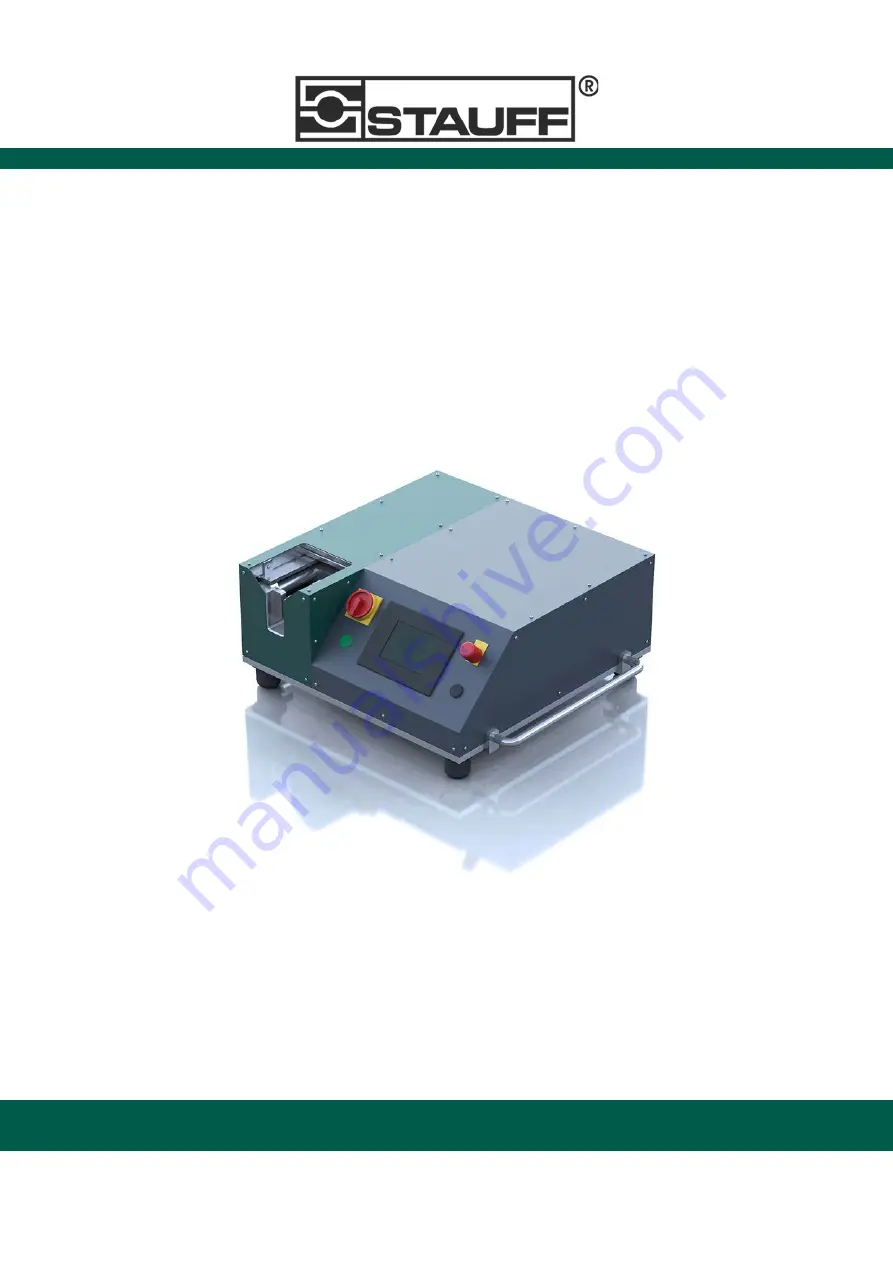
Operating instructions
Translation of the
original operating instructions
Machine for cutting ring
pre-assembly and final assembly
SPR-PRC-POC
R3.0, valid from firmware 3.6.x, 6010014620
22-10-2020
To avoid injuries and damage, read these operating instructions thoroughly
and attentively. Retain it for further reference.