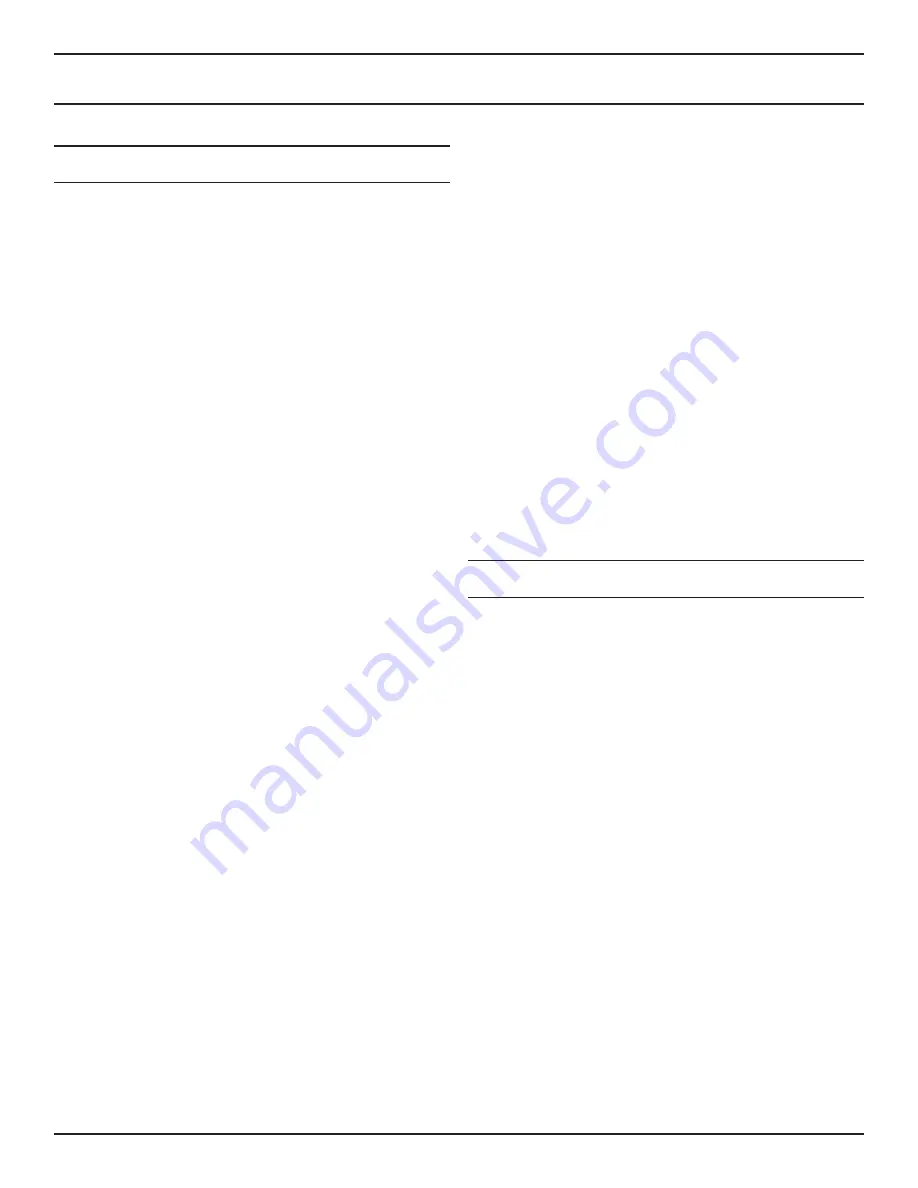
14
PREOPERATION PROCEDURES
HYDRAULIC SYSTEM REQUIREMENTS
The hydraulic system should provide a
fl
ow of 10-14
gpm/38-53 Ipm at an operating pressure of 1500-2000 psi/
105-140 bar. Recommended relief valve settings are 2100-
2250 psi/145-155 bar.
The system should have no more than 250 psi/17 bar back-
pressure measured at the tool end of the operating hoses.
The system conditions for measurement are at maximum
fl
uid viscosity of 400 ssu/82 centistokes (minimum operat-
ing tem peratures).
The hydraulic system should have suf
fi
cient heat rejection
capacity to limit the maximum oil temperature to 140° F/60°
C at the maximum ex pected ambient temperature. The
recommended minimum cooling capacity is 7 hp/5.22 kW at
a 40° F/22° C difference between ambient temperature and
oil temperature.
The hydraulic system should have a minimum of 25 micron
fi
ltration. It is recommended that
fi
lter elements be sized
for a
fl
ow of at least 30 gpm/114 Ipm for cold temperature
startup and maxi mum dirt holding capacity.
The hydraulic
fl
uid used should have a vis cosity between
100 and 400 ssu/20 and 82 cen tistokes at the maximum
and minimum expected operating temperatures. Petro-
leum based hydraulic
fl
uids with antiwear properties and a
viscosity index over 140 ssu/28 centistokes will meet the
recom mended requirements over a wide range of oper ating
temperatures.
The recommended hose size is .625-inch/16 mm I.D. up to
50 ft/15 m long and .750-inch/20 mm I.D. minimum up to
100 ft/30 m long.
CHECK POWER SOURCE
1. Using a calibrated
fl
owmeter and pressure gauge, check
that the hydraulic power source develops a
fl
ow of 10-14
gpm/38-53 Ipm at 1500 -2000 psi/105-140 bar.
2. Make certain that the hydraulic power source is equipped
with a relief valve set to open at 2100 -2250 psi/145-155
bar.
CONNECT HOSES
1. Wipe all hose couplers with a clean lint-free cloth before
making connections.
2. Connect the hoses from the hydraulic power source to
the tool
fi
ttings or quick disconnects. It is good practice to
connect return hoses
fi
rst and disconnect them last to mini-
mize or avoid trapped pressure within the tool.
3. Observe the arrow on the couplers to ensure that the
fl
ow is in the proper direction. The female coupler on the
tool hose is the inlet (pressure) coupler.
4. Move the hydraulic circuit control valve to the “ON” posi-
tion to operate the tool.
Note:
If uncoupled hoses are left in the sun, pressure in-
crease inside the hose may make them diffi cult to con-
nect. Whenever possible, connect the free ends of the
hoses together.
OPERATING PROCEDURES
The following are general wood cut ting procedures and
techniques. Dif ferences in the terrain, vegetation, and type
of wood will make this infor mation more or less valid for
particu lar areas. For advice on speci
fi
c woodcutting prob-
lems or techniques for your area, consult your local Stanley
representative or your county agent. They can often pro-
vide infor mation that will make your work safer and more
productive.
CUTTING TIPS
1. Check the lean of the tree. Tie a weight to a piece of
string about 2 feet long. Hang the weight in your line of
sight. The string is a good vertical line to help you judge the
lean of the tree. The tree should fall the way it is leaning.
Trees that are straight (leaning no more than 5 degrees)
gener ally can be felled in any direction.
2. Avoid felling across another tree, log, rocks, gulley or
ridge. Do not fell straight uphill or down hill. Fell the tree di-
agonally to the hill. Consider the wind direction and velocity.
Do not attempt cutting in strong winds.
3. Check the weight distribution. A tree is heavier on the
side with the most limbs. It will try to fall on its heavy side.
Trim a few limbs to “balance” the tree.
OPERATION
Summary of Contents for CS11
Page 2: ...2 ...
Page 22: ...22 CS11 PARTS ILLUSTRATION ...