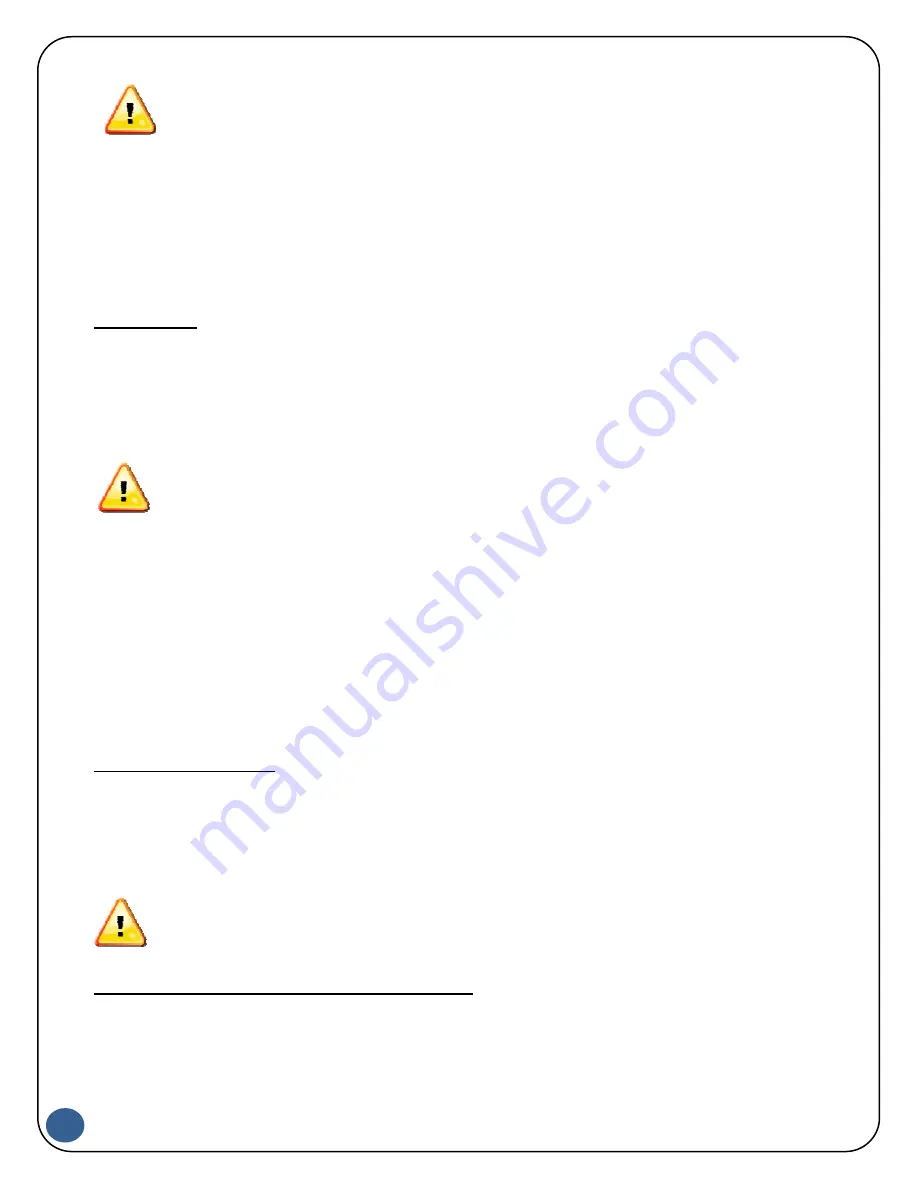
AA
19
0D
AG
Se
ries
Air
Motor
‐
Driven
Tank
Washer
|
1
1/
1
1/
20
10
|
RE
V
.
1
12
DANGER
IT IS YOUR RESPONSIBILITY TO ENSURE THAT THERE IS NO POSSIBILITY OF THE MOVING
PARTS COMING IN CONTACT WITH FIXED OBJECTS. FAILURE TO INSTALL THE TANK
CLEANER WITH SUFFICIENT CLEARANCES COULD RESULT IN THE GENERATION OF
SPARKS WITH A RESULTANT EXPLOSION OR FIRE. IF YOU DO NOT FOLLOW THESE
INSTRUCTIONS, YOU MAY BE KILLED OR SERIOUSLY INJURED.
GROUNDING
A GROUND SCREW IS PROVIDED ON THE LIQUID INLET BODY MARKED WITH A GROUND
SYMBOL. A GROUND WIRE SHOULD BE CLAMPED UNDER THE SCREW HEAD AND
CONNECTED TO EARTH GROUND VIA AN APPROVED GROUNDING METHOD. LIKEWISE, A
GROUND WIRE SHOULD BE AFFIXED TO THE TANK AND TERMINATED AT AN EARTH
GROUND.
DANGER
IT IS NOT SUFFICIENT TO GROUND ONLY THE TANK CLEANER OR THE TANK ITSELF
BECAUSE THE ELECTRICAL CONTINUITY BETWEEN THE TANK CLEANING UNIT AND TANK
CANNOT BE GUARANTEED. A SEPARATE GROUND CONNECTION FROM BOTH THE TANK
CLEANING UNIT AND THE TANK ITSELF SHOULD BE MADE. FAILURE TO FOLLOW THIS
INSTRUCTION CAN RESULT IN BUILDUP OF STATIC CHARGE BETWEEN THE TANK AND
THE TANK CLEANER PARTS WHICH COULD CAUSE A SUDDEN DISCHARGE OF CURRENT
WITH A RESULTANT EXPLOSION OR FIRE.
YOU MAY BE KILLED OR SERIOUSLY INJURED IF YOU DO NOT FOLLOW THESE
INSTRUCTIONS.
HIGH IMPACT SPRAYS
THIS TANK CLEANER MAY BE EQUIPPED WITH SOLID STREAM NOZZLES WHICH
CONCENTRATE THE FLOW ENERGY INTO A SMALL AREA FOR MAXIMUM IMPACT AND
CLEANING EFFICIENCY. OPERATION AT HIGH PRESSURE INCREASES THEIR
EFFECTIVENESS BUT ALSO CREATES A HAZARD IF THE PROPER PRECAUTIONS ARE NOT
FOLLOWED.
WARNING
INJURY HAZARD FROM HIGH IMPACT SPRAYS.
HIGH IMPACT SPRAYS CAN CAUSE SEVERE INJURY. THE LIQUID PRESSURE TO THE TANK
CLEANER SHOULD NEVER BE TURNED ON WHILE THE UNIT IS OUTSIDE THE TANK.
FAILURE TO FOLLOW THIS INSTRUCTION CAN RESULT IN FLUID PENETRATION
THROUGH CLOTHING AND INTO THE HUMAN SKIN CAUSING SEVERE INJURY, POSSIBLY
RESULTING IN AMPUTATION OR DEATH
. IF ANY PART OF THE BODY COMES IN CONTACT
WITH THE SPRAY STREAM, IMMEDIATELY CONSULT A PHYSICIAN.