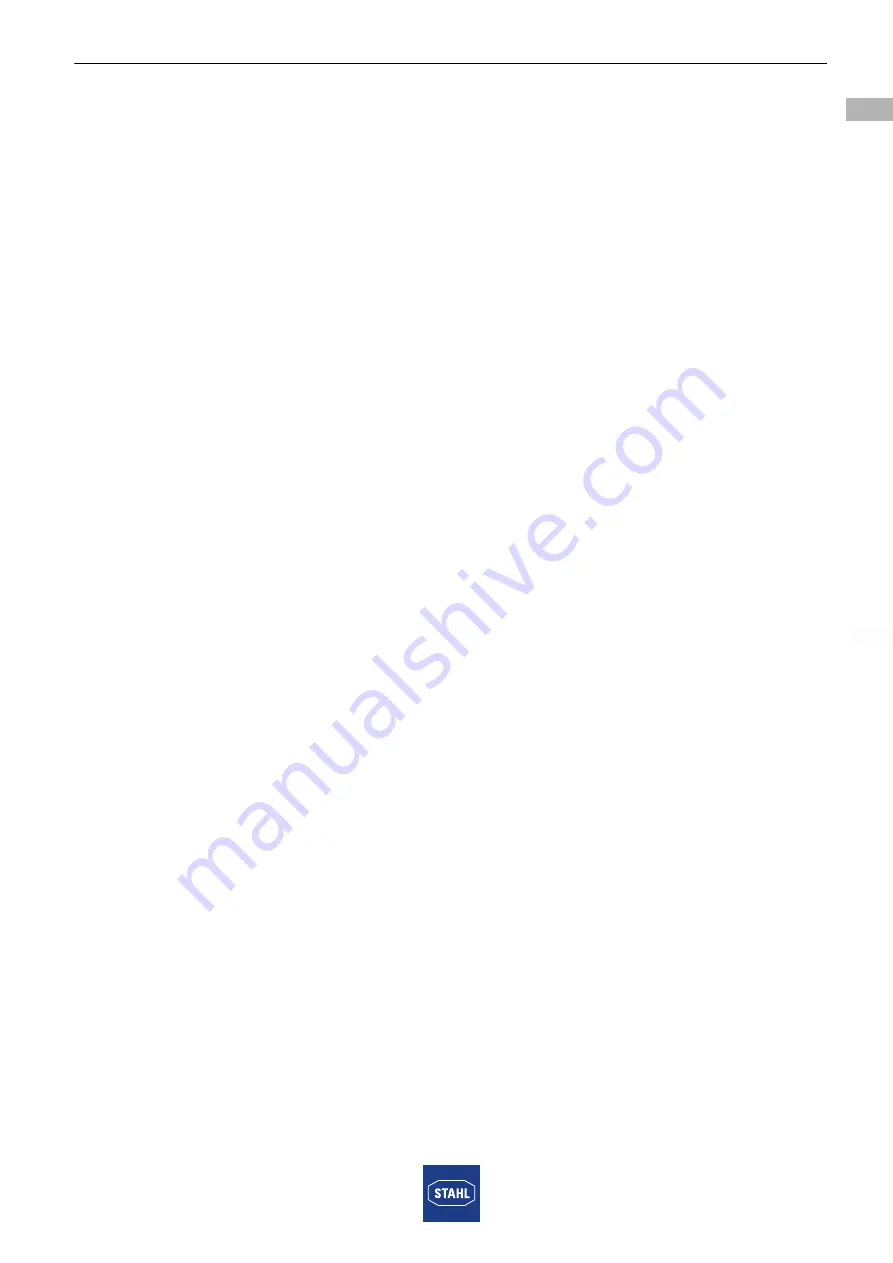
202161 / 815060300020
2016-12-13·BA00·III·en·05
Commissioning
19
EN
EN
EN
EN
EN
EN
EN
EN
EN
EN
EN
EN
EN
EN
EN
EN
EN
EN
EN
EN
EN
EN
EN
EN
EN
Terminal Box
Series 8150/1, Series 8150/2
Clearance and creepage distances of intrinsically safe components
Make sure that the creepage distances and clearances between the uncoated, conductive
parts of connection terminals of separated, intrinsically safe circuits to earthed or
potential-free, conductive parts is equal or greater than the values of EN IEC 60079-11,
Table 5.
For separated, intrinsically safe electric circuits, set up a safe distance between
the uncoated, conductive parts of external connections, which meets the following
requirements:
• minimum 6 mm between the separated, intrinsically safe circuits
• minimum 3 mm to earthed parts if possible connection to earth has not been considered
in the safety analysis.
7
Commissioning
Before commissioning, carry out the following checks:
Check the enclosure for damage.
Check that mounting and installation have been performed correctly. When doing so,
check whether all covers and partitions for live parts have been installed and fastened.
Make sure that all openings/drilled holes in the enclosure are sealed with permissible
components. Dust and transport protection (adhesive tape or plastic caps) fitted at
the factory must be replaced with certified components.
Make sure that seals and sealing systems are clean and undamaged.
If necessary, remove foreign bodies.
If necessary, clean the connection chamber.
Check whether all prescribed tightening torques have been observed.
8
Maintenance, overhaul, repair
Observe the relevant national regulations in the country of use, e.g. EN IEC 60079-14,
EN IEC 60079-17, EN IEC 60079-19.
8.1
Maintenance
Check the following points in addition to the national regulations:
• whether the clamping screws holding the cables are securely seated,
• whether the device enclosure and / or protective enclosure have cracks or other visible
signs of damage,
• compliance with the permitted temperatures,
• whether the nut is securely seated.
8.2
Maintenance
Perform maintenance on the device according to the applicable national regulations
and the safety notes in these operating instructions (chapter 3).
8.3
Repair
Perform repairs to the device only using original spare parts and after consulting with
R. STAHL.