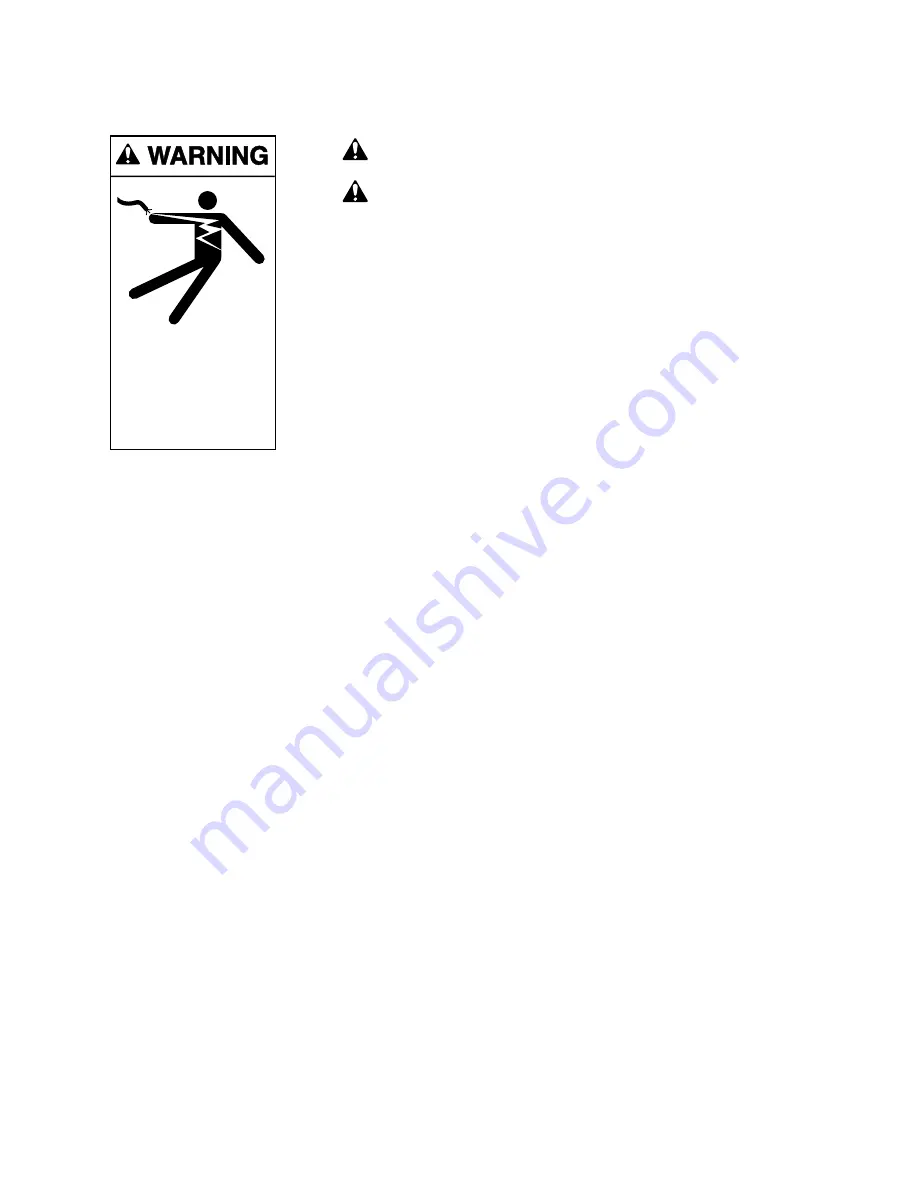
11
TROUBLESHOOTING GUIDE
Read and understand safety and operating instructions in this manual
before doing any work on pump!
Only qualified personnel should electrically test pump motor!
FAILURE TO PUMP; REDUCED CAPACITY OR DISCHARGE PRESSURE
Suction leaks/lost prime:
1. Pump must be primed; make sure that pump volute and trap are full of
water. See priming instructions, Page 7.
2. Make sure there are no leaks in suction piping.
3. Make sure suction pipe inlet is well below the water level to prevent
pump from sucking air.
4. If suction trap gasket is defective, replace it.
5. Suction lift of 15 to 25 feet (4.5 to 7.5 meters) will reduce performance.
Suction lift of more than 25 feet (7.5 meters) will prevent pumping and
cause pump to lose prime. In either case, move pump closure (vertically)
to water source. Make sure suction pipe is large enough.
Clogged pipe/trap/impeller, worn impeller:
6. Make sure suction trap is not clogged; if it is, clean trap and strainer.
7. Make sure impeller is not clogged (follow steps 1 through 7 under
“Removing Old Seal”, Page 9; check impeller for clogging; follow steps 7
through 11 under “Installing New Seal”, Page 10, for reassembly).
8. Impeller and diffuser may be worn. If so, order replacement parts from
Repair Parts List, Pages 12-14.
9. Pump may be trying to push too high a column of water. If so, a “higher
head” pump is needed.
Electrical:
10. Pump may be running too slowly; check voltage at motor terminals and at
meter while pump is running. If low, see wiring instructions or consult
power company. Check for loose connections.
11. Pump may be too hot.
A. Check line voltage; if less than 90% or more than 110% of rated volt-
age consult a licensed electrician.
B. Increase ventilation.
C. Reduce ambient temperature.
D. Tighten any loose connections.
MECHANICAL TROUBLES AND NOISE
1. If suction and discharge piping are not adequately supported, pump as-
sembly will be strained. See “Installation”, Page 4.
2. Do not mount pump on a wooden platform! Securely mount on concrete
platform for quietest performance.
Hazardous voltage.
Can shock, burn,
or cause death.
Disconnect power
before working
on pump or motor.