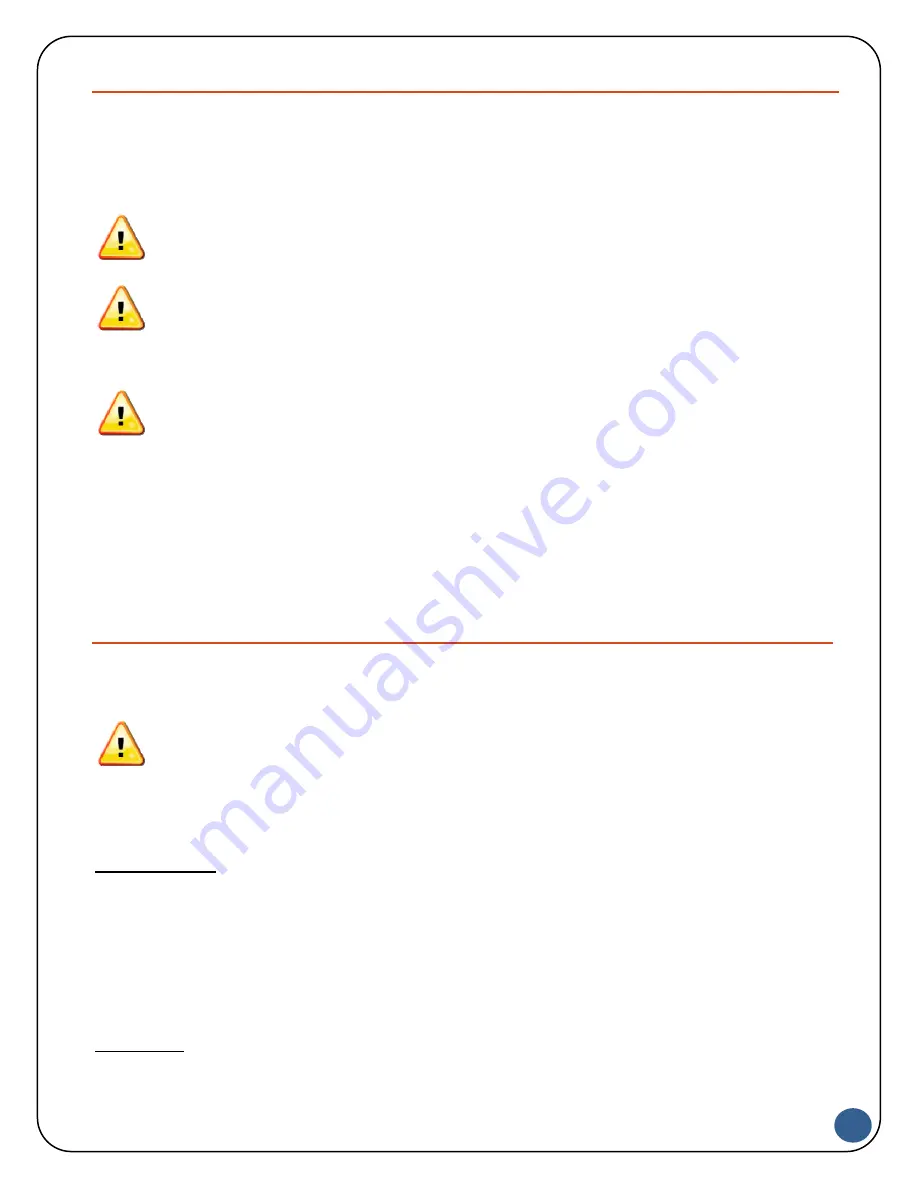
AA
09
0AG
Seri
es
Air
Mo
tor
‐
Driven
Tank
Wa
sher
0
8/
15/
20
11
7
SAFETY
PRECAUTIONS
YOUR
SAFETY
AND
THE
SAFETY
OF
OTHERS
IS
EXTREMELY
IMPORTANT.
WE HAVE PROVIDED IMPORTANT SAFETY MESSAGES IN THIS MANUAL FOR YOUR
PRODUCT. ALWAYS READ AND OBEY ALL SAFETY MESSAGES.
THIS IS THE SAFETY ALERT SYMBOL. THIS SYMBOL ALERTS YOU TO HAZARDS
THAT CAN KILL OR HARM YOU AS WELL AS OTHERS. THE SAFETY ALERT
SYMBOL AND THE WORDS “DANGER” AND “WARNING” WILL PRECEDE ALL
SAFETY MESSAGES. READ THE FOLLOWING WORDS AND WHAT THEY SIGNIFY:
DANGER
YOU MAY BE KILLED OR SERIOUSLY INJURED IF YOU DON’T FOLLOW THESE
INSTRUCTIONS.
WARNING
YOU MAY BE SERIOUSLY INJURED IF YOU DON’T FOLLOW THESE INSTRUCTIONS.
ALL SAFETY MESSAGES WILL IDENTIFY THE HAZARD, TELL YOU HOW TO REDUCE THE
CHANCE OF INJURY AND TELL YOU WHAT CAN HAPPEN IF THE SAFETY INSTRUCTIONS
ARE NOT FOLLOWED.
INSTALLATION
Qualified personnel must perform all work required to assemble, install, operate, maintain and
repair this equipment. Improper installation and operation can result in severe personal injury
and/or damage to property. Correct installation is your responsibility.
WARNING
Install proper guards as needed. Follow basic lifting guides when transporting or handling this
product. Failure to follow this instruction can result in back injury, burns or other serious injury.
CONNECTIONS
Please refer to datasheet 090AG during installation. Connect the air muffler (shipped loose) to the
air motor exhaust connection. The exhaust connection is the threaded connection on the left as
you face the motor openings. Connect the lubricator sub-assembly to the air inlet connection of the
air motor. The inlet connection is the threaded connection on the right as you face the motor
openings. Attach a compressed air line to the quick connect fitting of the pressure regulator and
verify that the nozzle hub rotates clockwise when viewed from the nozzle hub end by applying air
pressure to the motor. Connect the liquid line to the inlet connection of the liquid inlet body.
MOUNTING
Bolt or clamp the unit to the tank to be cleaned as dictated by the mounting flange provided.
Adjustable flanges allow easy positioning of the tank wash unit to various spray depths for
maximum cleaning effectiveness.