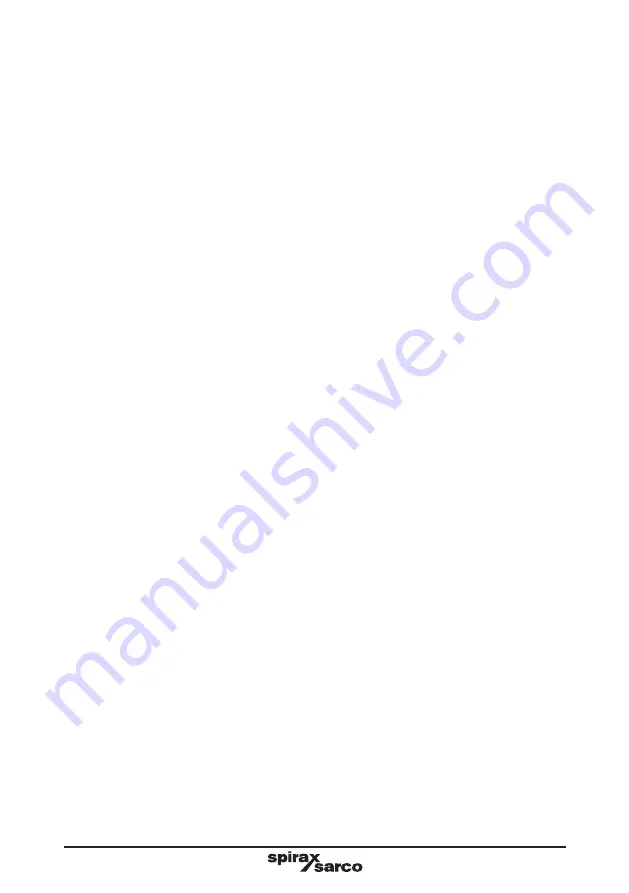
IM-P130-29
CMGT Issue 7
5
1.2 Access
Ensure safe access and if necessary a safe working platform (suitably guarded)
before attempting to work on the product. Arrange suitable lifting gear if required.
1.3 Lighting
Ensure adequate lighting, particularly where detailed or intricate work is required.
1.4 Hazardous liquids or gases in the pipeline
Consider what is in the pipeline or what may have been in the pipeline at some
previous time. Consider: flammable materials, substances hazardous to health,
extremes of temperature.
1.5 Hazardous environment around the product
Consider: explosion risk areas, lack of oxygen (e.g. tanks, pits), dangerous gases,
extremes of temperature, hot surfaces, fire hazard (e.g. during welding), excessive
noise, moving machinery.
1.6 Isolation
Consider the effect on the complete system of the work proposed. Will any proposed
action (e.g. closing isolation valves, electrical isolation) put any other part of the
system or any personnel at risk?
Dangers might include isolation of vents or protective devices or the rendering
ineffective of controls or alarms. Ensure isolation valves are turned on and off in a
gradual way to avoid system shocks.
1.7 Pressure
Before attempting any maintenance consider what is or may have been in the
pipeline. Ensure that any pressure is isolated and safely vented to atmospheric
pressure before attempting to maintain the product, this is easily achieved by
fitting Spirax Sarco depressurisation valves type DV (see separate literature for
details) and consider double isolation (double block and bleed) and the locking or
labelling of closed valves. Do not assume that the system is depressurised even
when a pressure gauge indicates zero.
1.8 Temperature
Allow time for temperature to normalise after isolation to avoid the danger of burns
and consider whether protective clothing (including safety glasses) is required.
1.9 Tools and consumables
Before starting work ensure that you have suitable tools and/or consumables available.
Use only genuine Spirax Sarco replacement parts.
1.10 Protective clothing
Consider whether you and/or others in the vicinity require any protective clothing
to protect against the hazards of, for example, chemicals, high / low temperature,
radiation, noise, falling objects, and dangers to eyes and face.
Summary of Contents for SGC40
Page 2: ...IM P130 29 CMGT Issue 7 2...
Page 16: ...IM P130 29 CMGT Issue 7 16...