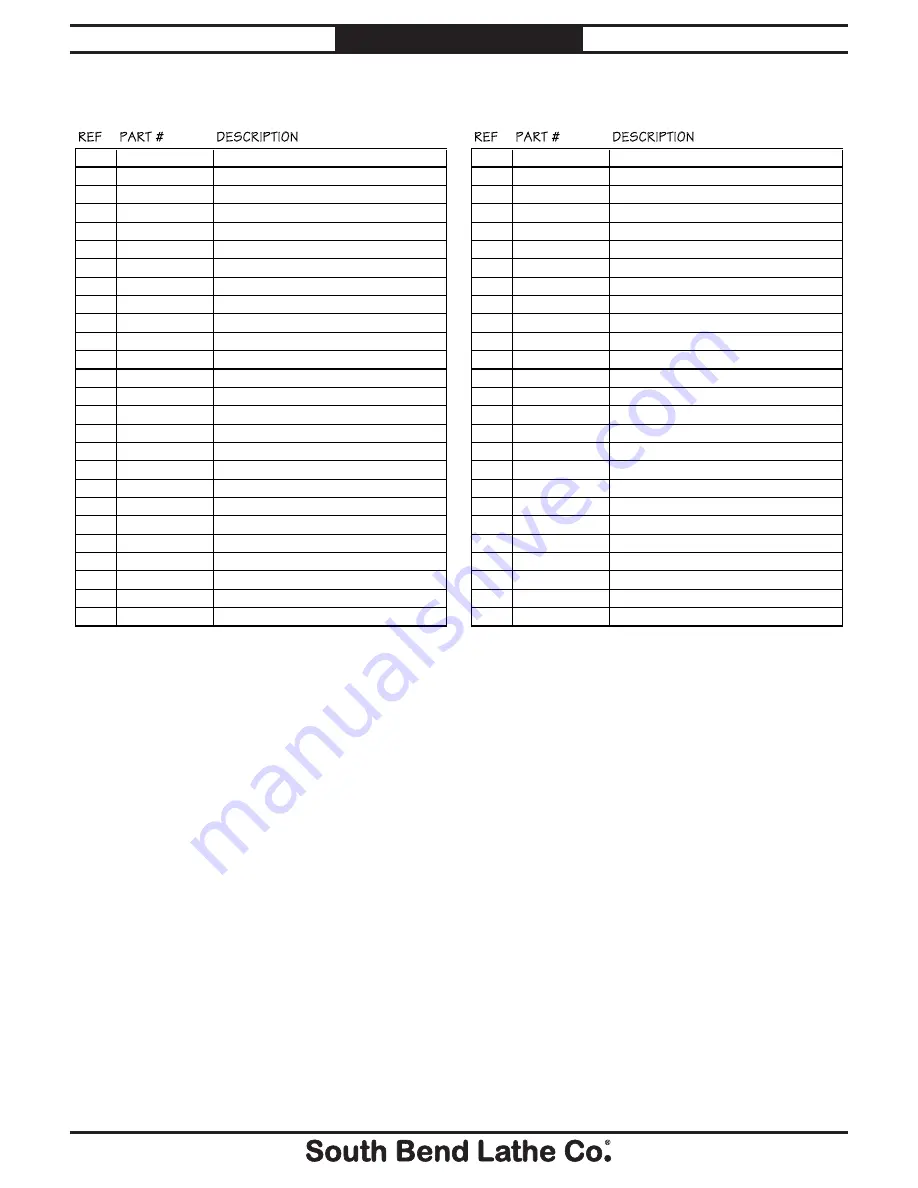
For Machines Mfg. Since 8/09
Model SB1037/SB1038 Parts
-31-
P A R T S
Tailstock Parts List
REF PART #
DESCRIPTION
REF PART #
DESCRIPTION
1801
PSB10121801
INCH TAILSTOCK LEADSCREW
1828 PSB10121828
TAILSTOCK ALIGNMENT PIN
1802 PSB10121802
INCH LEADSCREW NUT
1829 PSB10121829
PIVOT BLOCK
1803 PK34M
KEY 5 X 5 X 20
1830 PSB10141830
DOG POINT SET SCREW
1804 PSB10121804
THRUST BEARING MTB/AS2-2035
1831
PSB10121831
TAILSTOCK BASE
1805 PSB10121805
INCH LEADSCREW FLANGE BRACKET
1832 PSB10121832
GIB ADJUSTMENT SCREW
1806 PR37M
EXT RETAINING RING 32MM
1833 PSB10121833
BEDWAY WIPER
1807 PSB10121807
INDEX DIAL SPACER
1834 PSB10121834
BEDWAY WIPER PLATE
1808 PSB10121808
INCH INDEX RING
1837 PSB10121837
TAILSTOCK GIB
1809 PSB10121809
HANDWHEEL
1838 PSB10121838
COMPRESSION SPRING 25 X 45
1810
PSB10121810
HANDWHEEL WASHER 6MM
1839 PSB10121839
CLAMP BLOCK
1811
PSB10121811
HANDLE BOLT M8-1.25 X 90
1840 PSB10121840
TAILSTOCK STUD M14-2 X 110
1812
PSB10121812
HANDWHEEL HANDLE
1901
PCAP01M
CAP SCREW M6-1 X 16
1813
PSB10120515
COMPRESSION SPRING 6 X 16
1902 PSS04M
SET SCREW M6-1 X 12
1814
PSTB001
STEEL BALL 1/4
1903 PCAP26M
CAP SCREW M6-1 X 12
1815
PSB10121815
QUILL LOCK LEVER
1904 PCAP128M
CAP SCREW M8-1.25 X 70
1816
PSB10121816
QUILL LOCK CAM SHAFT
1905 PCAP35M
CAP SCREW M8-1.25 X 60
1817
PSB10121817
TAILSTOCK LOCK LEVER
1906 PCAP68M
CAP SCREW M6-1 X 8
1818
PSB10121818
TAILSTOCK LOCK CAM SHAFT
1907 PCAP01M
CAP SCREW M6-1 X 16
1819
PRP04M
ROLL PIN 4 X 24
1908 PS08M
PHLP HD SCR M5-.8 X 12
1821
PSB10121821
OIL SEAL DH53
1909 PW04M
FLAT WASHER 10MM
1822 PLUBE001
TAP-IN BALL OILER 1/4
1910
PB144M
HEX BOLT M10-1.5 X 55
1823 PSB10141823
TAILSTOCK CASTING
1911
PW10M
FLAT WASHER 14MM
1824 PSB10121824
TAILSTOCK QUILL
1912
PN32M
HEX NUT M14-2
1825 PSB10121825
QUILL GUIDE KEY
1913
PN03M
HEX NUT M8-1.25
1826 PSB10121826
TOP OFFSET INDEX PLATE
1914
PRIV001M
STEEL FLUTED RIVET 2 X 5MM
1827 PSB10121827
BOTTOM OFFSET INDEX PLATE
1915
PLW06M
LOCK WASHER 10MM