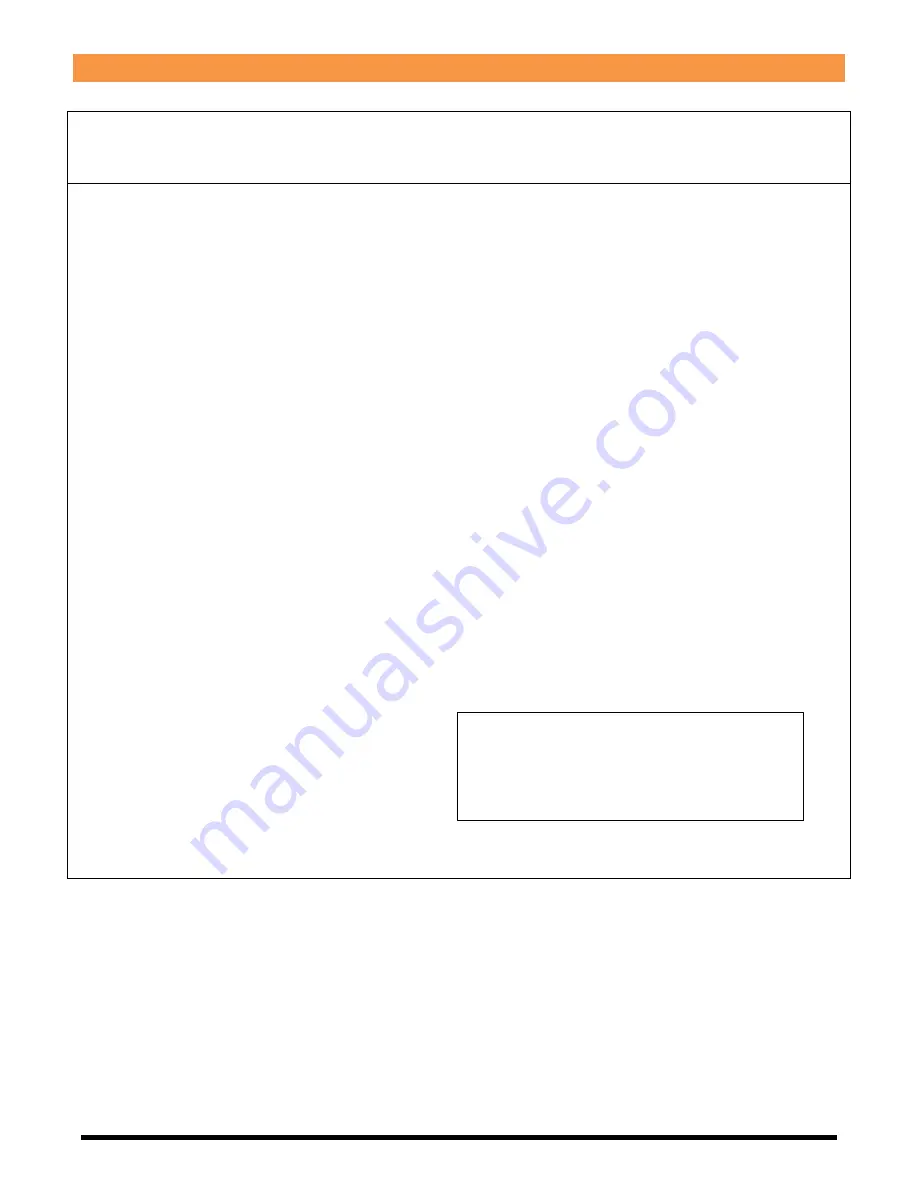
Series WTH
Page 48
LT105 Feb. 2019
Warranty
SERIES WTH INFRARED HEATERS
WARRANTY
The Manufacturer warrants to the original owner that the product will be free of defects in material and
workmanship. For the Series WTH, the warranty for all components is limited to 24 months from the date of
installation. The hot rolled heat exchanger shall be warranted for an additional 3 years for units which are proven to
the satisfaction of the manufacturer to be inoperative due to defects in material or workmanship. Aluminized heat
exchangers shall be warranted for an additional five years beyond burner components.
The Manufacturer’s obligation under this warranty is limited to repair or replacement, F.O.B. its facility, of the
defective part. In no event shall the manufacturer be liable for incidental expense or consequential damages of any
kind.
This warranty does not cover any shipping, installation or other costs incurred in the repair or replacement of the
product. No materials will be accepted for return without authorization.
This warranty will not apply if in the judgment of the Manufacturer, the equipment has been improperly installed,
unreasonably used, damaged or modified.
This warranty will not apply to damage to the product when used in corrosive atmospheres and in particular
atmospheres containing halogenated hydrocarbons. No person is authorized to assume for the Manufacturer any
other warranty, obligation or liability.
THE REMEDIES PROVIDED FOR IN THE ABOVE EXPRESS WARRANTIES ARE THE SOLE AND EXCLUSIVE
REMEDIES. NO OTHER EXPRESS OR IMPLIED WARRANTIES ARE MADE INCLUDING, BUT NOT LIMITED
TO, ANY IMPLIED WARRANTY OF MERCHANTABILITY OR FITNESS FOR A PARTICULAR USE OR
PURPOSE.
Address questions to your local distributor/ or
Heater Series:______________
Installed rate:_______________Btu/hr
Serial Number:______________
Installed date:_______________
563 Barton Street, Stoney Creek, Ontario L8E
5S1 Canada
Call: 905-664-8274