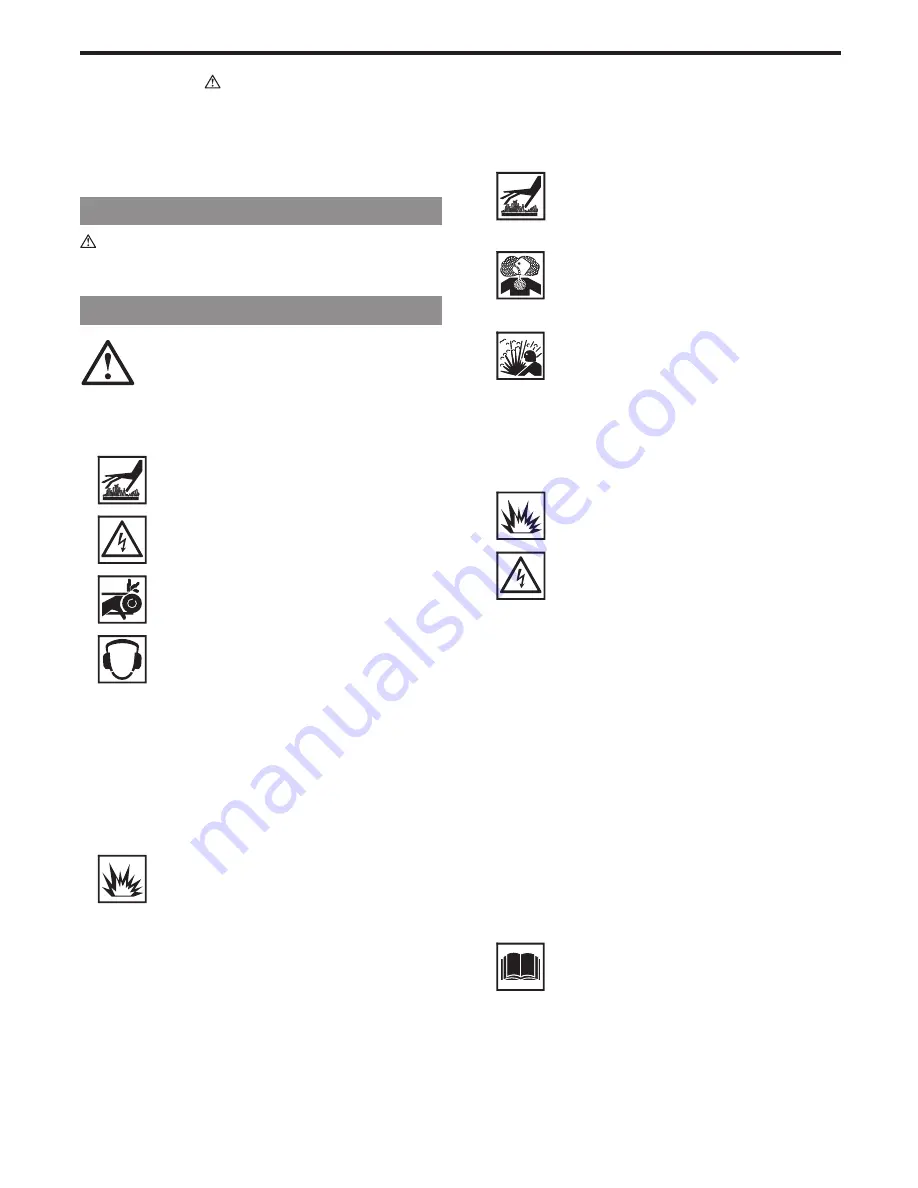
4
• ENGLISH
IMPORTANT
This instruction manual provides important installation, use,
maintenance and safety information and must be at hand at all
times. Before operating this equipment, read this manual and
make sure you understand all of its instructions in order to
avoid personal injuries or damage to your piston compressor.
Warning!
Read and understand all instructions. Failure to
follow all instructions listed below, may result in electric shock,
fire and/or serious personal injury.
SAFETY INSTRUCTIONS
If an Air Compressor is improperly used it may
cause physical and material harm. In order to avoid
them, follow the recommendations below:
1.
This equipment:
►Has hot, electric and moving parts;
►When connected to electric power, it may turn on
or turn off automatically due to tank’s pressure or
to the tripping of electric protectionelements;
►May cause mechanical or electric interferences
in nearby equipment;
►Must not work in places where non authorized
people, children or animals may have access;
►Requires an authorized person to supervise its
use and maintenance as well as the use of ad
equate individual protection equipment.
►Must be installed and operated in well ventilated
areas and protected against humidity or water
leakage.
2.
Never exceed the maximum pressure indicated in
the compressor’s identification tag/sticker.
3.
Do not change the pressure switch safety valve factory
adjustment. If any adjustment to the pressure switch is
needed, call the nearest
Stanley
Black&Decker
Authorized
ServiceCenter.
4.
Never weld or carry out maintenance jobs on the
tank, once they may affect its resistance or may hide
more serious problems. In case of leakage, cracks
or deterioration caused by corrosion, stop using
the equipment immediately and get in touch with the
nearest
Stanley
Black&Decker
Authorized Service Center.
5.
Never run the tank above the maximum pressure indicated
on its identification tag.
6. The end user must provide a new inspection of the
Pressure Vessel (tank) to be carried out after 5 (five)
years from the manufacturing date shown in its
identification tag, or when there is chemical or mechanical
damage that may endanger its resistance. The inspection
must be carried out and approved by a duly qualified
engineer (skilled professional), according to local
technical standards and legislation. The next period for
testing will be determined by the responsible engineer
himself. We recommend that the Pressure Vessel (tank)
be exchanged for a new one every 10 (ten) years, or
according to the responsible engineer’s judgment.
7.
Air compression is a heat generating process and
parts and accessories are subject to high
temperatures. Therefore, one must be careful
when handling them in order to avoid burns.
8.
The produced compressed air is not adequate for
human consumption. To use it for this purpose, it
is necessary to install special filters. Please
contact
Stanley
Black&Decker
for aditional information.
9.
Do not carry out any maintenance while the
compressor is on. Do not clean or touch the
electric components without unplugging the
compressor from the outlet.
10.
The refrigeration air intake protecting screen must be
always clean to prevent the propeller from pulling in impurities.
11.
Never clean the compressor’s external surface with solvent
(thinner). Always use neutral detergent.
12.
Avoid the accumulation of solvents, paints or
other chemicals that may cause damage or
explosion risk to the compressor.
13.
Always use an electric extension cord according
to specifications
(see Table 2 - Page 21)
which
must not be amended. If these recommendations
are not followed, the user may be injured and the
compressor’s electric components may be
damaged, violating the warranty. When necessary,
use a longer air hose.
14.
If the equipment presents any irregularities, stop its use
immediately and call the nearest
Stanley
Black&Decker
Authorized Service Center.
WELCOME
You have purchased another product with
Stanley
Black&Decker
quality standards.
The design, inspection and manufacturing of your
Stanley
Black&Decker
tank is based on
EN286-1 1998
Attachment 1.
It is a mix of high technology and easy use.
INTRODUCTION
WE RECOMMEND READING THIS MANUAL PRIOR
TO USING THIS PRODUCT.
It will help you to optimize product performance, guarantee
safe use and guide you in preventive maintenance.
If there is any problem that cannot be solved by the
information provided in this manual, please contact the
nearest
Stanley
Black&Decker
Authorized Service Center.
In order to extend the useful life of this coaxial air compressor,
the use of mineral lubricant oil and original parts are highly
recommended.
GENERAL SAFETY RULES
SAVE THESE INSTRUCTIONS
INTRODUCTION