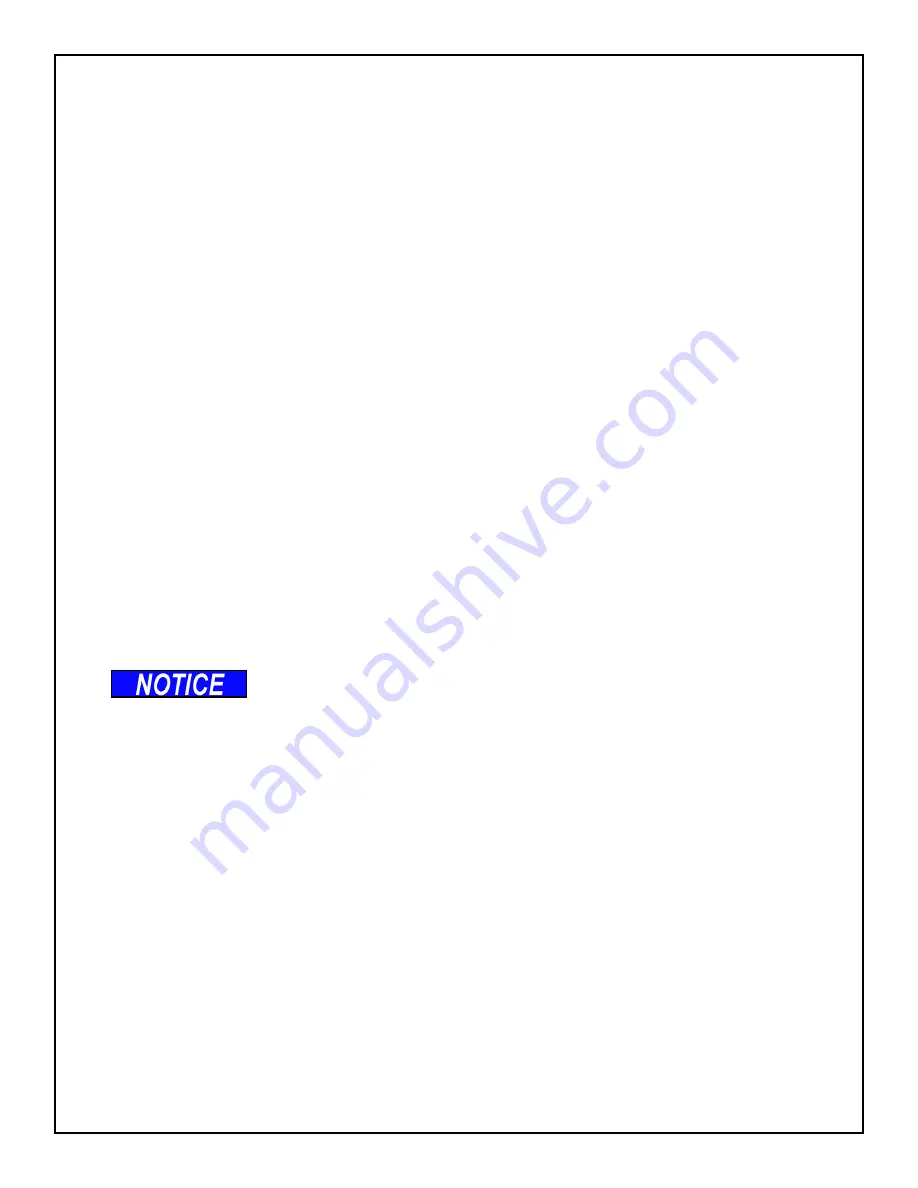
Southworth Products
PUN Manual
PUN Manual
25
9.
Hydraulic System Information
9.1 Hydraulic Power Unit
HYDRAULIC POWER UNIT SPECIFICATIONS
MOTOR
: Baldor: 5HP, 1750 RPM 208/230 - 460V / 3 / 60, 184TC wired for 460.
PUMP
: Parker gear pump: 0.61 CUIN / Rev with pump adapter and flex coupling for
1750 PSI operation.
RESERVOIR: 15 gallon with suction strainer, return filter and drip pan.
VALVE MANIFOLD
: Parker 2-station parallel manifold with system relief valve, dual
counter balance valves and pump unloading valve.
PRESS GAUGE: 0 - 2,000 PSI
RECOMMENDED FLUID
: If the lift will be used at normal ambient temperatures, the
machine is supplied the unit with Conoco AW 32 oil. This may be replaced by any other
good quality oil with 150 SSU at 100° F and rust and oxidation inhibitors and anti-wear
properties. If the lift will be used at ambient temperatures below 0°F, use aircraft hydraulic
oil. Use Type 15 aircraft hydraulic oil.
The following are
equivalent to Conoco AW
32:
Debris in the hydraulic system can damage the hydraulic pump.
Make sure tank and lines are clear of debris before operating the
machine.
NOTES:
• Cleanliness of inside of hydraulic tank must be maintained at all times. Wipe inside of
tank clean of all loose debris, metal chips, dust and dirt. Inside of tank must be dry and
free of moisture before adding hydraulic oil.
• Fill tank to the proper level indicated on tank level / temperature gauge before operating
system. Be sure not to overfill and thoroughly clean any spills.
•
For long term storage make sure all exposed ports and fittings are capped or plugged.
Type
Manufacturer
DTE 24
EXXON/MOBIL
NUTO H32
EXXON/MOBIL
AMOCO AW32
CHEVRON (AMOCO CO.)
AW32
CITGO