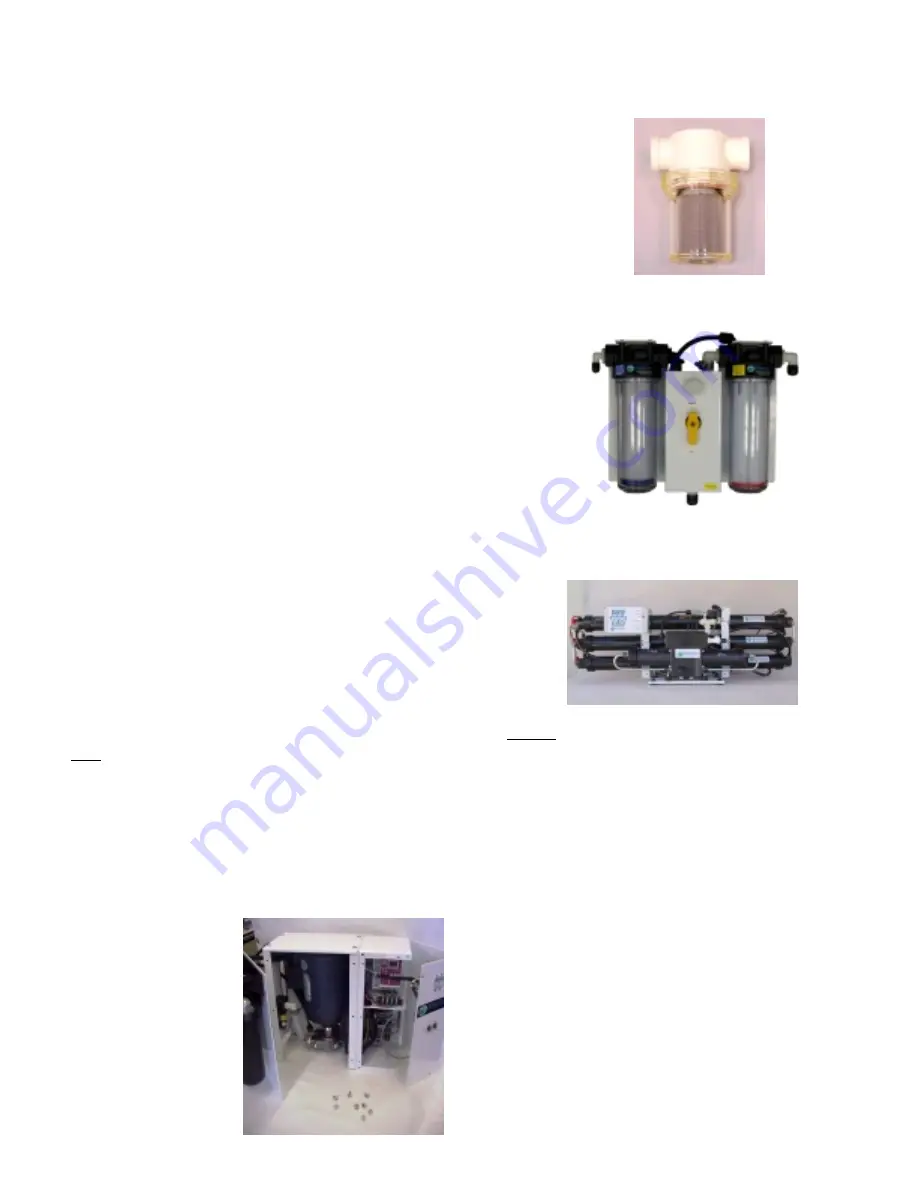
10
Component Placement
Refer to the Plumbing Diagrams
Strainer
Mount the strainer in an accessible area close to the intake through-
hull that can handle water spillage during service. Extra care during
assembly must be taken to avoid air leaks from the strainer. Use the
supplied “Quick Block” and wire tie for mounting.
The fresh water flush module should be located between the intake
strainer and the feed pump Module and as low as possible in the
vessel. It should be mounted with the filter housings vertical and
accessible for changing filters. Allow 2” below the filter housing
for removal. Do not install over electrical equipment. Remove filter
bowls for access to the screw holes in the mounting plate. The unit
contains a 50 Micron prefilter, charcoal filter for the flush water,
flush solenoid and three way intake service valve.
Optional Z– Brane
The optional Z-Brane Water treatment system is permanently in-
stalled in the membrane pressure vessels and continuously helps
prevent biogrowth and fouling of the membrane system.
Feed Pump/Main Module
Fresh Water Flush Module
Mount the feed pump/main module on a horizontal or vertical sur-
face that can be up to 4’ (1.2M) above the waterline. It is prefer-
able to mount as low as possible. Locate in an area that allows easy
access to filters and a location that will not be a problem when
water spills during filter change. Keep future maintenance in mind
when choosing a location. The Feed Pump module has overheat
shutdown protection. It must be installed in a dry location where
temperatures will not exceed 120degrees F (50C).
Remove front covers to
access mounting holes in
the enclosure.
Summary of Contents for Newport 1000
Page 2: ...2...
Page 4: ...4...
Page 6: ...6...
Page 8: ...8...
Page 38: ...38 Push the Auto Flush button press Stop press Auto Flush again...
Page 59: ...59 Z BRANE OPERATION MANUAL...