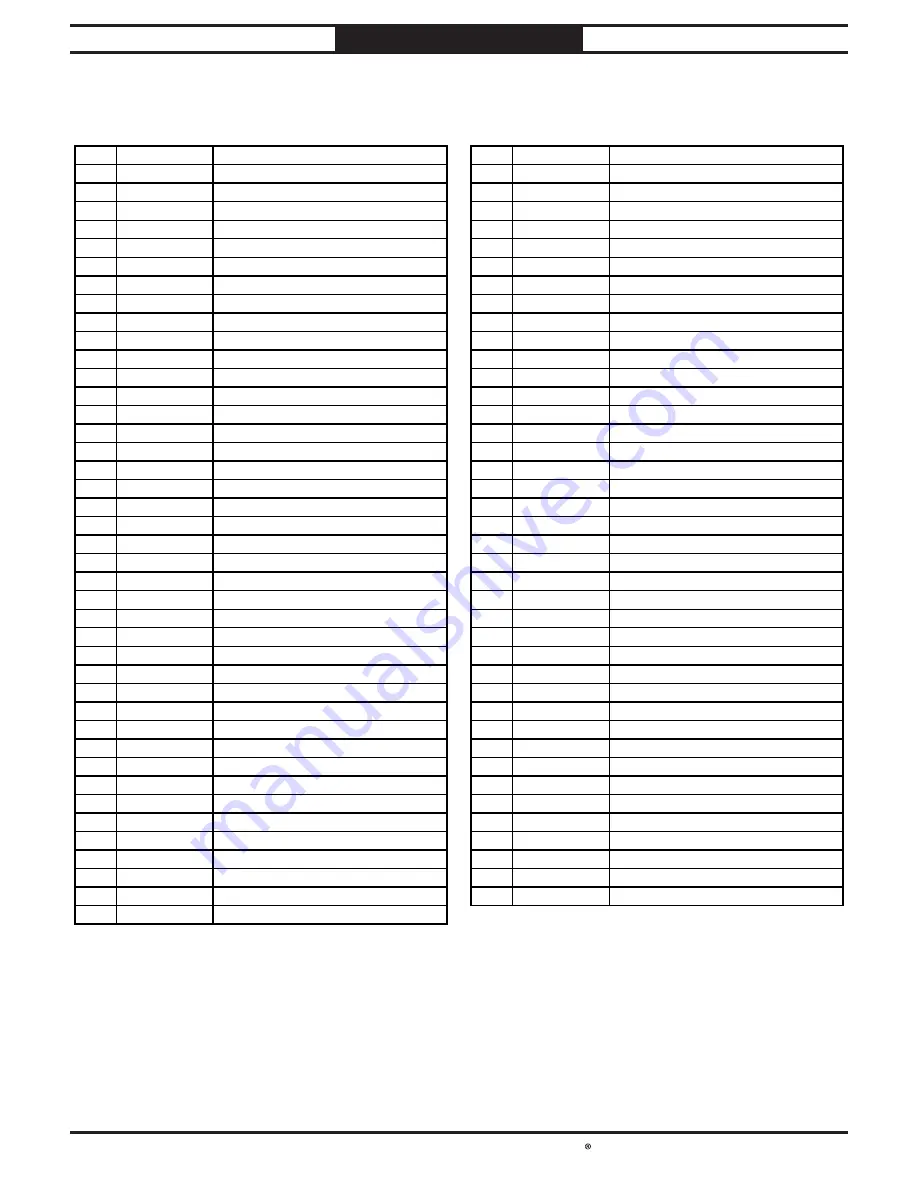
South Bend Tools
For Machines Mfd. Since 12/21
Model SB1102
-49-
P A R T S
Stand & Motor Parts List
REF PART #
DESCRIPTION
REF PART #
DESCRIPTION
4
PSB1102004
SIDE PANEL (LEFT)
221
PSB1102221
LOCK NUT M4-.7
5
PSB1102005
SIDE PANEL (RIGHT)
227
PSB1102227
FLANGE SCREW 8-32 X 3/8
6
PSB1102006
DRIVE SPROCKET 10T
230
PSB1102230
LATCH
7
PSB1102007
IDLER SPROCKET 10T
231
PSB1102231
TAP SCREW #8 X 3/8
8
PSB1102008
TABLE LEADSCREW 3/4-16
235
PSB1102235
DUST SCOOP
9
PSB1102009
ELEVATION CHAIN
236
PSB1102236
HEX BOLT 1/4-20 X 3/4
13
PSB1102013
DUST PORT 4" (FLAT BASE)
237
PSB1102237
HEX NUT 1/4-20
14
PSB1102014
DUST HOOD
238
PSB1102238
PRIMARY TABLE LEADSCREW 3/4-16
15
PSB1102015
DUST PORT 4" (CURVED BASE)
239
PSB1102239
GEAR 25T
16
PSB1102016
FRONT PANEL
240
PSB1102240
KEY 5 X 5 X 10
18
PSB1102018
MOTOR PULLEY
241
PSB1102241
LOCK NUT 1/2-13
19
PSB1102019
KEY 5 X 5 X 25 RE
244
PSB1102244
BEARING SEAT (UPPER)
20
PSB1102020
MOTOR 5HP 220V 1-PH
245
PSB1102245
LOCK WASHER 5MM
20-1
PSB1102020-1
FAN COVER
246
PSB1102246
NEEDLE BEARING TLA-810
20-2 PSB1102020-2 MOTOR FAN
247
PSB1102247
BEARING SEAT (LOWER)
20-3 PSB1102020-3 CAPACITOR COVER
248
PSB1102248
PHLP HD SCR 10-24 X 1/2
20-4 PSB1102020-4 S CAPACITOR 300M 250V 1-3/4 X 3-1/2
249
PSB1102249
FLAT WASHER #10
20-5 PSB1102020-5 R CAPACITOR 60M 300V 1-3/4 X 3-1/2
250
PSB1102250
BALL BEARING 698ZZ
20-6 PSB1102020-6 MOTOR JUNCTION BOX
251
PSB1102251
HEX BOLT 1/4-20 X 3/4
20-7 PSB1102020-7 CONTACT TYPE-1, 27 X 70, CPT 7MM
259
PSB1102259
FLAT WASHER 3/8
20-8 PSB1102020-8 CENTRIFUGAL SWITCH
260
PSB1102260
FLAT WASHER 5/16
20-9 PSB1102020-9 BALL BEARING 6205ZZ (FRONT)
261
PSB1102261
HEX NUT 3/8-16
20-10 PSB1102020-10 BALL BEARING 6203ZZ (REAR)
262
PSB1102262
HEX NUT 5/16-18
21
PSB1102021
IDLER SPROCKET SHAFT
264
PSB1102264
FLAT WASHER #8
145
PSB1102145
HEX BOLT 1/4-20 X 3/8
265
PSB1102265
FLAT WASHER 1/2
146
PSB1102146
FLAT WASHER 1/4
269
PSB1102269
REAR PANEL
201
PSB1102201
HEX BOLT 3/8-16 X 1
270
PSB1102270
SIDE BRACKET
202
PSB1102202
HEX NUT 3/8-16
271
PSB1102271
TAP SCREW #8 X 3/8
203
PSB1102203
MOTOR BRACKET
272
PSB1102272
TAP SCREW #8 X 1/2
204
PSB1102204
HEX BOLT 3/8-16 X 1
283
PSB1102283
ADHESIVE FOAM STRIP
205
PSB1102205
FLAT WASHER 3/8
293
PSB1102293
FRONT BRACE
206
PSB1102206
HEX NUT 3/8-16
294
PSB1102294
REAR BRACE
208
PSB1102208
SET SCREW 1/4-20 X 1/2
296
PSB1102296
HANDLE
210
PSB1102210
HEX BOLT M8-1.25 X 24
297
PSB1102297
FRAME
211
PSB1102211
FENDER WASHER 3/8
298
PSB1102298
PHLP HD SCR M6-1 X 8
214
PSB1102214
HOOD SUPPORT ARM RIGHT
299
PSB1102299
HEX NUT M6-1
215
PSB1102215
HOOD SUPPORT ARM LEFT
319
PSB1102319
HEX BOLT 3/8-16 X 2
216
PSB1102216
PHLP HD SCR M4-.7 X 6
320
PSB1102320
FLAT WASHER 3/8
217
PSB1102217
TAP SCREW #8 X 3/8
354
PSB1102354
HEX WRENCH 3MM
218
PSB1102218
HEX NUT M4-.7
355
PSB1102355
HEX WRENCH 5MM
219
PSB1102219
HINGE
356
PSB1102356
PLASTIC P-CLIP 1"
220
PSB1102220
PHLP HD SCR M4-.7 X 10