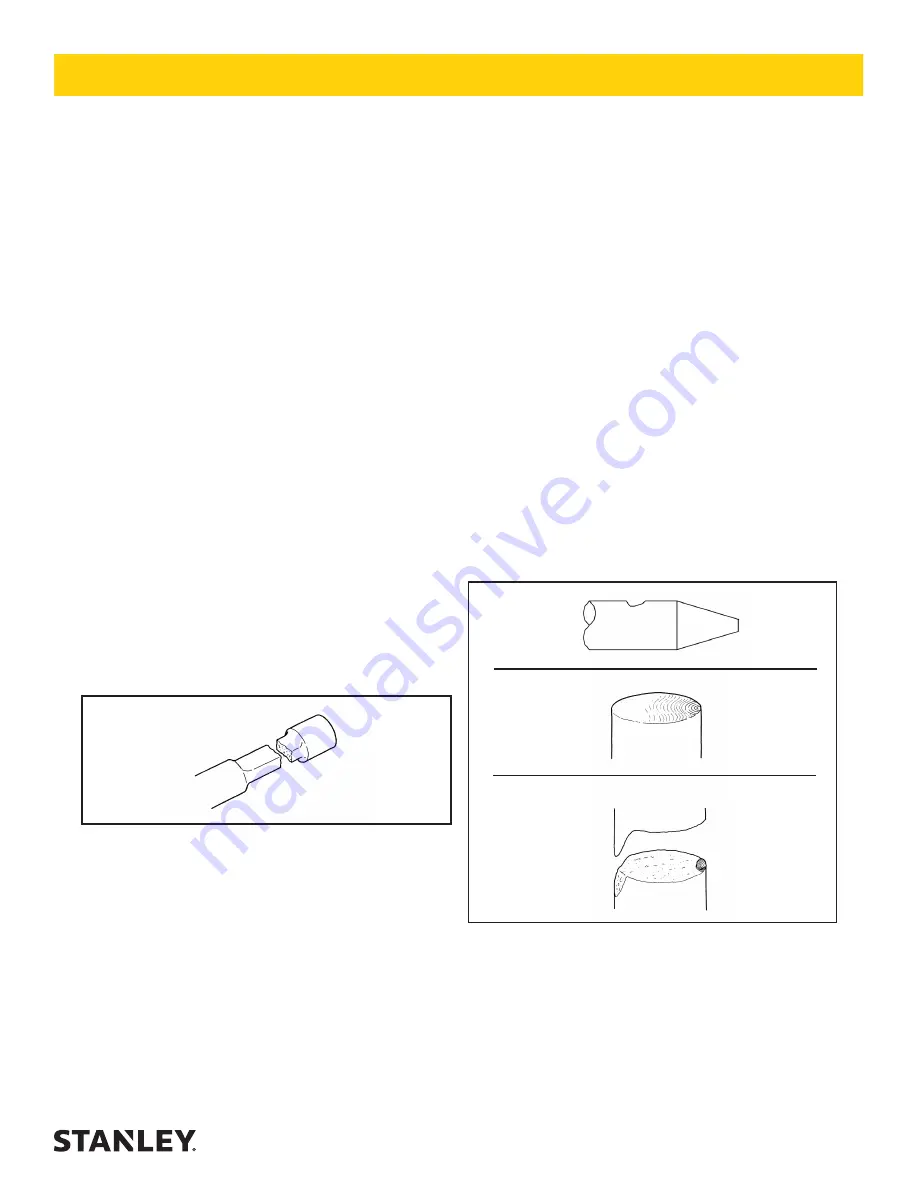
MB05 User
Manual ◄ 19
METAL-TO-METAL CONTACT
Extreme caution should be used to avoid scratches or
gouges on the surface of the tool. These areas create a
stress concentration Metal-to-Metal Contact point, thus
weakening the tool.
Another form of metal-to-metal contact is galling, which
usually occurs from the lack of lubrication. Special care
should be taken to keep the tool shank lubricated every
two (2) to three (3) hours.
Steel failures that were caused by surface damage take
two main forms. The simplest form is caused by deep
scratches on working steel surface. The broken surface
has a shell pattern around the starting point of failure,
similar to the one in the fatigue failure. The other parts of
the broken surface are brittle. These failures work slowly
through the steel until it suddenly parts completely.
The second form of failure caused by surface damage
occurs when there are deep scratches on working steel
surface and there was also excessive bending stress.
The broken surface also shows the shell pattern, but the
other parts of the broken surface are brittle and usually
have a “lip” like that in a stress failure.
Tool bits are made and heat treated to specification.
Tool bits, however well made, are wear parts, and are
used in the most destructive applications. Even when
the hydraulic breaker is used properly, and the operator
is an experienced one, a tool bit may become damaged.
When a tool bit has been damaged, it is useful to de-
termine the cause immediately in order to prevent the
damage from occurring again.
All Stanley tool bits are machined and hardened for
maximum performance. Care must be taken to maintain
the tools original condition for optimum productivity and
life expectancy. It is not uncommon for an operator who
is unfamiliar with using a hammer to break a point. This
is part of the learning experience.
Listed below are several methods to determine tool fail-
ure and will quickly aid in warranty determination.
TOOL FAILURE NOT COVERED
UNDER WARRANTY
BLANK FIRING OR FREE RUNNING
This occurs when the tool is not in proper contact with
the work, thus causing the energy produced by the ham-
mer to be concentrated on the tool retainer(s) and the
retainer slot(s) on the tool itself. Caution should be used
to prevent the hammer from sliding off slanted surfaces
or when breaking through thin material.
The illustration below is typical of the kind of breakage
that occurs from excessive blank firing.
WORN-OUT FRONT BUSHING(S) OR
RETAINER PIN(S)
Worn-out front bushing(s) will cause the tool to become
misaligned inside the hammer. This misalignment will
cause uneven contact between the piston and tool, thus
causing stress to concentrate on one particular area of
the tool. This can also cause the tool to bind inside the
hammer. Call your dealer for acceptable wear allow-
ances.
Worn-out retainer pin(s) will cause uneven loading on
the pin(s) themselves, causing failure of the tool or re-
tainer pin(s). This will also cause excessive wear to the
front bushing(s).
PROPER CARE OF TOOL BITS
Summary of Contents for MB05
Page 35: ......