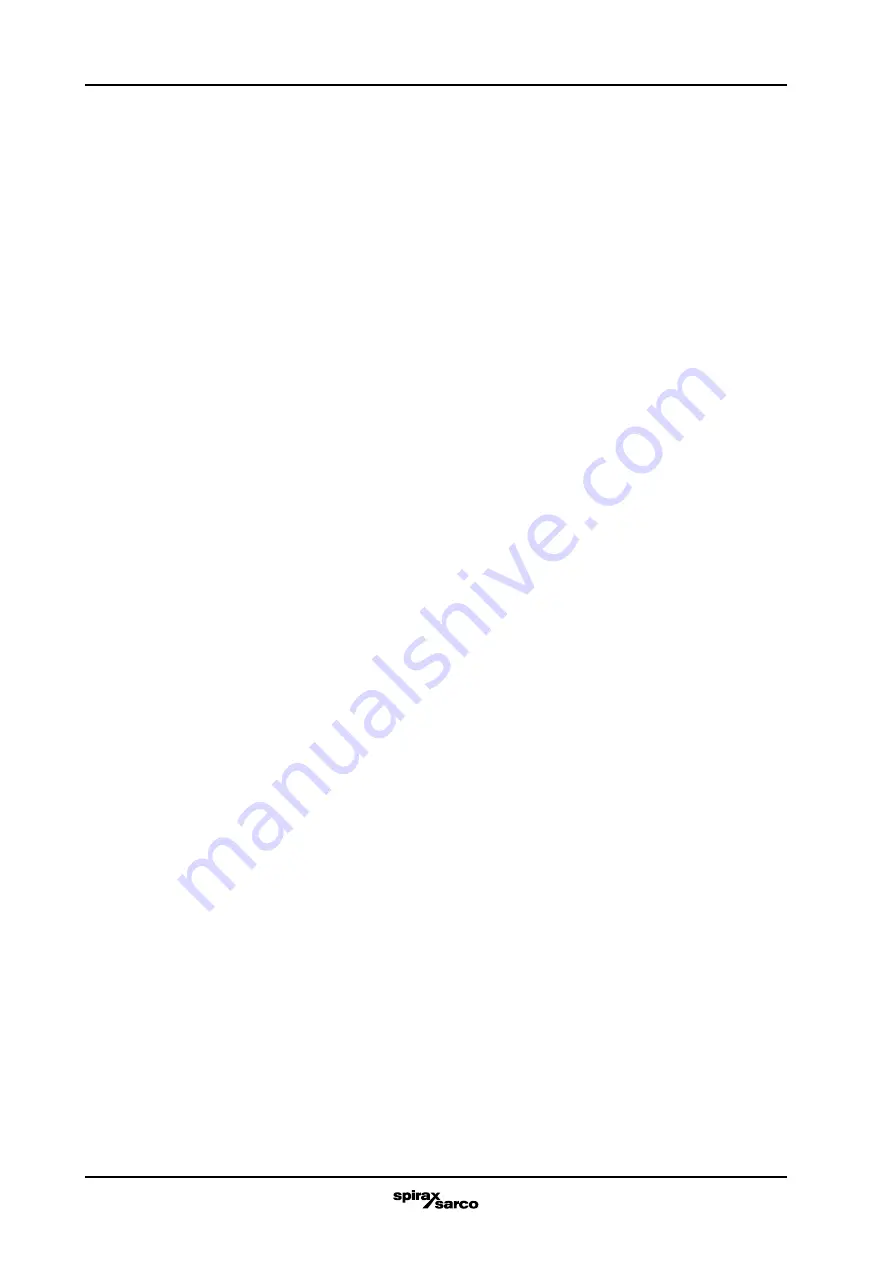
3.696.5275.210
32
∆
There may still be residual steam condensate (or boiler / high temperature
water), this residual condensate / water could present a danger of injury in the coil
that can run out during removal of the coil from the tank if sufficient time has not
been allowed for cooling.
6. Examine the heat exchanger coil for scale buildup and signs of leakage. If no leakage
is detected, carefully clean the excess scale from the coils and prepare the heat
exchanger coil for installation. If leakage is detected between the coils and water in
the tank, either repair the leaking coil(s) or replace the heat exchanger coil.
7. Remove the old gaskets and completely clean the mating surfaces. Install the two (2)
new gaskets: one (1) between the tube face of the coil and the flange welded to the
tank, and one (1) gasket with a divider to fit between the head and the tubesheet.
8. Carefully insert the heat exchanger coil into the tank. The coil should be installed so
that the divider in the head lines up with the coil, and that the divider is parallel to the
horizon.
9. After assuring that the heat exchanger unit is correctly aligned, clamp the flanges
together and proceed with the torque procedure detailed in appendix A.
a. Lubricate the bolt threads and the nut faces with a suitable lubricant.
b. Insert the bolts through the flanges, then start and finger tighten the nuts.
c. Number all bolts so that torquing requirements can be followed.
d. Apply torque in twenty percent (20% [1/5]) steps of required final torque, loading
all bolts at each step before proceeding to the next step.
e. Use rotational tightening until all bolts are stable at final torque level.
A minimum of two (2) rotations is usually required.
10. Reconnect the energy source inlet and clean steam outlet lines to the heat exchanger
coil. If these lines were broken at an additional location to allow for removal of the coil,
be sure to also tighten those connections. Follow recommendations contained in the
manufacturers documentation, local codes, or accepted contractor practices as to the
use and / or type of joint compound or sealer at the connections.
11. Reconnect the small line leading to the energy source pressure gauge.
12. Follow the startup procedures to put the unit back on-line.
Carefully check all connections for any sign of leakage.
Inlet, Outlet, and Condensate / Water Return Line and Manual Shutoff
Valves - Replacement
If any of the inlet, outlet, return lines, or shutoff valves are damaged and must be replaced,
follow the steps outlined below.
∆
The combination of electricity, steam, and water can pose a very dangerous
situation. Turn off / disconnect all electric power before attempting any maintenance
procedures.
1. Follow the shutdown procedure (page 22) to take the unit off-line before attempting to
replace damaged lines or shutoff valves.
∆
While it might seem feasible to replace inlet, outlet, condensate / water return
lines, and shutoff valves without shutting down the entire unit, it is not advised.
Unless the unit is completely shutdown, and the clean steam and energy source are
isolated from the system, failure of a manual shutoff valve during the replacement
process could result in serious injury.
Summary of Contents for CSM-C
Page 6: ...3 696 5275 210 2...