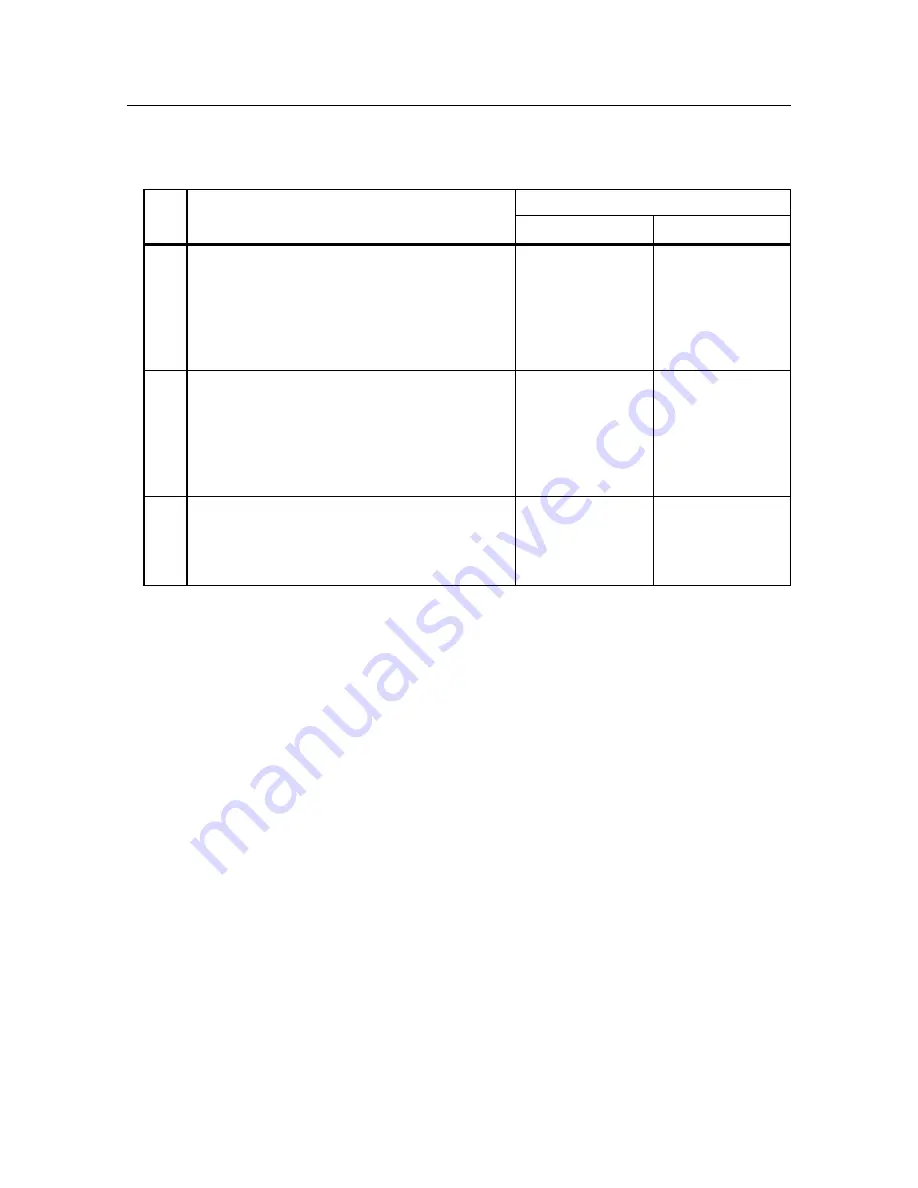
– 120 –
TROUBLESHOOTING
2.4 E5
Step
Check
Remedy
YES
NO
1
(Initial Check)
Are any parts broken, malformed, incorrectly installed
or different from those listed in the specifications?
• Principle Parts to be Checked:
(1) MCU PWB, (2) HVPS assembly
(3) Interlock access pin
2
(Check the interlock access pin.)
Does the interlock access pin push in the interlock
switch in the HVPS assembly when the front cover
assembly is closed, and does it release the interlock
switch when the front cover assembly is opened?
(Check by listening for the click sound.)
3
(Check the interlock access switch in the HVPS
assembly.)
Is the interlock access switch functioning properly?
• Check using diagnosis code 02.
Replace the part or
install the part
correctly.
See step 2.
See step 3.
Replace the front
cover or the HVPS
assembly.
Replace the MCU
PWB.
See section 3.2
Faulty HVPS
Assembly 24VDC.
Summary of Contents for WinType 4000
Page 1: ...WinType 4000 TECHNICAL MANUAL SECOND EDITION LASER PRINTER ...
Page 4: ......
Page 6: ... 2 GENERAL SPECIFICATIONS ...
Page 14: ... 10 THEORY OF OPERATION ...
Page 26: ... 22 THEORY OF OPERATION Figure 2 9 Electrical ...
Page 28: ... 24 REPLACEMENT AND ADJUSTMENT OF PARTS ...
Page 62: ... 58 REPLACEMENT AND ADJUSTMENT OF PARTS ...
Page 64: ... 60 MAINTENANCE GUIDE ...
Page 114: ... 110 MAINTENANCE GUIDE ...
Page 116: ... 112 TROUBLESHOOTING ...
Page 176: ... 172 5 ELECTRICAL 5 1 Disassembly Drawing 1 2 3 4 14 4 14 2 14 1 14 3 13 12 11 6 5 7 8 9 10 ...
Page 179: ......