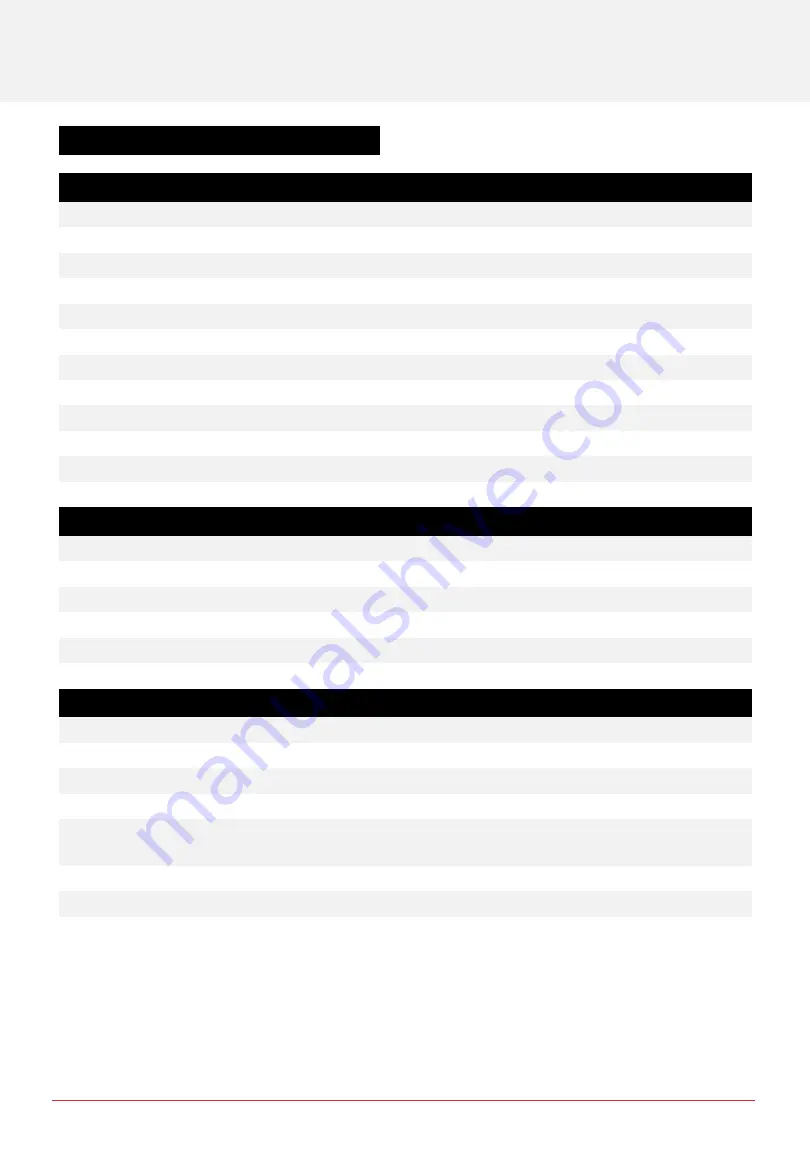
Fuel Cell
PROTIUM-1000
Type
PEM
No. of cells
30
Architecture
Closed cathode
Coolant
Air cooled
Rated/gross power
1000/1200W
Rated/gross current
55.5/66.6A
Voltage output
18-27VDC
Start-up time
30s
Operating ambient temperature
[-10,45]
o
C
Operating altitude without power derating
1500m AGL
System weight
4,800g
Max dimension
396 x 165 x 324mm
Fuel Supply
Hydrogen gas
Dry, 99.999% purity
Delivery pressure
0.7bar (10 psig)
Fuel consumption @ rated power
12.5L/min
Gas tubing
PU, 8 x 5.5
Supply & purge control
Solenoid valves with integrated pressure sensor
Stack leakage checks
Automated via integrated pressure sensors
Electronic Controller
Processor board
FEATHER V1.2
External power supply requirement
15-90V, 150W max
Weight (including casing)
680g
Output connector
XT-90
Warning & protections
Low voltage, high/low temperature, high/low
pressure, low battery, stack leakage
Communication
868MHz ultra long range radio modem
Data acquisition (DAQ) software GUI
PC/Android app
Remote control
Fan speed, blower speed, manual purge, remote on-
off
CHAPTER 2 | SPECIFICATIONS
2
SPECIFICATIONS
2.1 PROTIUM-1000 TECHNICAL DATA SHEET