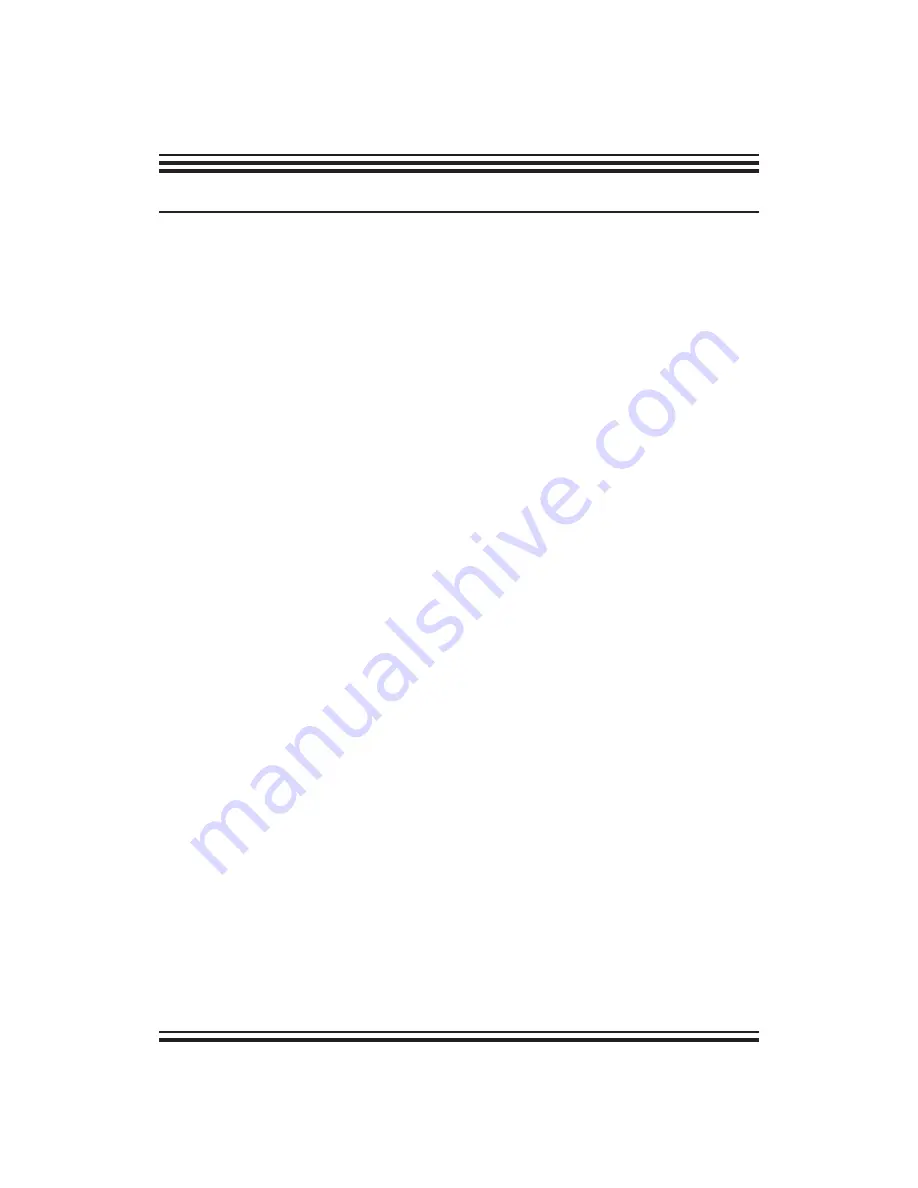
SpectraPure
SpectraPure®Inc.
480.894.5437 Call us toll-free 1.800.685.2783
2167 East Fifth St, Tempe, Arizona 85281
®
18
1. Low production rate:
a.
Plugged
pre-filters.
i.
Replace
pre-filters.
b.
low
water
temperature.
ii.
Heat feed water OR use higher GPD
membrane.
c.
low
line
pressure.
iii. Use booster pump OR use higher GPD membrane.
d.
high
TDS
content.
iv. Use booster pump OR use higher GPD membrane.
e. fouled membrane.
v. Clean or replace membrane to restore flux.
f. plugged flow restrictor.
vi. Replace flow restrictor & membrane.
2. Zero production rate:
a. Missing flow restrictor.
i. Put flow restrictor in the yellow line.
b. Dried membrane.
ii. Try to restore flux using rubbing alcohol OR
replace
membrane.
c. Plugged flow restrictor.
iii. Replace flow restrictor and clean/replace
membrane.
3. Extremely high production rate:
a.
Ruptured
membrane.
i.
Replace
it.
b. Very high line pressure (> 90 psi).
ii. Use a pressure reducing valve.
4. Red light on purity monitor comes on:
a. Exhausted deionization cartridge.
i. Replace cartridge.
b. Bad membrane & exhausted cartridge. ii. Replace membrane & deionization cartridge.
c.
Faulty
monitor/probe.
iii.
Replace
monitor/probe.
5. Pressure gauge does not register anything:
a. Missing flow restrictor.
i. Put flow restrictor in the yellow line.
b. Pressure gauge screwed in too far.
ii. Unscrew pressure gauge one turn and retest.
c. Plugged pressure gauge orifice.
iii. Clean orifice with a needle.
d. Defective pressure gauge.
iv. Replace it.
6. Low deionization cartridge life:
a.
Defective
membrane.
i.
Replace
it.
b. Low pressure (< 40 psi).
ii. Use booster pump.
c. High CO2 levels in water (> 5 ppm).
iii. Aerate RO product water or use a straight
anion
cartridge
ahead
of
DI
cartridge.
d. High TDS in feed water (> 1000 ppm). iv. NO EASY SOLUTION.
e. High levels of silica, nitrates,
v. Use straight anion cartridge ahead of mixed
phosphates etc. in tap water.
bed cartridge.
f. High pH tap water (> 9.0).
vi. Acidify feed water to the RO membrane
to
improve
its
rejection.
TROUBLESHOOTING GUIDE FOR RO/DI SYSTEMS: