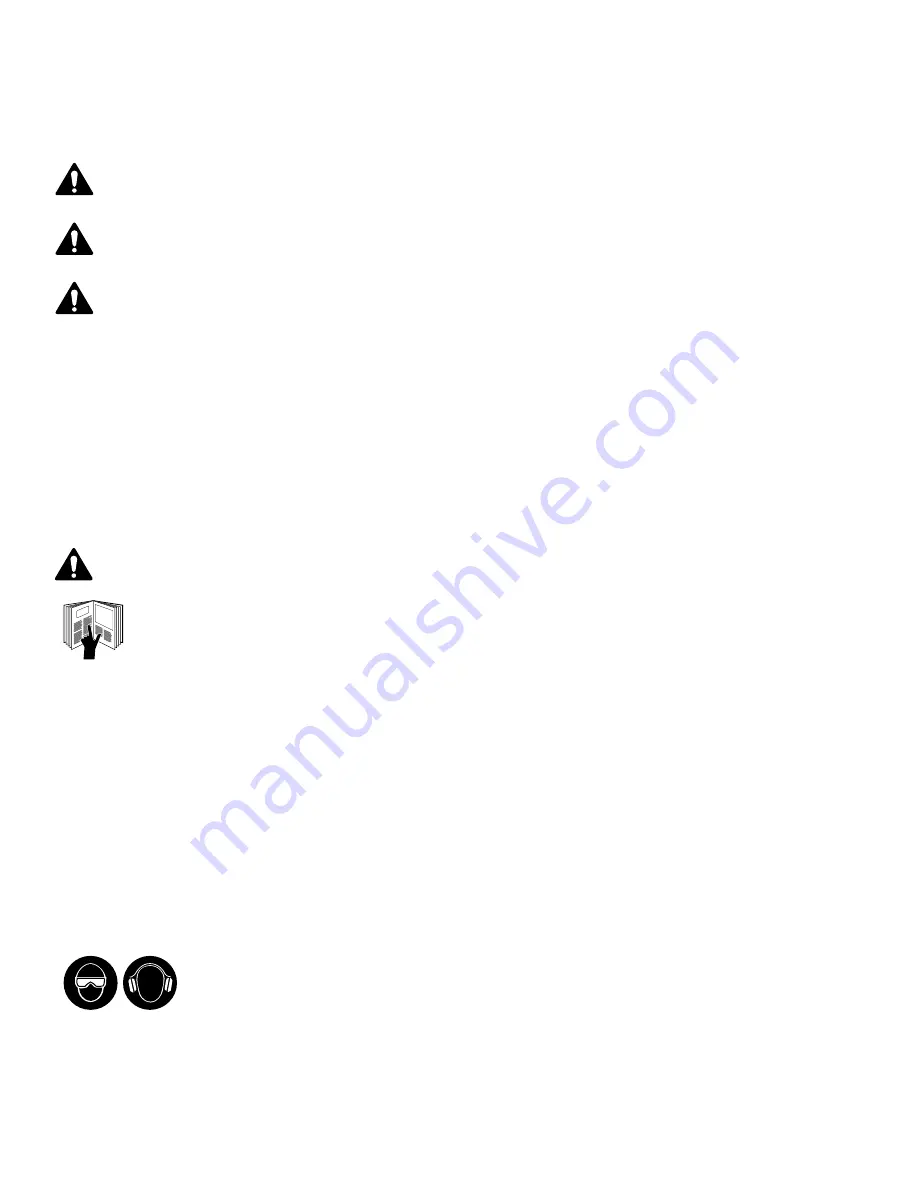
3
Form No. 1000853
Rev. 4 October 8, 2018
© 2018 SPX FLOW, Inc.
SAFETY DEFINITIONS
The safety signal word designates the degree or level of hazard seriousness.
DANGER: Indicates an imminently hazardous situation which, if not avoided, will result in death or
serious injury.
WARNING: Indicates a potentially hazardous situation which, if not avoided, could result in death or
serious injury.
CAUTION: Indicates a potentially hazardous situation which, if not avoided, may result in minor or
moderate injury.
CAUTION: Used without the safety alert symbol indicates a potentially hazardous situation which, if not
avoided, may result in property damage.
IMPORTANT: Important is used when action or lack of action can cause equipment failure, either immediate or
over a long period of time
WARNING: To prevent personal injury:
Read Instruction Manual before operation. For the latest revision of the instruction sheet please visit
the “Resources” page on our Website.
IMPORTANT: For instructions specific to the various system components refer to the related individual
instruction sheet.
IMPORTANT: The following procedures must be performed by qualified, trained personnel who are familiar
with this equipment. Operators must read and understand all safety precautions and operating instructions
included with equipment. If the operator cannot read these instructions, operating instructions and safety
precautions must be read and discussed in the operator’s native language.
• These products are designed for general use in normal environments. These products are not designed
for lifting and moving people, agri-food machinery, certain types of mobile machinery, or in special work
environments such as: explosive, flammable, or corrosive. Only the user can decide the suitability of this
product in these conditions or extreme environments. Power Team will supply information necessary to
help make these decisions. Consult your nearest Power Team facility.
Safety glasses must be worn at all times by the operator and anyone within sight of
the unit. Additional personal protection equipment may include: face shield, goggles, gloves, apron, hard
hat, safety shoes, and hearing protection. Check for local safety requirements and obey all safety rules and
regulations in force at the job site.
• The owner of this tool must ensure that safety-related decals are installed, maintained, and replaced if they
become hard to read.
SAFETY PRECAUTIONS