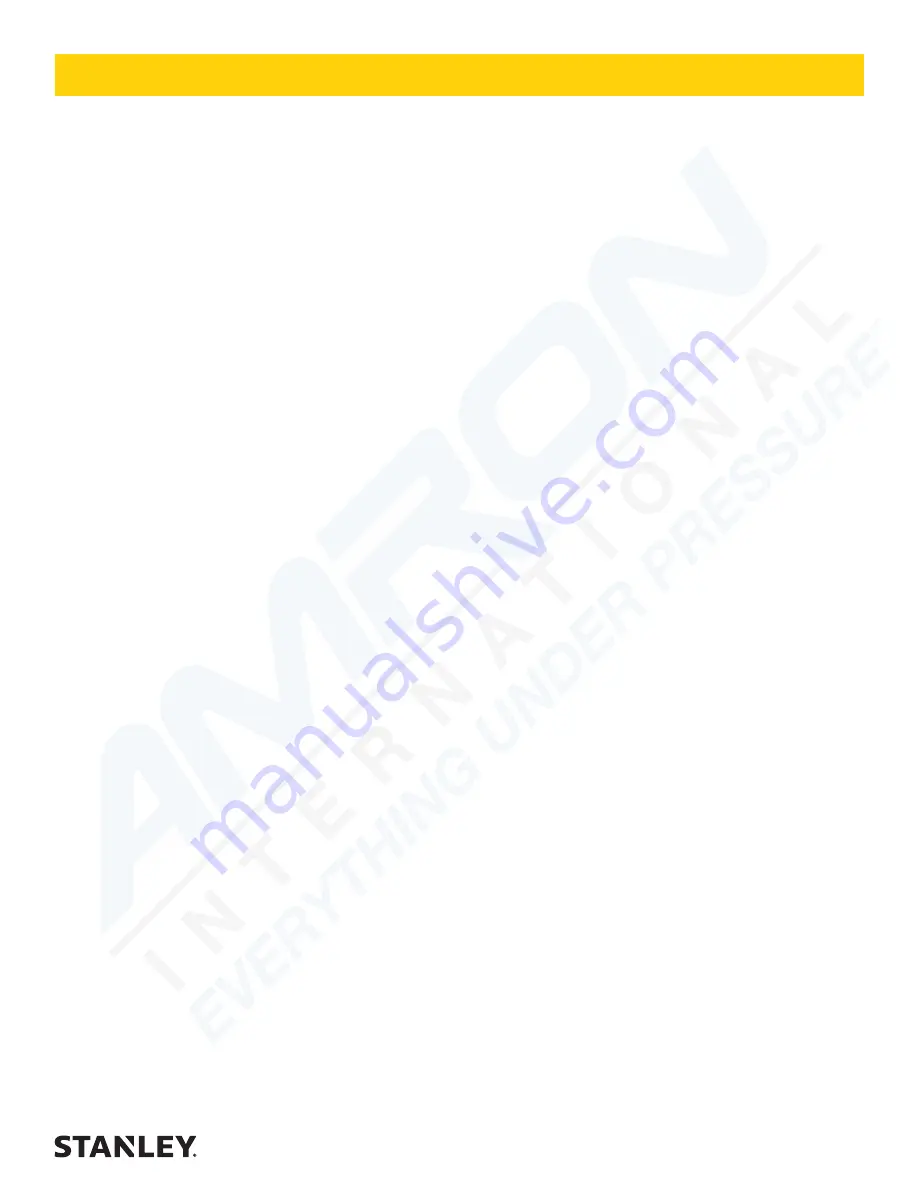
SRP 6570 User
Manual ◄ 7
SAFETY
Machine control
Operating devices which adjust themselves automatically when re-
leased in normal use, must not be locked.
Check protective devices and brakes for proper functioning prior
to operation.
When reversing, particularly on the edges and banks of ditches,
as well as in front of obstacles, the machine operator cannot fall or
be crushed.
Always keep a safe distance away from the edges and banks of
ditches and refrain from any actions which could cause the ma-
chine to topple over!
Always control the machine, so that hand injuries through hard
objects are avoided!
Always ascend slopes carefully in a direct path.
Reverse up steep slopes to prevent the machine from toppling over
on to the machine operator.
If faults on the safety devices or other faults detrimental to the safe
operation of the machine are noticed, operation of the machine
must be stopped immediately and the faults remedied.
When undertaking compaction work in the vicinity of buildings or
above pipelines and similar, check the effect of the vibrations on
the buildings and pipes and stop compaction work if necessary.
Parking the machine
Park the machine on a firm and level surface.
Shutdown the drive and secure it to prevent accidental movement
and unauthorized use. If available, close the fuel valve. Do not
place or store equipment with integrated moving gear on the
chassis. The moving device is intended only for transportation
purposes.
Filling Fuel
Only fill fuel by switched-off motor. No open fire, do not smoke.
Do not spill any fuel, collect discharging fuel in a suitable
container, prevent fuel from seeking into the soil.
Ensure that the filler cap is tight.
Leaky fuel tanks constitute an explosion hazard and must
therefore be replaced immediately.
Maintenance and repairs
Observe the maintenance, inspection and adjustments and inter-
vals specified in the operating instructions, as well as the informa
-
tion for part replacement.
Maintenance work must be undertaken only by qualified and
authorised persons.
Maintenance and repairs only by switched-off drive.
Only carry out maintenance and repairs when the machine is
parked on a firm and even surface and is secured to prevent it from
rolling.
When changing larger assemblies and individual components, only
use suitable and perfectly functioning hoisting and lifting gears with
suitable loading capacity. Attach and secure parts on hoisting care-
fully!
Spare parts must comply with the technical requirements of the
manufacturer. Therefore only use original spare parts.
Hydraulic lines must previously be rendered pressureless, before
working on them. Hydraulic oil discharging under pressure can
cause serious injuries.
Replace externally damaged hydraulic hoselines at regular inter-
vals (depending on time used), even when no safety-relevant faults
are visible.
Before working on the electrical system of the machine, discon-
nect the battery and insulate by covering or remove.
Inspect the electrical equipment of the machine at regular intervals.
Faults such as loose connections, worn or scorched cables must
be immediately eliminated.
During transport, secure the battery to prevent it from tilting, short-
circuit, slipping and damage.
Dispose of used batteries in a proper manner. Do not place any
tools on the battery.
Handling acid-batteries
Transport filled batteries upright to prevent acid spillage.
Keep away from sparks, open fire and other sources of ignition.
Avoid contact of acid with skin and clothing. In case of contact,
wash off acid immediately with clear water and go to medical in-
stitution.
Properly refit and inspect all protective devices after maintenance
and repairs.
Disposal of the machine after finish of its service life
At disposal of the machine after finish of its service life, the owner
is obliged to comply with national regulations and laws on wastes
and protection of environment. Therefore we recommend in such
cases to contact the following:
• professional specialized companies engaged in such activities
and having the relevant certificate
• the manufacturers or contracting service organizations
authorized by him.
The manufacturer is not responsible for damages to health of own-
ers neither for damages to the environment in events of failing to
comply with above mentioned hygienic and ecological principles.
Testing
Road rollers, trench rollers and vibrating plates must be tested for
safety by an expert depending on the particular application and
operating conditions as required, however at least once a year.
Work on hydraulic devices must be undertaken only by persons
with a special knowledge of hydraulics and the necessary experi-
ence!
Do not adjust pressure relief valves.
Drain hydraulic oil at operating temperature—caution risk of
scalding!
Collect discharging hydraulic oil and dispose of the same in an
environmentally-friendly manner.
Do not start the motor when hydraulic oil has been drained off.
After completing all work (by pressureless system), inspect all
connections and bolted connections for leaks.
Inspect all hoses and bolted connections for leaks at regular
intervals and any externally visible damage! Rectify any damage
immediately.