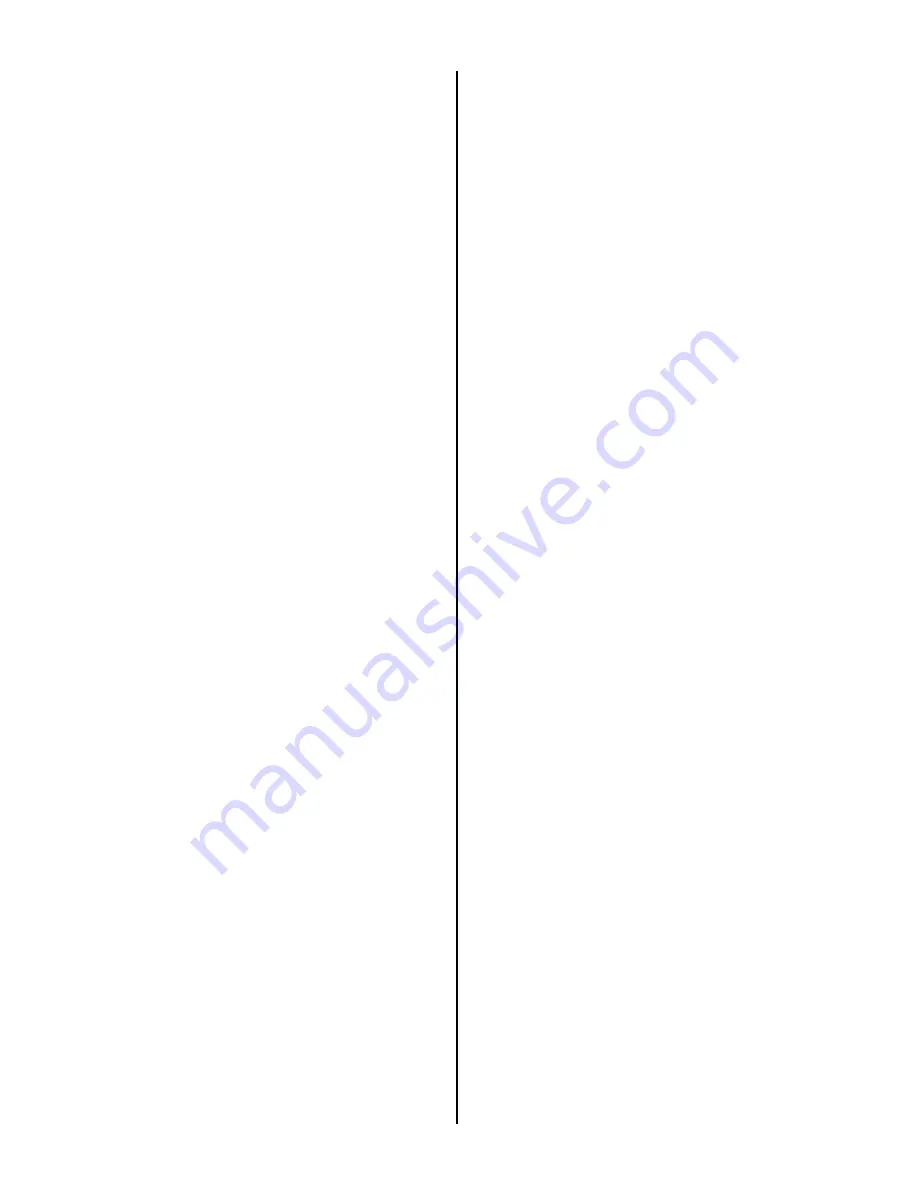
ELECTRICAL INSTALLATION
copper tubing is recommended. A shut-
off valve should be convenicnitly placed
in the water feed line.
Rough- in the steam line using 1/2" NPT
brass pipe or 3/4 " I. D. copper tubing. Do
not use iron pipe. it will rust and discolor
wall of steamroom. For a steam line that
is longer than 10 feet, insulation must be
used. The stearnhead location should be
approximately 12” to 18" above the
steamroom floor.
CAUTION: NO shut-off valve should be
installed on the steam line. Do not create
traps or valleys in this line which would trap
condensation and block the flow of steam.
The steam pipe should be pitched away from
the stearnhead allowing condensation to run
back into steam generator (Preferably) Or
pitched toward the steamhead.
Rough- in a 3/4" indirect waste line to be
used for the safety valve and drain. The in-
direct drain must be in accordance with lo-
cal plumbing codes.
2)
3)
C. Steam Generator Plumbing Installation
Care must be taken when installing the steam
generator. Leave proper access for servicing
(30'’ minimum each side). (Refer to Figure 2
for typical steam generator installation.)
CAUTION: The steam generator is designed
to be used ONLY in an upright and level posi-
tion ; to do otherwise would damage the unit
and void the warranty.
If needed mount the steam generator on a
platform to allow draining into a basin or
into previously installed indirect waste line.
NOTE: Optional automatic blowdown must
be piped into the 3/4" indirect waste line.
Connect the 3/4" NPT safety valve into ihe
previously installed indirect waste line.
In areas where high water pressure may be
a problem a water hammer arrestor should
be installed. Connect the water supply to
the steam generator connection marked
“water inlet”. (See Figure 1.)
Connect the steam line from the preViously
roughed-in location to the steam solenoid
valve on the generator marked .. steam out-
let”. (See Figure 1.)
1)
2)
3)
4)
In the steamroom. place the center of the
escutcheon onto the steam pipe and Screw
the stearnhead into place. Care must be
taken not to Scratch the stearnhead or es-
cutcheon with a wrench. Be Sure the steam
slot in the stearnhead is facing down.
After the plumbing connections are complete
the electrician may finish the wiring and test
the unit.
II. ELECTRICAL INSTALLATION
Electrical Pre- Installation
Proper electrical supply: see specification
label located above the drain valve (see Fig-
ure 1)Determine proper size of wire,voltage,
amperage. and phase for the steam genera-
tor.
Inline fuse/circuit breaker required: fu or
circuit breaker sized in accordance with
specification label. Do not install a (GFI)
Ground Fault interrupter to this equip-
ment.
B. Electrical Rough-In
Route power supply cable to the location the
steam generator will be installed before walls
are closed.
C. Steam Generator Electrical Installation
WARNING ALL POWER TO THE STEAM
GENERATOR MUST BE TURNED OFF.
Locate appropriate knockout found on top
of the steam generator. Mount proper stain
relief into knockout hole.
Strip back the power cable’ s outer insulat-
ing jacket twelve inches and insert into steam
generator. Strip back insulation 1/2" from
the incoming wires; single phase (two power
and one ground). 3 phase (three power and
one ground).
Insert ground wire into grounding lug located
on the lower left side wall of the gray elec-
trical power box.
CAUTION: Insure ground wire does not
come in contact with live electrical connec-
tions.
Locate the fuse block. found in the upper
part of the gray power box. Insert power
wires into the proper power lug terminals
on top of the fuse block and secure.
5)
A.
1)
2)
1)
2)
3)
4)
5 )
2
Locate and remove six (6) screws securing
the access cover to the gray electrical power
box. (See Figure 1.)
1)
Summary of Contents for HC-10
Page 1: ...HEAVY COMMERCIAL STEAMBATH GENERATOR OWNERS MANUAL Models HC 9 Thru HC 18 3 98 Pub No 400 G ...
Page 12: ......
Page 13: ......
Page 14: ......