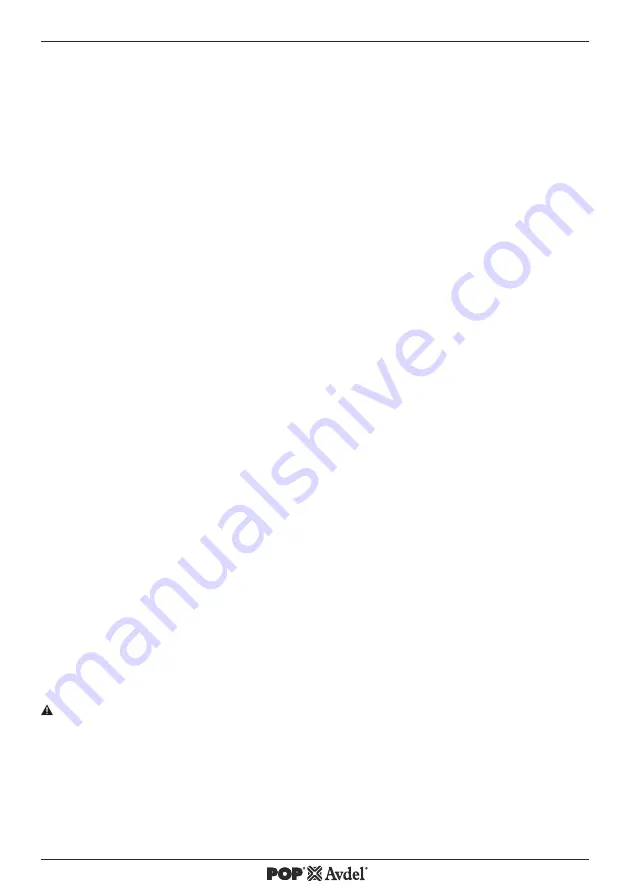
Before priming, empty the oil from tool as follows.
•
Switch OFF air supply at ON/OFF Valve (
7
.)
•
Remove all nose equipment (
1
.) Refer to section 3.1.
•
Remove Bleed Screw (
4
)
and Seal (
5.
)
•
Invert tool over suitable container, switch ON air supply at ON/OFF Valve (
7
)
and actuate tool.
•
Residual oil in the tools hydraulic system will empty through bleed screw orifice.
CARE SHALL BE TAKEN TO ENSURE THAT THE BLEED HOLE IS NOT DIRECTED TOWARDS THE OPERATOR
OR OTHER PERSONNEL.
•
Switch air supply OFF at ON/OFF Valve (
7
.)
•
Screw priming pump (07900-00700) into bleed screw port, utilizing Seal (
5
.)
•
Actuate Priming Pump by pressing down and releasing several times until resistance is evident and the
Head Piston starts to move rearward.
ENSURE PUMP IS KEPT ‘SQUARE’ TO BLEED SCREW PORT DURING PRIMING OPERATION TO PREVENT
BREAKAGE OF BLEED NIPPLE ON PRIMING PUMP.
•
Remove the priming pump, surplus oil will expel from bleed screw port.
•
Replace the Bleed Screw (
4
)
together with Seal (
5.
)
•
Switch ON air supply at ON/OFF Valve (
7.
)
•
Check that the stroke of the head piston reaches specification. If not repeat above procedure.
•
Switch OFF air supply and refit nose equipment. Refer to section 3.1.
•
Check that the stroke of the tool meets the minimum specification of 26 mm.
•
To check the stroke, measure the distance between the front face of the Jaw Guide (
1g
) and the front
of the Head (
12
), BEFORE pressing the trigger and when the trigger is fully actuated. The stroke is the
difference between the two measurements. If it does not meet the minimum specification, repeat the
Priming Procedure.
6. Maintenance
I M P O R TA N T
SAFETY WARNINGS APPEAR ON PAGE 7 & 8.
THE EMPLOYER IS RESPONSIBLE FOR ENSURING THAT TOOL MAINTENANCE INSTRUCTIONS
ARE GIVEN TO THE APPROPRIATE PERSONNEL. THE OPERATOR SHOULD NOT BE INVOLVED
IN MAINTENANCE OR REPAIR OF THE TOOL UNLESS PROPERLY TRAINED.
Every 500,000 cycles the tool must be completely dismantled and inspected Components must be replaced
where worn or damaged. All O rings and seals should be replaced with new ones and lubricated with
Molykote 55M grease (07992-00075) for pneumatic sealing or Molykote 111 (07900-00755) for hydraulic
sealing.
WARNING
The airhose must be disconnected before any servicing or dismantling is attempted unless specifically
instructed otherwise.
The dismantling operation must be carried out in clean conditions.
Before proceeding with dismantling, empty the oil from the tool as follows.
Before priming, empty the oil from tool as follows.
ENGLISH
17