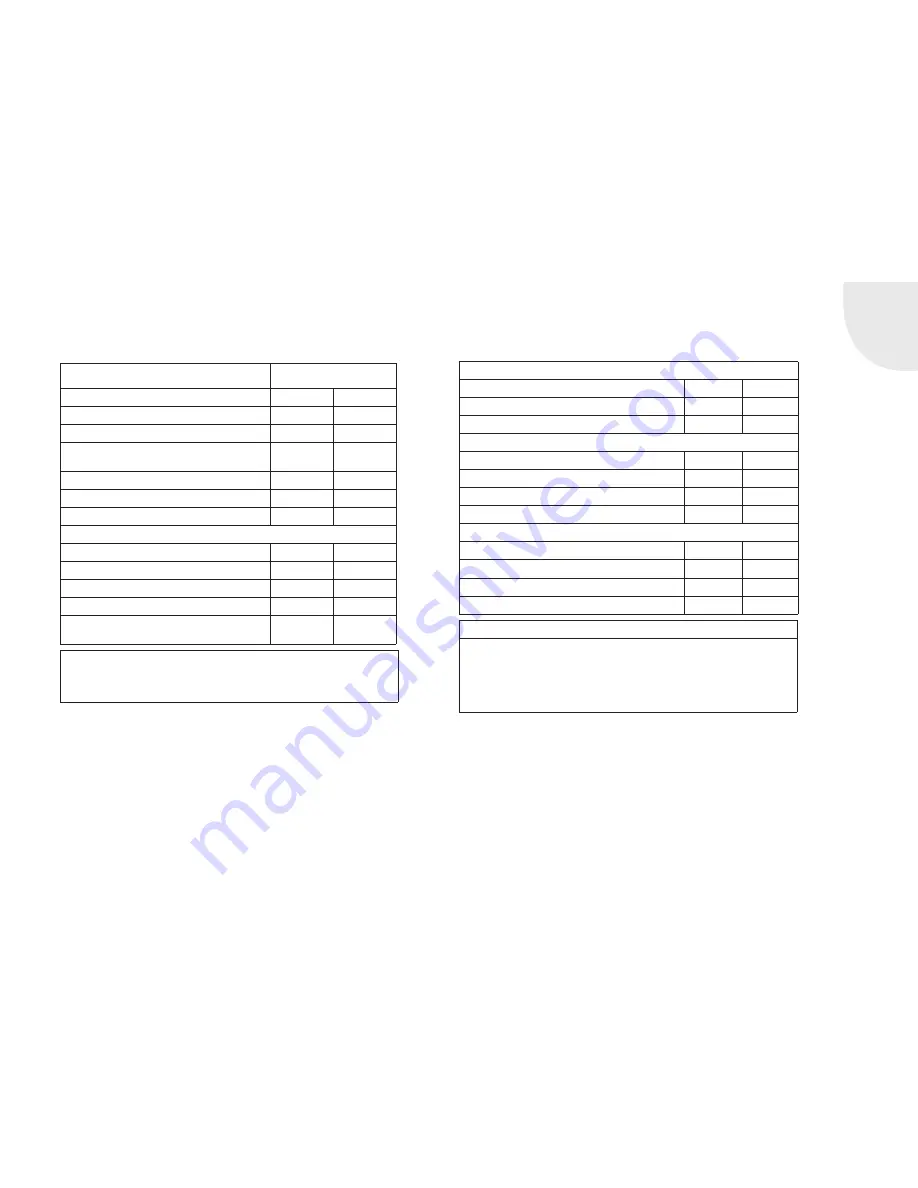
GB
GB
5
1.2 TECHNICAL DATA
Nova F
Weight (empty, without accessories)
190
kg
Nominal power with heat recovery section*
10
kW
Average heating gas temperature at the duct
355
°C
Average flue gas temperature downstream of the heat recovery
section
225
°C
Necessary min. delivery pressure**
12
Pa
Mass flow of flue gas
9,2
g/s
Wood feed quantity with nominal heat output/maximum
3,7
kg/70min
For other fill quantities:
Maximum possible feed quantity
8
kg/60min
Triplet values for 8 kg/60 min:
15
Pa
Average flue gas temperature at the duct
610
°C
Mass flow of flue gas
26
g/s
Average flue gas temperature at duct downstream of the heat
recovery section
395
°C
Between the triplet values after test (3.7 kg) and the max. fill quantity of 8 kg, interpolation is possible.
The draught length must be determined by the stove fitter based on the conditions, materials and
design. An estimate can be made using 50-80 K/m draught length.
This means that 610°C - 180°C = 430 K / 60 K = ~ 7 m
* The specified values represent the mean value over a combustion. These
values occur under test conditions with nominal heat output, if in 70 min
a quantity of approx. 2.7 kg of dry pieces of beech wood is burned and
the Spartherm metallic coasting temperature box (coasting temperature
unit) is installed.
** Pressure at the heating insert duct. Increased delivery pressures must be
reduced to less than 25 Pa through suitable measures, such as a draught
regulator or a damper.
Necessary minimum insulation thicknesses (Silca 250 KM)
Attachment wall (side / rear)
mm
100
Ceiling
mm
160
Setup floor (only under the metallic coasting temperature box
mm
20
Necessary minimum distances to heating chamber / components
Convection chamber (side / rear) to insert
mm
100
Insert to the setup floor
mm
140
Heat recovery section to the wall of the heating chamber
mm
100
Connecting line to the heating chamber ceiling
mm
200
Minimum distances in the radiation areas of the view pane
Flammable parts
mm
800
Flammable parts behind a radiation protection element
mm
400
Area of the non-flammable floor covering to the front
mm
500
Area of the non-flammable floor covering to the side
mm
300
Sheet metal radiation protection element
A sheet metal radiation protection element must be provided at the depth of the heating insert 1.0 m x
1.0 m 25 cm above the upper edge of the setup floor between the heating insert and the heating chamber
wall. Alternatively, the distance between the heating insert and heating chamber wall can be increased to
130 mm, and the insulation thickness can be increased to 120 mm. If the metallic coasting temperature
box (coasting temperature unit) is used, a sheet metal radiation protection element or insulation 20 mm
in thickness must be provided under the unit‘s base area.
The thicknesses of thermal insulation material are determined with open
air grates in the heating chamber, in accordance with DIN EN 13229. If a
closed heating chamber should be created, the thermal insulation material
thicknesses must be increased in the verification procedure. When using the
tested external firing unit, it must be fastened inside of other components
with suitable 100 mm fire protection insulation (see Material specification,
minimum insulation thicknesses).
Summary of Contents for Nova F
Page 1: ...GB Installation and Operating Manual Nova F...
Page 17: ...GB GB GB 17 NOTES...
Page 18: ...GB 18 NOTES...
Page 19: ...GB GB GB 19...