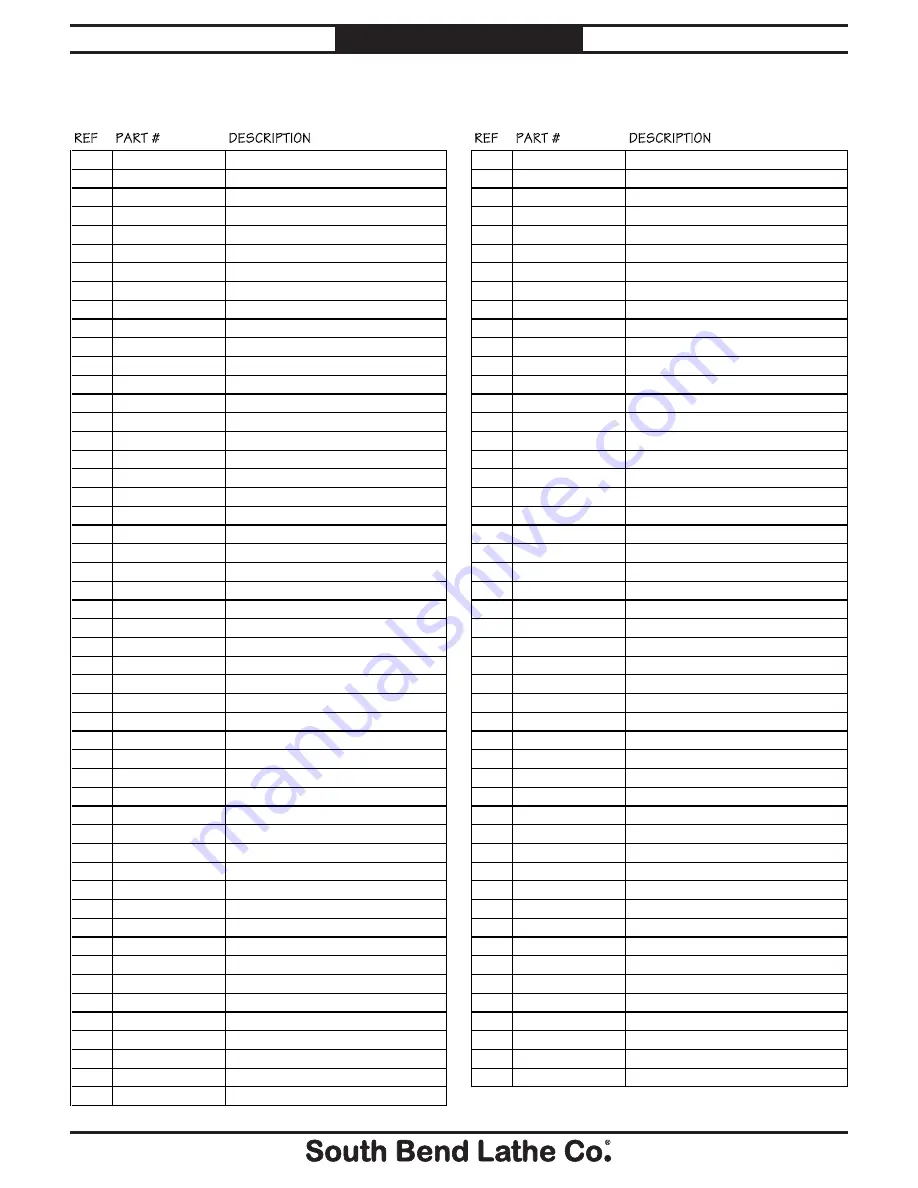
For Machines Mfg. Since 3/11
Turn-Nado
®
Gearhead Lathes
-109-
P A R T S
Gearbox Parts List
REF PART #
DESCRIPTION
REF PART #
DESCRIPTION
301
PSB1046PF0301
SPLINED SHAFT
352
PSB1046PF0352
SHAFT NUT
302
PK109M
KEY 7 X 7 X 35
353
PSS02M
SET SCREW M6-1 X 6
303
PSB1046PF0303
SHAFT SPACER
354
PR10M
EXT RETAINING RING 22MM
304
PSB1046PF0304
OIL SEAL 253708
355
PSB1046PF0355
COMBO GEAR 45T/18T
305
PSB1046PF0305
NEEDLE BEARING
356
PSB1046PF0356
GEAR 22T
306
PCAP01M
CAP SCREW M6-1 X 16
357
PSB1046PF0357
GEAR 22T
307
PSB1046PF0307
SPLINED SHAFT SEAT
358
PSB1046PF0358
GEAR 33T
308
PSB1046PF0308
SPACER
359
PSB1046PF0359
GEAR 22T
309
PR11M
EXT RETAINING RING 25MM
360
PSB1046PF0360
SPACER
310
PSB1046PF0310
GEAR 19T/19T
361
PSB1046PF0361
GEAR 36T
311
PSB1046PF0311
SPLINED SHAFT
362
PSB1046PF0362
SHAFT SEAT
312
PSB1046PF0312
SHAFT COVER
363
PSB1046PF0363
OIL SEAL 304005
313
PSB1046PF0313
COVER GASKET
364
PSB1046PF0364
SPACER
314
P6005-OPEN
BALL BEARING 6005 OPEN
365
PSB1046PF0365
SPLINED SHAFT
315
PSB1046PF0315
SPACER
366
PSB1046PF0366
SHAFT SEAT
316
PSB1046PF0316
GEAR 20T/30T
367
PSB1046PF0367
SPACER
317
PSB1046PF0317
SPACER
368
PSB1046PF0368
SHAFT
318
PR15M
EXT RETAINING RING 30MM
369
PSB1046PF0369
PIN 6 X 36
319
PSB1046PF0319
SPLINED SHAFT
370
P6003-OPEN
BALL BEARING 6003 OPEN
320
PSB1046PF0320
GEAR 22T
371
PR18M
EXT RETAINING RING 17MM
321
PSB1046PF0321
SHAFT SPACER
372
PSB1046PF0372
BEARING SEAT
322
PSB1046PF0322
SPLINED SHAFT
373
PLW03M
LOCK WASHER 6MM
323
PSB1046PF0323
GEARBOX CASTING
374
PSB1046PF0374
PLATE
324
PSB1046PF0324
SPACER
375
PSB1046PF0375
REVERSE STOP PLATE
325
PSB1046PF0325
GEAR 32T
376
PSB1046PF0376
UPPER/LOWER PLATE
326
PSB1046PF0326
GEAR 23T
377
PSTB001
STEEL BALL 1/4
327
PSB1046PF0327
GEAR 16T
378
PSB1046PF0378
COMPRESSION SPRING
328
PSB1046PF0328
SPACER
380
PRP24M
ROLL PIN 5 X 16
329
PR25M
INT RETAINING RING 47MM
381
PSB1046PF0381
BOTTOM SHIFT FORK SUPPORT
330
P6204-OPEN
BALL BEARING 6204-OPEN
382
PRP24M
ROLL PIN 5 X 16
331
PSB1046PF0331
SPACER
383
PSB1046PF0383
BOTTOM SHIFT FORK
332
PSB1046PF0332
SHAFT CLUTCH
384
PCAP15M
CAP SCREW M5-.8 X 20
333
PR09M
EXT RETAINING RING 20MM
385
PSB1046PF0385
PARTITION
334
PSB1046PF0334
COMBO GEAR 35T/35T
386
PSB1046PF0386
LOWER-MID SHIFT FORK SUPPORT
335
PSB1046PF0335
SPACER
387
PSB1046PF0387
LOWER-MID SHIFT FORK
336
PSB1046PF0336
GEAR 22T
388
PSB1046PF0388
UPPER-MID SHIFT FORK SUPPORT
337
PSB1046PF0337
GEAR 16T
389
PSB1046PF0389
UPPER-MID SHIFT FORK
338
PSB1046PF0338
GEAR 20T
390
PSB1046PF0390
TOP SHIFT FORK SUPPORT
339
PSB1046PF0339
SPACER
391
PSB1046PF0391
TOP SHIFT FORK
340
PSB1046PF0340
GEAR 24T
392
PSB1046PF0392
SPACER
341
PSB1046PF0341
SPACER
393
PSB1046PF0393
PARTITION NUT
342
PSB1046PF0342
GEAR 23T
394
PSB1046PF0394
PARTITION PLATE
343
PSB1046PF0343
SPACER
395
PSB1046PF0395
GEARBOX GASKET
344
PSB1046PF0344
GEAR 27T
396
PSB1046PF0396
SHIFT GATE
345
PSB1046PF0345
SPACER
397
PSB1046PF0397
SELECTOR LEVER RETAINER
346
PSB1046PF0346
GEAR 24T
398
PORG035
O-RING 3.1 X 34.4 G35
347
PSB1046PF0347
SPACER
399
PSB1046PF0399
SELECTOR LEVER
348
PSB1046PF0348
GEAR 28T
400
PSB1046PF0400
COMPRESSION SPRING
349
PSB1046PF0349
SPACER
401
PORG040
O-RING 39.4 X 3.1 G40
350
PSB1046PF0350
GEAR 26T
402
PSB1046PF0402
SELECTOR LEVER BASE
351
PSB1046PF0351
GEAR 32T
Summary of Contents for TURN-NADO SB10146PF
Page 138: ......