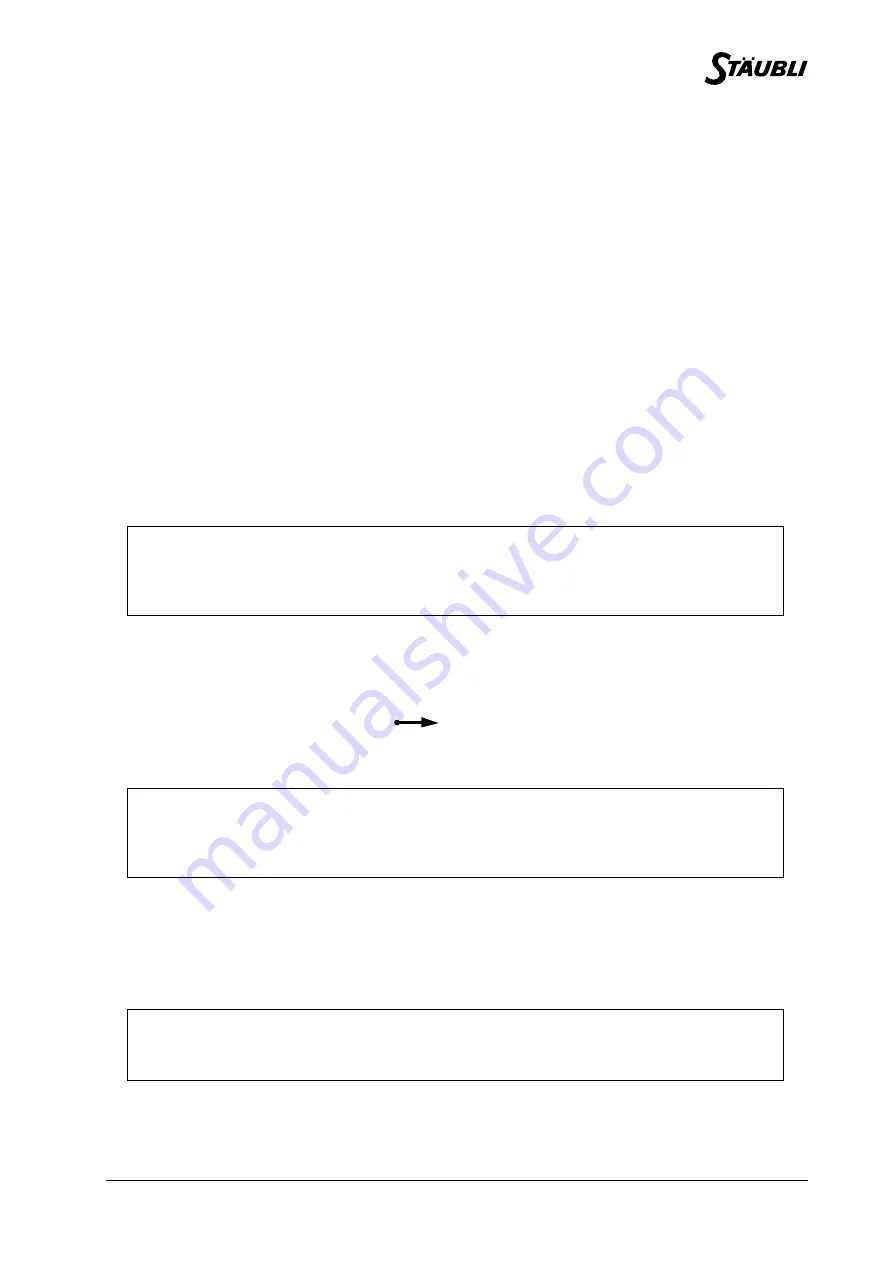
Chapter 1 – Description
D18326204C - 11/2004
21
1.6.
USER CIRCUIT
The electric wiring of the arm is assembled into a harness including several cables supplying the motors
(power, brakes, resolvers), the solenoid valves, the limit switches and user connector. These components
are connected by means of removable connectors.
The harness also includes pneumatic hoses which supply air to the solenoid valves (
EV1
and
EV2
).
The robot also has a pressure source (
P2
) close to the tool clamp.
The outlets of the solenoid valves
EV1
and
EV2
are on the forearm:
•
A1
and
B1
for solenoid valve
EV1
.
•
A2
and
B2
for solenoid valve
EV2
.
Figure
is for all robots except the clean room application.
Figure
is for clean room application robots.
The wiring is inside the structure and routed through the centre of the joints. It is connected to the arm base
on a plate which includes several electrical and pneumatic components such as:
Figures 1.11 and 1.12:
• Arm/controller connector
(1)
.
• R23 connector intended for the user for possible electrical connection of grip (
JOC
).
• Brake release selector
(3)
.
• Brake release pushbutton
(2)
.
• Compressed air network pneumatic (or vacuum) connections
P1
and
P2
.
• Pneumatic (or vacuum) exhaust muffler
.
• Arm ground connection
(4)
.
1.7.
RELEASING JOINT BRAKE
The controller must be switched on.
Place the brake release selector in position corresponding to the joint to be released.
Press the brake release pushbutton, the selected joint is totally free. When the pushbutton is released, the
brakes will then be engaged and the corresponding joint locked.
CAUTION:
When a connector is plugged to E10, there may be a risk of collision with the cover (5)
in some arm configurations.
CAUTION:
Do not add wires or cables to arm wiring as this may cause premature wear of the arm
electrical wiring and lead to loss of the warranty.
CAUTION:
Make sure that the arm and load relevant to this joint are suitably supported.
Summary of Contents for 90B family
Page 1: ...St ubli Faverges 2004 Arm RX series 90B family Characteristics D18326204C 11 2004...
Page 4: ...4 D18326204C 11 2004...
Page 6: ...6 D18326204C 11 2004...
Page 7: ...Chapter 1 Description D18326204C 11 2004 7 CHAPTER 1 DESCRIPTION...
Page 8: ...8 D18326204C 11 2004 Figure 1 1 B A C D E F 3 4 5 2 1 6 RX 90 RX 90 R...
Page 10: ...10 D18326204C 11 2004 Figure 1 2 Figure 1 3...
Page 12: ...12 D18326204C 11 2004 Figure 1 4...
Page 14: ...14 D18326204C 11 2004 Figure 1 5...
Page 16: ...16 D18326204C 11 2004 Figure 1 6 Effective tapped depth 8 mm...
Page 18: ...18 D18326204C 11 2004 Figure 1 7 Figure 1 8 Figure 1 9 Figure 1 10...
Page 22: ...22 D18326204C 11 2004 Figure 1 13...
Page 24: ...24 D18326204C 11 2004 Figure 1 14...
Page 26: ...26 D18326204C 11 2004 Figure 1 15 Figure 1 16 11 1...
Page 30: ...30 D18326204C 11 2004...
Page 31: ...Chapter 2 On site preparation D18326204C 11 2004 31 CHAPTER 2 ON SITE PREPARATION...
Page 32: ...32 D18326204C 11 2004 Figure 2 1...
Page 34: ...34 D18326204C 11 2004...
Page 35: ...Chapter 3 Installation D18326204C 11 2004 35 CHAPTER 3 INSTALLATION...
Page 36: ...36 D18326204C 11 2004 Figure 3 1 Figure 3 2 Figure 3 3 1 5 X L Y 2 P 7 H 6 3 4...
Page 38: ...38 D18326204C 11 2004 Figure 3 4 Figure 3 5 Figure 3 6 Figure 3 7 6 3 5 7 3...
Page 42: ...42 D18326204C 11 2004...