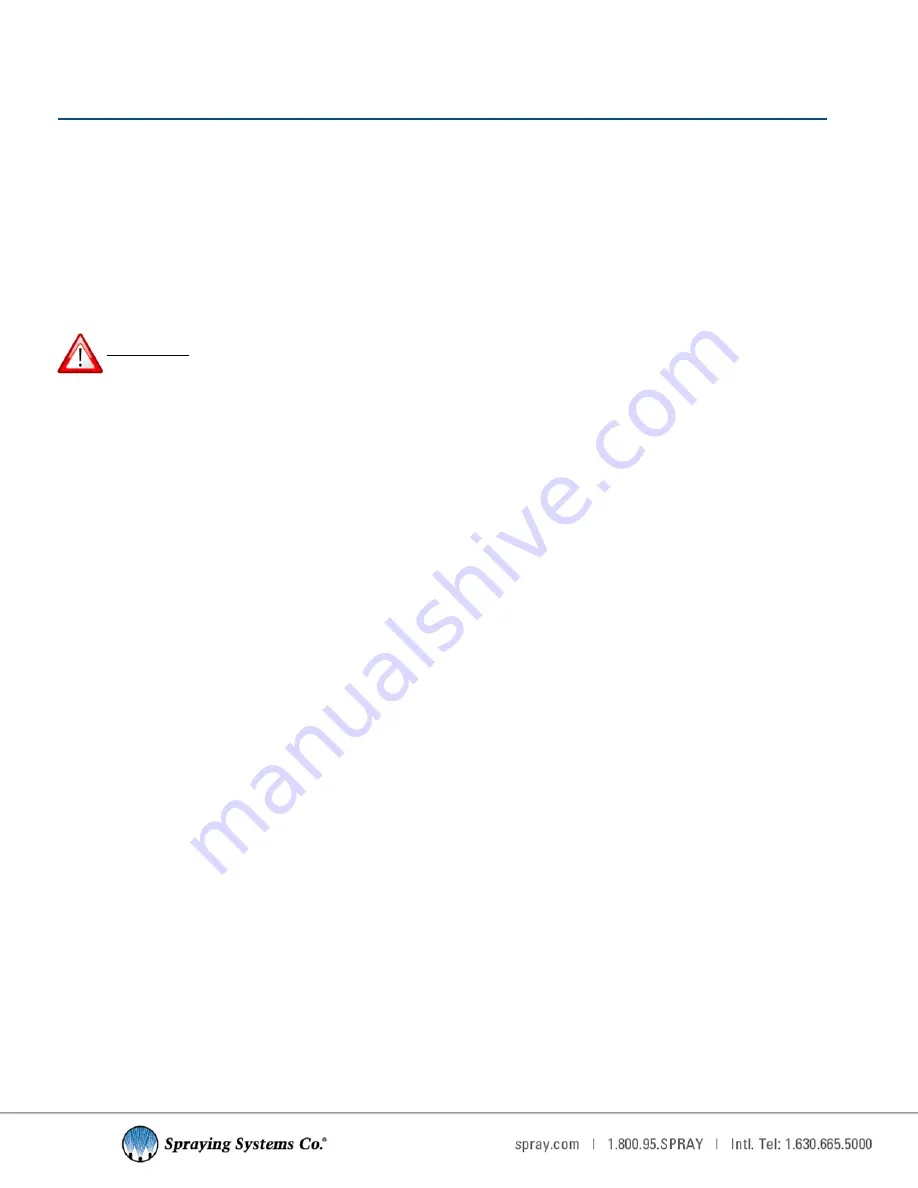
4
SECTION 2
SAFETY
2.1 GENERAL SAFETY INFORMATION
READ AND FOLLOW INSTRUCTIONS
All safety related and operating instructions should be read before the system is operated. Follow all operating instruc-
tions.
SERVICING
Do not attempt to service this system unless you have been trained or authorized to conduct repairs. Only authorized
and qualified service personnel should attempt to service this system. Service by unauthorized personnel will void any
warranties.
WARNING: Before performing any maintenance, make sure all components are completely cool,
electrical power is off, and any air/liquid pressure is bled from the system
.
REPLACEMENT PARTS
This system has been designed with components that work together to provide the best system performance. When
replacement parts are required, only Spraying Systems Co.
®
recommended components should be used to maintain
proper system operation, electrical, and pneumatic safety. The use of any unauthorized replacement parts will void
any warranties.
UNINTENDED USE
Use of Spraying Systems Co.
®
equipment in ways other than those described in the documentation supplied with the
equipment may result in injury to persons or damage to property. Examples of unintended use of equipment would
be:
•
Using incompatible materials
•
Making unauthorized modifications
•
Removing or bypassing safety guards or interlocks
•
Using incompatible or damaged parts
•
Using unapproved auxiliary equipment
•
Operating equipment in excess of maximum ratings
REGULATIONS AND APPROVALS
Make sure all equipment is rated and approved for the environment in which it is used. Any approvals obtained for
Spraying Systems Co. equipment will be voided if instructions for installation, operation, and service are not followed.
All phases of equipment installation must comply with federal, state, and local codes.
PERSONAL PROTECTIVE EQUIPMENT
Spraying Systems Co. strongly recommends the use of appropriate safety equipment when working in potentially haz-
ardous environments and chemicals. This safety equipment includes, but is not limited to, the following:
•
Protective hat
•
Safety glasses or face shield
•
Chemical
-
resistant safety gloves and apron
•
Long sleeve shirt and long pants
Users of this product should never place themselves in the path of the resulting spray. Users should consult and follow
the recommendations of the Safety Data Sheet (SDS) of any chemical or fluid sprayed using this system.