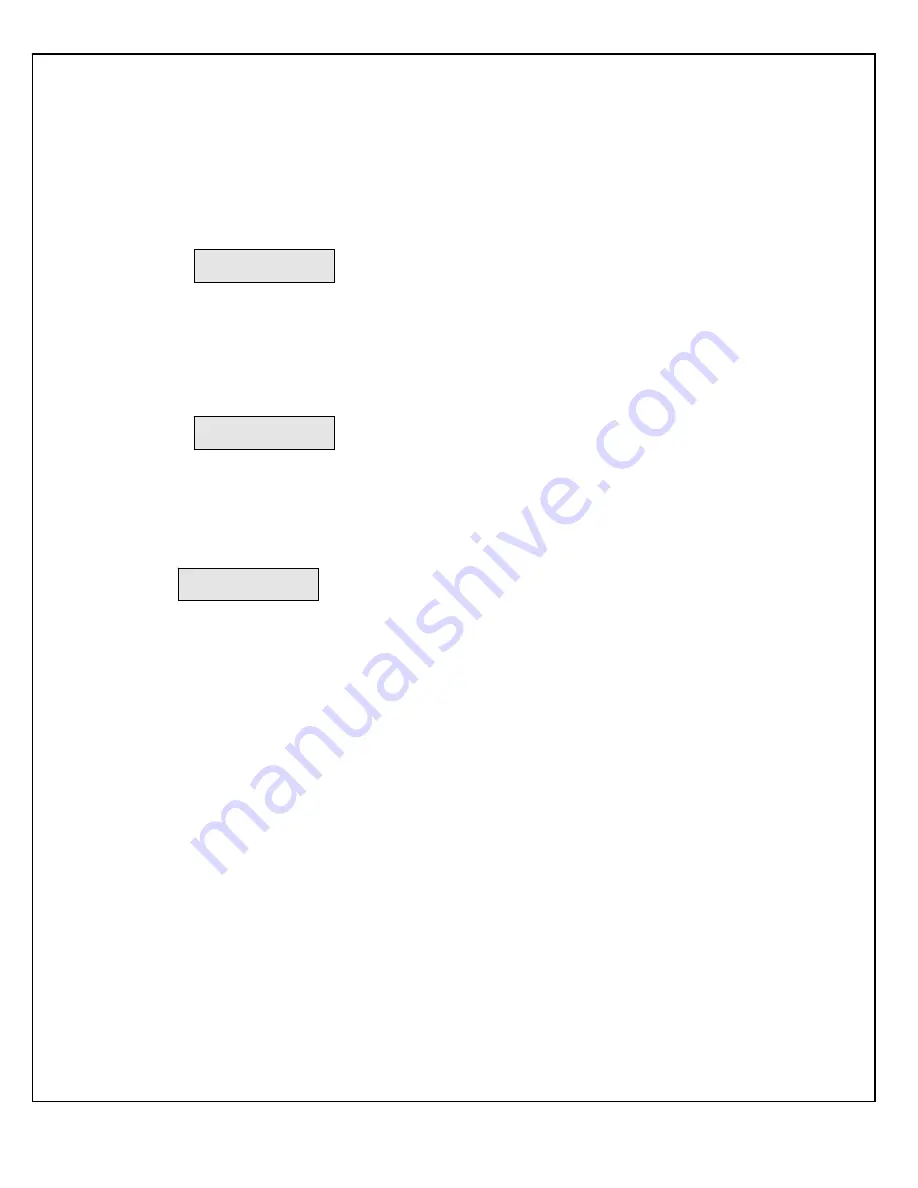
SL2KW SERIES MANUAL
8
118088-001 REV C
M)
To turn off the power supply, turn the circuit breaker
to the off position (0).
NOTE:
If a power supply fault, or system
monitoring fault occurs, the power supply will revert
to the POWER DOWN mode. In this mode the
output power will be turned off. The HV OFF lamp
will be off. To reset, depress the HV OFF switch.
AFTER TURNOFF, DO NOT HANDLE THE LOAD
UNTIL THE CAPACITANCE HAS BEEN
DISCHARGED!
LOAD CAPACITANCE MAY BE DISCHARGED BY
SHORTING TO GROUND.
THE VOLTMETER ON THE POWER SUPPLY
FRONT PANEL DOES NOT READ THE OUTPUT
VOLTAGE WHEN THE POWER IS TURNED OFF,
EVEN IF A CHARGE STILL
EXISTS ON THE LOAD.
ALWAYS OPERATE THE UNIT WITH THE COVER
ON.
A fan maintains safe operating temperature in the power
supply by drawing air over the circuit components. The
cover must be on in order to direct the air flow over the
areas that need cooling. In operation, the unit must be
placed so that the air intake and the fan exhaust are clear
of obstructions that might impede the flow of air.
3.2 Standard Features
A note on remote interface circuitry and remote signal
grounding. Whenever possible, electrical isolation should
be provided when interfacing with any high voltage
power supply. For power control signals such as
EXTERNAL INTERLOCK, HIGH VOLTAGE OFF,
AND HIGH VOLTAGE ON, isolated relay contacts
should be used. For status signals and control signals
such as HIGH VOLTAGE ON, HIGH VOLTAGE OFF,
and EXTERNAL INHIBIT, etc., opto-isolation should be
used. If possible, analog programming and monitoring
signals should be isolated via analog isolation amplifiers.
Spellman application engineers are available to assist in
interface circuitry design. All interface cables should be
properly shielded. All power supply signals should be
referenced to the power supplies signal ground on the rear
external interface.
REMOTE PROGRAMMING:
Allows remote
adjustment of the output voltage and current via an
external voltage source. In local control (front panel
control), jumpers are installed on the external
interface J5 in the rear of the chassis between J5-10
and J5-11 for voltage control and between J5-8 and
J5-9 for current control.
For remote programming, the jumpers are removed and a
positive voltage source, from 0V to 10V, is applied to the
appropriate terminals. Programming signals should be
referenced to J5-1, signal ground. By adjusting the
voltage source from 0V (zero output) to 10V (full rated
output), the desired output can be selected. See Figure
3.2A for the wiring diagram and specifications.
An alternate method of controlling the output remotely is
by using external resistance, such as a potentiometer or a
resistor network. For remote control the jumpers are
removed and the desired register configuration installed.
See Figure 3.2B for the wiring diagram.
REMOTE MONITOR:
Test points are made
available at the 25 pin D connector on the rear of the
chassis for monitoring the voltage and current output.
The test points are always positive regardless of the
output polarity where 0V to 10V equals 0 to 100% of
the output
0.5%. Test points have an output
impedance of 5K ohms. See Figure 3.3 for the test
point designation.
REMOTE CONTROL:
Remote control of the
HIGH VOLTAGE ON and HIGH VOLTAGE OFF
can be accomplished via the rear panel interface.
HIGH VOLTAGE OFF and HIGH VOLTAGE ON
can be controlled by momentary normally closed and
normally open contacts respectively. See Figure 3.4
on page 14 for the recommended interface.
EXTERNAL INHIBIT:
Allows the user to inhibit
the power supply output without switching HIGH
VOLTAGE OFF control. This circuit can be used to
generate fast slewing output waveforms or control of
high voltage generation as in Laser and Capacitor
discharge applications. The maximum inhibit rate
should not exceed 5Hz. Consult the factory for
higher repetition rates or high pulse load
applications. See Figure 3.5 for the recommended
interface circuit.
WARNING
WARNING
CAUTION