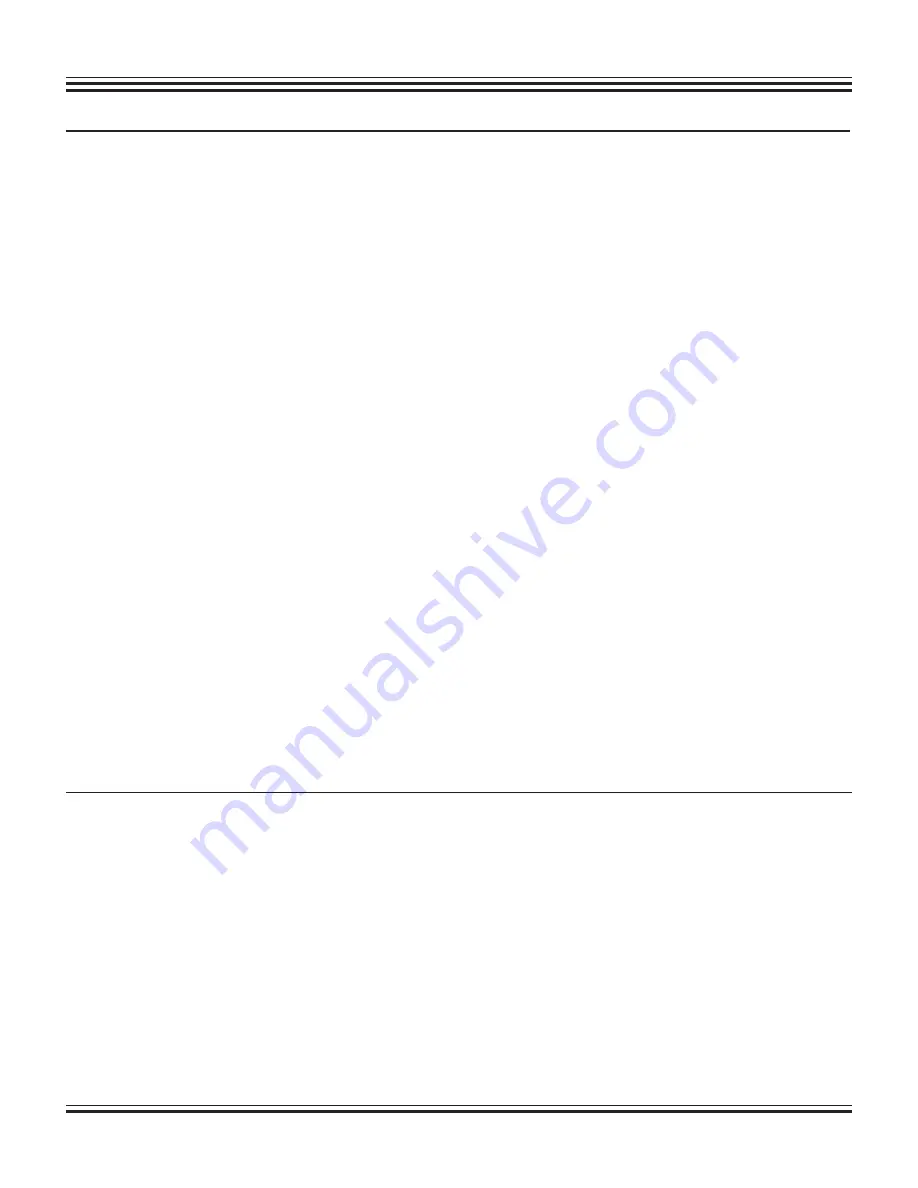
SpectraPure
®
SpectraPure
®
Inc.
480.894.5437 Call us toll-free 1.800.685.2783
2167 East Fifth St, Tempe, Arizona 85281
19
FILTER REPLACEMENT
(See Page 5 for filter locations.)
For maximum contaminant removal and long membrane life, the sediment and carbon prefilters should be changed at
6-month intervals. If your water contains a great deal of sediment or chlorine, the prefilters might have to be changed
at more frequent intervals to maintain an adequate production rate.
Sediment and Carbon block filter Replacement:
Maintenance Regime:
15 -20% drop in pressure OR at least once in 6 months OR when chlorine breakthrough
occurs.
Materials Needed:
(DWS-90; DWS-PP-90)
0.5 micron MicroTec™ sediment filter, 0.5 micron carbon block filter, GAC carbon post
filter, filter wrench
Materials Needed:
(MPDW-90)
1 micron MicroTec™ sediment filter, 1 micron carbon block filter, Inline carbon post filter,
filter wrench.
Procedure:
1. Shut off feed supply valve, close ball valve on tank, open the faucet and wait until pressure is relieved.
2. Remove the filter housings from their caps by unscrewing them clockwise as viewed from top or side. A filter wrench
may be needed. Discard old filters.
3. Thoroughly wash out the housings with hot soapy water to which a few teaspoons of household bleach have been
added, and rinse well with clean hot water.
4. Install the new sediment prefilter in the leftmost housing. Check to be sure that the O-ring is positioned in its groove
and hand tighten housing.
5. Install carbon block prefilter in appropriate housing making sure O -ring and black gaskets are in place. Hand tighten
housing.
6. (DWS-90, DWS-PP-90) Install GAC carbon post filter in rightmost housing making sure O -ring and black gaskets are
in place. Hand tighten housing.
7. (MPDW-90) Disconnect blue lines from inline carbon filter (See page 5 for location), remove the filter from the clips
and discard, insert new filter in clips and reattach blue lines.
NOTE: Make sure arrow on inline carbon housing is pointing towards the faucet (See “MPDW-90 Connections on
page 6).
8. Close faucet, open ball valve on tank, turn feed supply valve “ON”, wait for tank to fill, and check for leaks.
RECHARGING THE BLADDER TANK
If the storage capacity of the tank is diminished significantly it is likely that the tank has lost its air charge. Recharging the
bladder tank will restore its capacity.
Be sure water supply to the RO/DI system is turned off and the dispenser faucet is open. This will completely drain the
pressure tank.
1. Put the dispenser faucet in the “open” position (lever in up position). Leave the faucet in the open position until
the procedure is completed.
2. Drain as much water as possible from the tank.
3. Hook up an air pump to the “schrader” (tire) valve on the pressure tank and start pumping air into the tank.
4. Expel all the water from the tank.
5. Continue pumping air into the tank until the pressure reads NO MORE than 7 PSI.
6. This completes the procedure. Turn system back on.
NOTE: Should this procedure fail to restore the capacity of the tank, it is very likely that the bladder in the tank is
ruptured and the tank needs to be replaced.