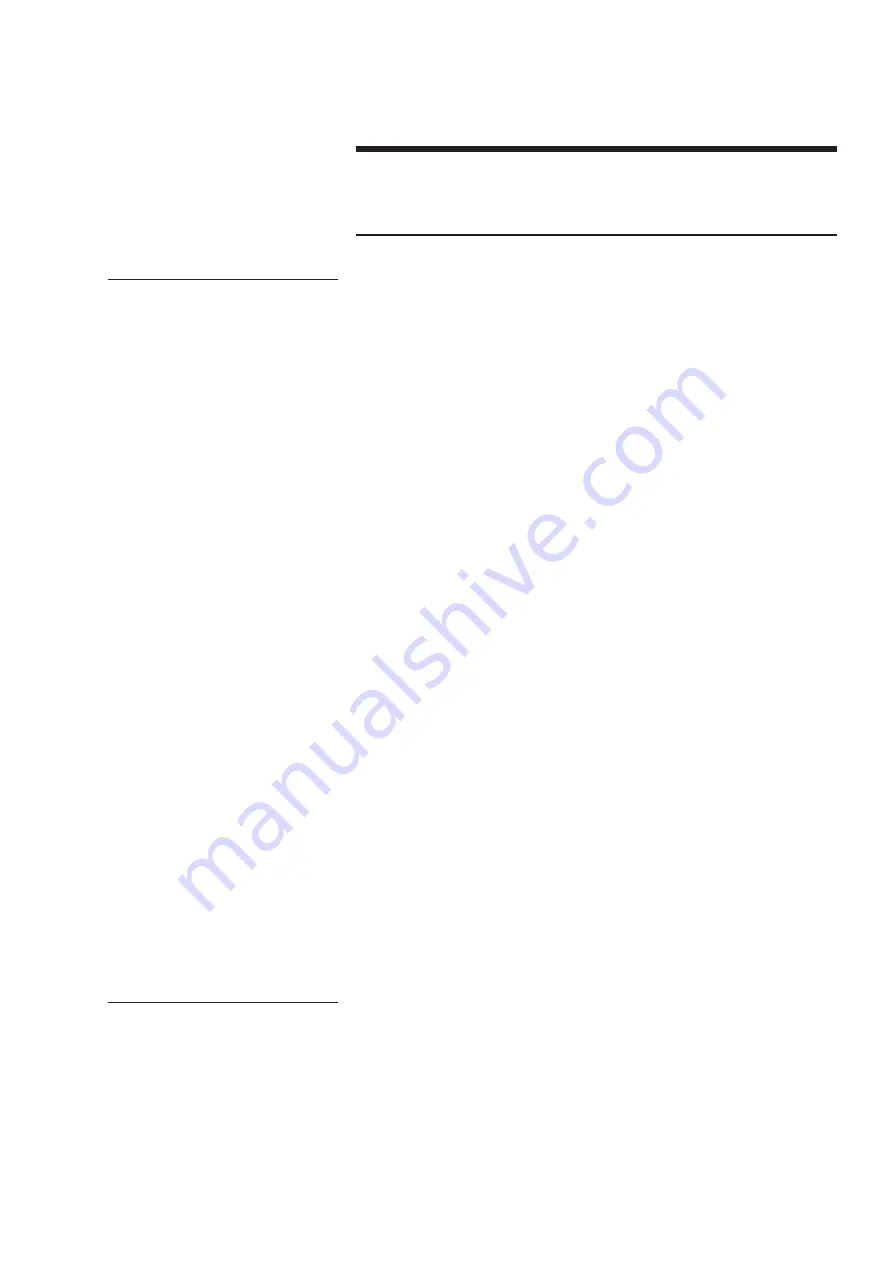
7
Fluid Cooler installation
These installation instructions are intended to help you prepare be-
fore your fluid cooler arrives. If discrepancies exist between these
instructions and those shipped with the fluid cooler, the instructions
shipped with the fluid cooler will govern.
1. Prior to placement of the fluid cooler, confirm that the supporting
platform is level, and that the anchor bolt holes are correctly located
in accordance with Marley drawings.
2. Place bottom module on your prepared supports, aligning anchor bolt
holes with those in your supporting steel. Make sure that the orienta-
tion agrees with your intended piping arrangement. Attach fluid cooler
to supporting steel with 13mm diameter bolts and flat washers (by
others). See support drawing for location and quantity. Position flat
washers between the bolt head and the fluid cooler basin flange.
3. Before setting top module in place on bottom module, clean any debris
from the underside of the top module, skid and beams and from the
top of the bottom module. Apply the mastic sealing strip supplied with
the fluid cooler according to the
MC Fluid Cooler Field Installation
Drawing
instructions. Place top module on the top peripheral bearing
surface of bottom module, aligning mating holes as it is set in place.
Attach top module to bottom module with fasteners provided accord-
ing the
MC Fluid Cooler Field Installation Drawing
instructions.
4. Connect the recirculation piping with rubber coupling shipped with
the bottom module piping according to drawings shipped with you
fluid cooler.
5. Attach makeup water supply piping to appropriately-sized float valve
connection located in collection water basin side wall. Install the drain
and overflow according to the
MC Fluid Cooler Field Installation
Drawing
instructions. If you wish to pipe overflow and drain water to
a remote discharge point, make those connections at this time also.
Fasteners and components provided by others that are to be attached
to the tower must be compatible with the fluid cooler materials—
i.e. fasteners in a stainless steel cold water basin must be stainless
steel.
Note
Installation
➠
Note
Summary of Contents for Hexacool Air Cooled Condenser none
Page 1: ...Marley MC Fluid Cooler User Manual uk_07 1185C...
Page 2: ......
Page 30: ......
Page 31: ......