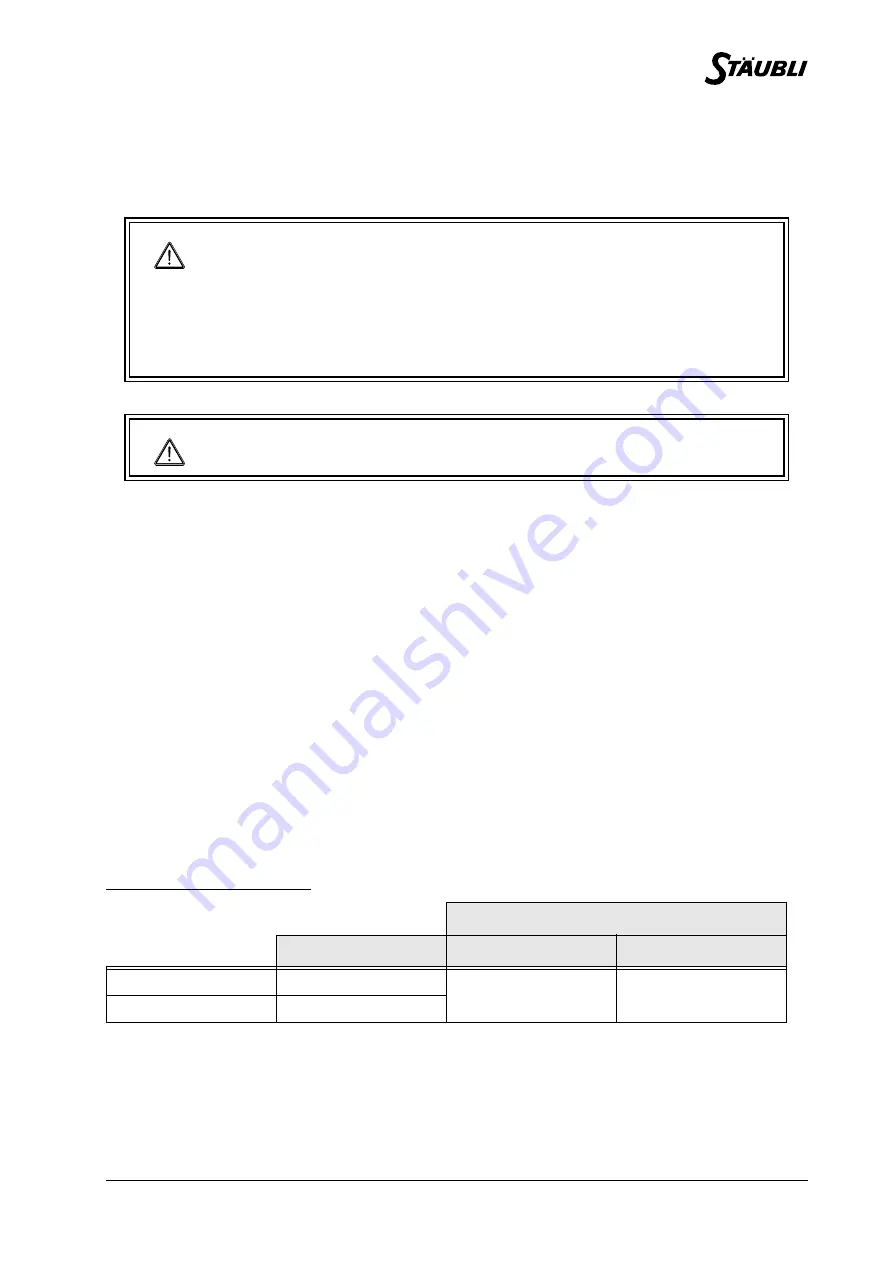
Chapter 2 – On-site preparation
D18326204C - 11/2004
33
2.1.
WORKING SPACE
The user is responsible for performing all preparatory work required to complete the on-site installation of
the robot. Working space must be sufficient, installation surface appropriate; power sources shall be
available (for electrical power, consult controller characteristics).
2.2.
ATTACHMENT
(figure 2.1)
The robot arm can be installed vertically, base downwards (floor-mounted version) or base upwards
(ceiling-mounted version). In all cases, it must be securely attached by 3 class 12.9 M12 hex. socket head
screws.
Attachment surface shall be flat and metallic. A deformable support will greatly reduce robot’s performance
in speed and accuracy.
To dimension the support, take into account the maximum loads generated by the arm in motion at point 0
which are:
• F
V
= 2232 N
• F
G
= 1635 N
• C
B
= 1700 Nm
• C
P
= 747 Nm
under following load conditions:
The user can accurately position the robot by means of two 10h8 diameter centering pins.
DANGER:
The arm's working area must be surrounded by a closed safety enclosure in
compliance with the country's safety legislation preventing personnel
accessing the dangerous area.
International standard: ISO 10218 (1992).
French standard: NF EN 775 (1993).
European Directive: machine directive CEE 89-392.
DANGER:
There must be no obstacles within the robot work envelope.
LOAD POSITION (mm)
LOAD (kg)
JOINT 5
JOINT 6
Standard arm
6
150
75
Long arm
3.5
Summary of Contents for 90B family
Page 1: ...St ubli Faverges 2004 Arm RX series 90B family Characteristics D18326204C 11 2004...
Page 4: ...4 D18326204C 11 2004...
Page 6: ...6 D18326204C 11 2004...
Page 7: ...Chapter 1 Description D18326204C 11 2004 7 CHAPTER 1 DESCRIPTION...
Page 8: ...8 D18326204C 11 2004 Figure 1 1 B A C D E F 3 4 5 2 1 6 RX 90 RX 90 R...
Page 10: ...10 D18326204C 11 2004 Figure 1 2 Figure 1 3...
Page 12: ...12 D18326204C 11 2004 Figure 1 4...
Page 14: ...14 D18326204C 11 2004 Figure 1 5...
Page 16: ...16 D18326204C 11 2004 Figure 1 6 Effective tapped depth 8 mm...
Page 18: ...18 D18326204C 11 2004 Figure 1 7 Figure 1 8 Figure 1 9 Figure 1 10...
Page 22: ...22 D18326204C 11 2004 Figure 1 13...
Page 24: ...24 D18326204C 11 2004 Figure 1 14...
Page 26: ...26 D18326204C 11 2004 Figure 1 15 Figure 1 16 11 1...
Page 30: ...30 D18326204C 11 2004...
Page 31: ...Chapter 2 On site preparation D18326204C 11 2004 31 CHAPTER 2 ON SITE PREPARATION...
Page 32: ...32 D18326204C 11 2004 Figure 2 1...
Page 34: ...34 D18326204C 11 2004...
Page 35: ...Chapter 3 Installation D18326204C 11 2004 35 CHAPTER 3 INSTALLATION...
Page 36: ...36 D18326204C 11 2004 Figure 3 1 Figure 3 2 Figure 3 3 1 5 X L Y 2 P 7 H 6 3 4...
Page 38: ...38 D18326204C 11 2004 Figure 3 4 Figure 3 5 Figure 3 6 Figure 3 7 6 3 5 7 3...
Page 42: ...42 D18326204C 11 2004...