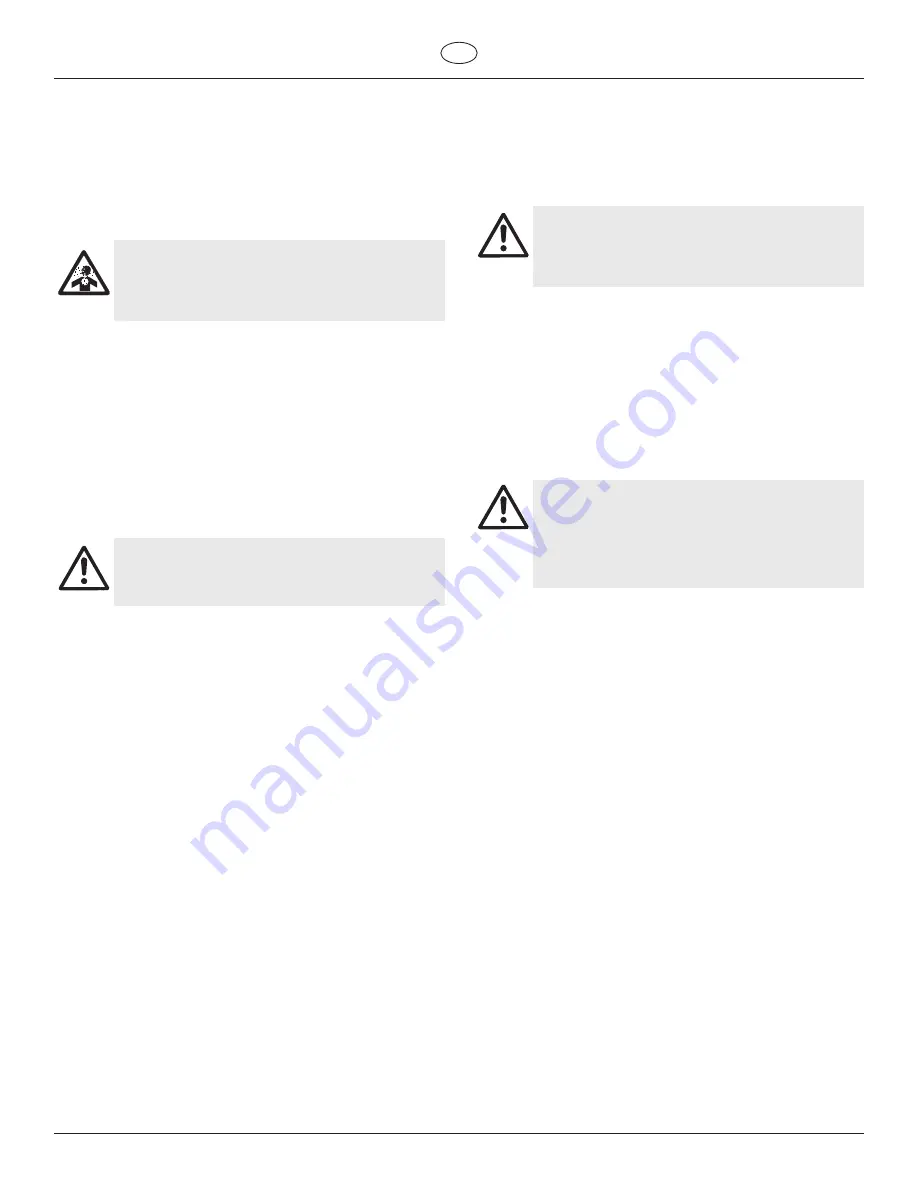
ProSpray 3.20
3
GB
Safety precautions
• Follow material and solvent manufacturer’s warnings and
instructions. Be familiar with the coating material’s MSDS
sheet and technical information to ensure safe use.
• Use lowest possible pressure to flush equipment.
• When cleaning the unit with solvents, the solvent should
never be sprayed or pumped back into a container with a
small opening (bunghole). An explosive gas/air mixture can
arise. The container must be earthed.
HAZARD: HAZARDOuS VAPORS
Paints, solvents, and other materials can be harmful
if inhaled or come in contact with body. Vapors can
cause severe nausea, fainting, or poisoning.
PREVENTION:
• Wear respiratory protection when spraying. Read all
instructions supplied with the mask to be sure it will provide
the necessary protection.
• All local regulations regarding protection against hazardous
vapors must be observed.
• Wear protective eyewear.
• Protective clothing, gloves and possibly skin protection cream
are necessary for the protection of the skin. Observe the
regulations of the manufacturer concerning coating materials,
solvents and cleaning agents in preparation, processing and
cleaning units.
HAZARD: GENERAL
This product can cause severe injury or property
damage.
PREVENTION:
• Follow all appropriate local, state, and national codes
governing ventilation, fire prevention, and operation.
• Pulling the trigger causes a recoil force to the hand that is
holding the spray gun. The recoil force of the spray gun is
particularly powerful when the tip has been removed and
a high pressure has been set on the airless pump. When
cleaning without a spray tip, set the pressure control knob to
the lowest pressure.
• Use only manufacturer authorized parts. User assumes all
risks and liabilities when using parts that do not meet the
minimum specifications and safety devices of the pump
manufacturer.
• ALWAYS follow the material manufacturer’s instructions for
safe handling of paint and solvents.
• Clean up all material and solvent spills immediately to prevent
slip hazard.
• Wear ear protection. This unit can produce noise levels above
85 dB(A).
• Never leave this equipment unattended. Keep away from
children or anyone not familiar with the operation of airless
equipment.
• Do not spray on windy days.
• The device and all related liquids (i.e. hydraulic oil) must be
disposed of in an environmentally friendly way.
1.2
Electric Safety
Electric models must be earthed. In the event of an electrical short
circuit, earthing reduces the risk of electric shock by providing an
escape wire for the electric current. This product is equipped with
a cord having an earthing wire with an appropriate earthing plug.
Connection to the mains only through a special feed point, e.g.
through an error protection insallation with INF < 30 mA.
DANGER — Work or repairs at the electrical
equipment may only be carried out by a skilled
electrician. No liability is assumed for incorrect
installation. Switch the unit off. Before all repair
work, unplug the power plug from the outlet.
Danger of short-circuits caused by water ingressing into the electrical
equipment. Never spray down the unit with high-pressure or high-
pressure steam cleaners.
Work or repairs at the electrical equipment:
These may only be carried out by a skilled electrician. No liability is
assumed for incorrect installation.
1.3
Electrostatic charging (formation of sparks or
flames)
Electrostatic charging of the unit may occur during
spraying due to the flow speed of the coating
material. These can cause sparks and flames upon
discharge. The unit must therefore always be
earthed via the electrical system. The unit must be
connected to an appropriately-grounded safety
outlet.
An electrostatic charging of spray guns and the high-pressure hose
is discharged through the high-pressure hose. For this reason the
electric resistance between the connections of the high-pressure
hose must be equal to or lower than 1 MΩ.