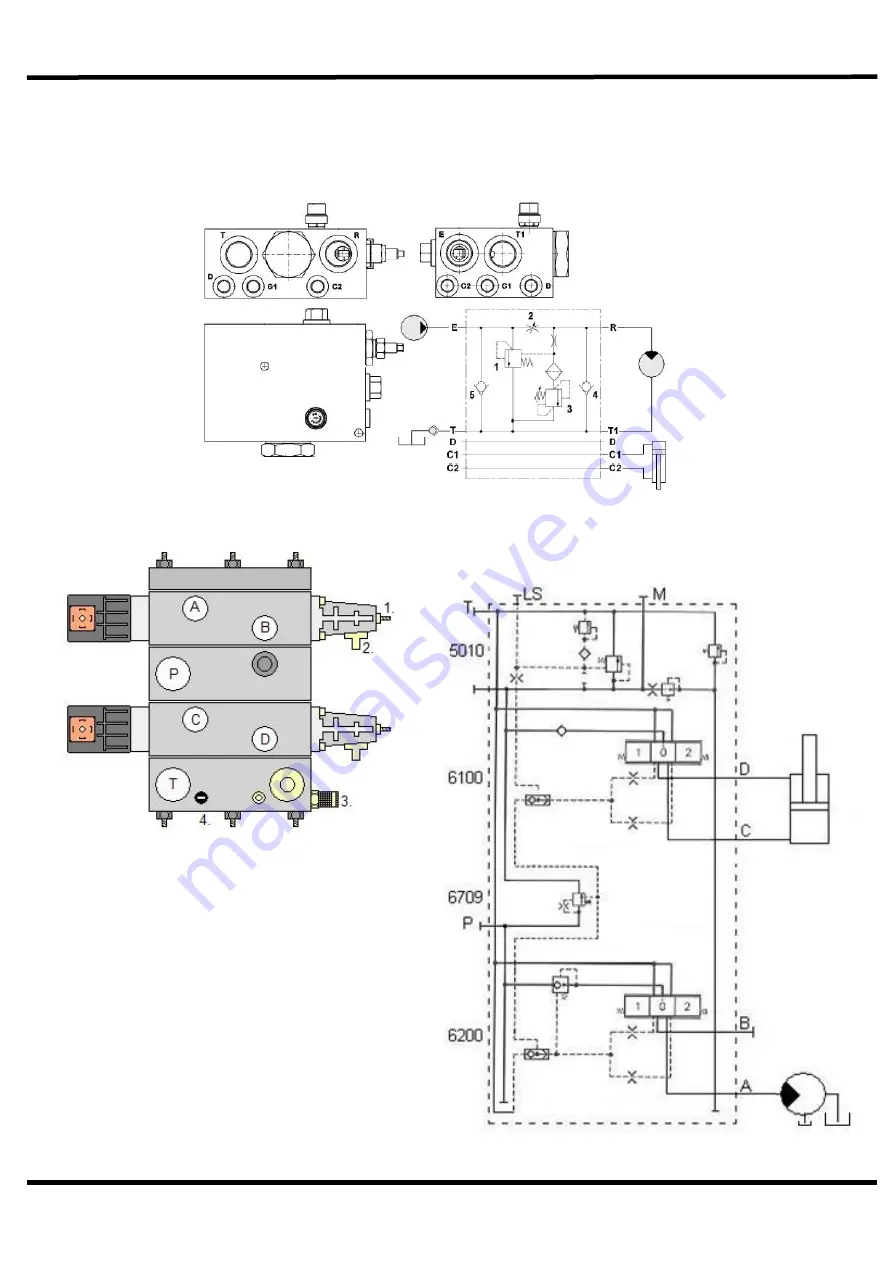
Spearhead RC
132/162
33
DIAGRAMS
Standard Splitter Valve:
Danfoss Splitter Valve Diagram:
1. Flow Adjustment
2. Manual Over-steering
3. Manometer Power Point (mini-mesh)
4. Safety Valve (200 bar)
A. Flow To Tool (regulated)
B. Not In Use
C. Cutting Angle
D. Cutting Angle
P. Pressure, Flow From Pump
T. Tank Connection, Depress
T From Engine
Summary of Contents for RC 132
Page 1: ...Spearhead RC 132 162 1 RC 132 162 ROTARY HEADS Edition 1 0 August 2017 Part No 8999108 ...
Page 34: ...Spearhead RC 132 162 34 Hydraulics Diagram RC 132 Hydraulic Diagram For Correct Fitting ...
Page 56: ...Spearhead RC 132 162 56 MAIN FRAME OVERVIEW RC 132 ...
Page 58: ...Spearhead RC 132 162 58 MAIN FRAME OVERVIEW RC 162 ...
Page 60: ...Spearhead RC 132 162 60 ROTOR OUTER 2 pcs ON MACHINE RC 132 ...
Page 62: ...Spearhead RC 132 162 62 ROTOR OUTER 2 pcs ON MACHINE RC 162 ...
Page 64: ...Spearhead RC 132 162 64 ROTOR CENTRE 1 pcs ON MACHINE RC 132 ...
Page 66: ...Spearhead RC 132 162 66 ROTOR CENTRE 1 pcs ON MACHINE RC 162 ...
Page 70: ...Spearhead RC 132 162 70 MOTOR TRANSMISSION RC 132 ...
Page 72: ...Spearhead RC 132 162 72 MOTOR TRANSMISSION RC 162 ...
Page 75: ...Spearhead RC 132 162 75 ...
Page 76: ...Spearhead RC 132 162 76 ...