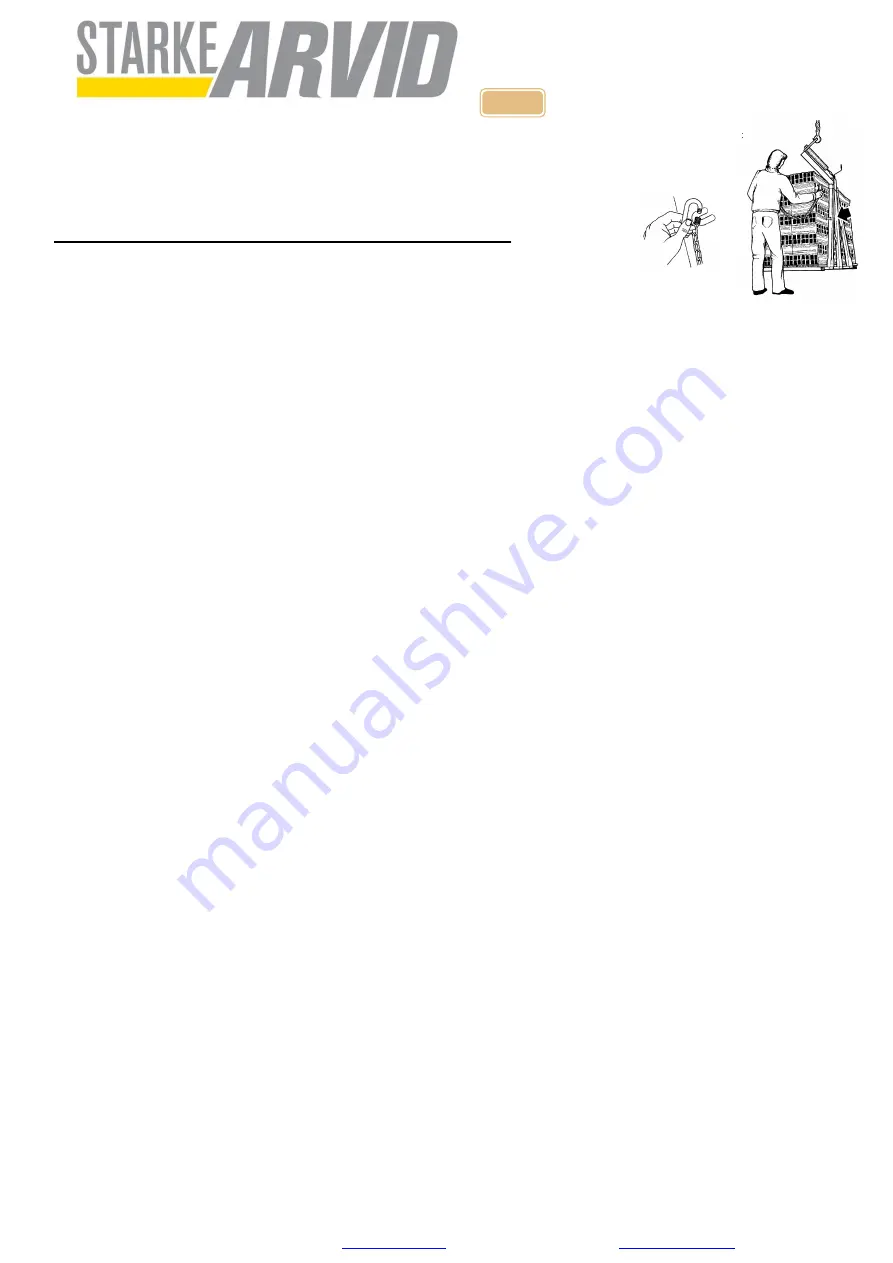
Starke Arvid AB
Lyckåsvägen 3 Tel: +46 522 - 22 000 Fax: +46 522 - 22 344
SE-459 30 Ljungskile
8
•
Having forked the load, before starting to lift it, secure it with a chain or belt, suitable for this purpose,
to the specific hooks placed on the side supports of the fork. The ends of the chains or belts must
be equipped with an anti-unhooking device and the length must ensure the right tension during the
transport operational phase.
Safety precautions to conduct with anchoring system using belt
-
Before use always visually inspect anchorage.
-
Never use if damaged (for example cuts on belt and/or deformations on metal
parts).
-
Comply with the tensioning value planned for anchorage.
-
Use edge guards on sharp edges.
-
Avoid exposure to heat sources over 100°C.
-
Do not knot or twist the belt.
•
When moving and lifting materials, avoid abrupt acceleration and jolts. Increase speed progressively and use the
buzzer alarm on the crane to signal the start of the movement operations.
•
Avoid using the equipment to strap or pull any object, since the equipment was designed to support loads in a vertical
position. This manoeuvre may be dangerous.
•
When the work phase is complete, ensure the fork points are free of any types of material.
Non-compliance with the aforementioned instructions may create dangerous situations and/or damage the
equipment, making it unsafe.
6.
MAINTENANCE AND REPLACEMENT OF COMPONENTS SUBJECTED TO NORMAL WEAR
•
A control must be conducted by previously assigned, trained and qualified staff on the use of the load hold moving
equipment (forks and pliers), it being understood that employees must be trained to work on the crane.
•
The control on the information, training and qualifications provided must be backed up by a report on the training
provided, kept by the contractor.
•
Any maintenance or service operations must be conducted with the equipment resting on the ground in a stable
position.
We recommend that checks of the efficiency and good maintenance of the materials constituting these accessories are
carried out at least on a quarterly basis.
Remember also that on the basis of the above, if reductions greater than 10% are detected in the section of the
constituent elements of the accessories, the accessory must be replaced. This replacement must be carried out also
when, as a result of stress, the material exceeds its elastic capacity with a permanent effect.
6.1. Ordinary maintenance
The fork lift must be compulsorily inspected:
•
whenever it is removed from the warehouse and every day before start up in the worksite;
•
after a repair;
•
during the service life of the equipment.
Control of the equipment is necessary to ensure the efficiency of the equipment and consists of:
•
Checking there are no cracks in the welding;
•
Checking the range conditions of the pivots and in particular point alignment;
•
Checking for breakages and/or deformations on the metal structure;
•
Checking the conditions of the screws and correct tightening of the nuts;
•
Checking the status of the spring, where present, in particular any cracks that can occur with onerous use;
•
Periodically greasing the regulation locking wheel on the models versions MB and MBA and versions MBCR and
MBACR;
•
Replacing the worn parts with original replacement parts provided by the manufacturing company.
In the case any anomalies are detected contact the manufacturer for the servicing of the device. Operations
conducted incorrectly make the equipment dangerous. All repair and servicing
of the forks must be performed by
qualified personnel at our facilities. The use of aftermarket
parts may compromise the safety of the device, as well
as invalidate the CE compliance of the equipment.