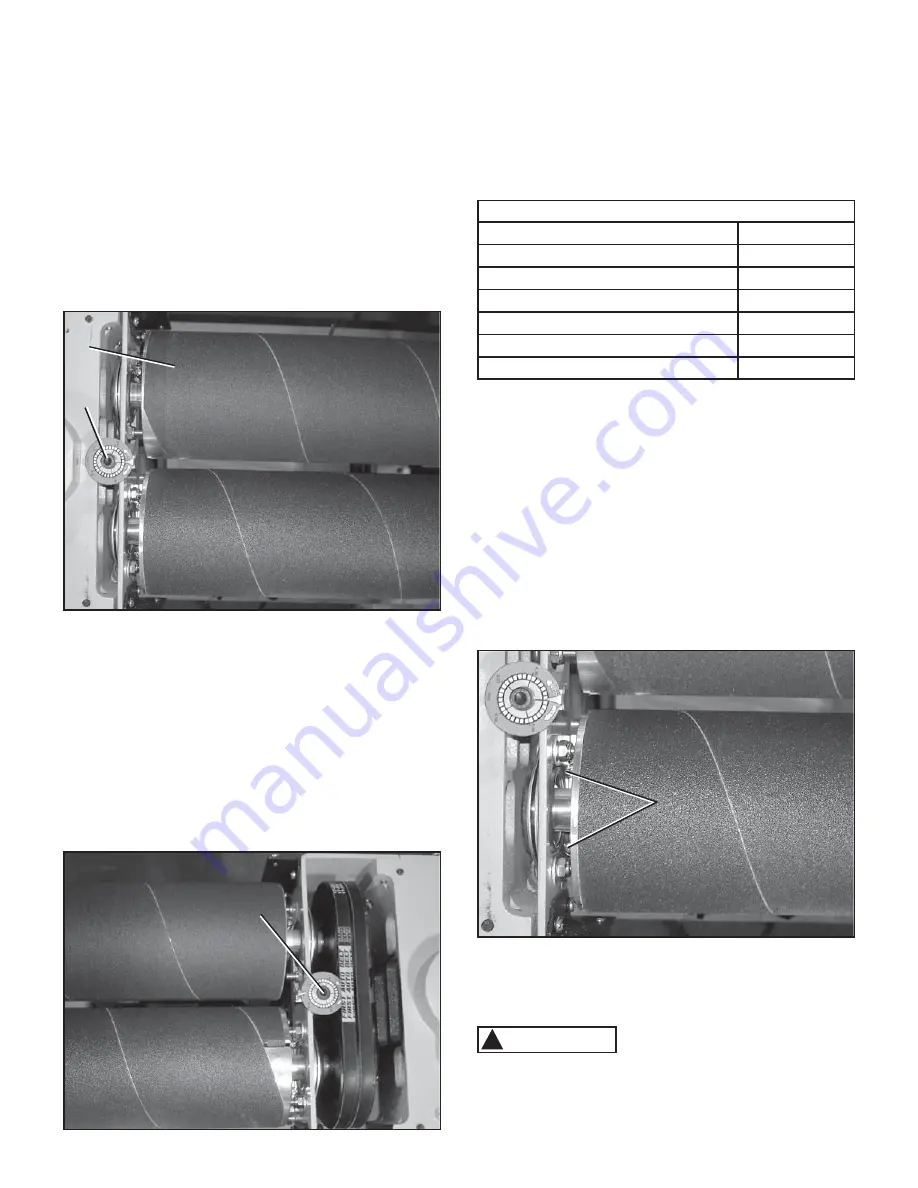
18
PARALLELISM ADJUSTMENT
OF SANDING DRUM
The front sanding drum has been factory adjusted and
needs no further adjustment. The rear sanding drum
must be adjusted for parallelism.
TO ADJUST, FOLLOW THESE PROCEDURES:
1.
Adjust using the cap screws (A) on either end of the
sanding drums (B), using a T-wrench. Turning the
cap screw clockwise will raise the drum while turn-
ing it counterclockwise will lower the drum.
SEE FIG. 10.
2.
Make adjustments to both sides of the rear drum if
necessary, until it is parallel with the front drum.
Fig. 10
A
B
DRUM HEIGHT
When using different abrasive grits on the drums, the
height of the drums from the workpiece must vary. To
achieve this, the back drum (which should always have
the finer grit) has been designed for easy adjustment.
1.
Rotate the cap screw (A) to the desired measure-
ment.
SEE FIG. 11.
2.
Repeat this dial setting on the opposite end of the
drum.
NOTE:
It is important that the dial setting be
identical at both ends of the drum.
IMPORTANT:
After changing abrasive strips, always
check and, if necessary, reset the back drum height.
The chart below shows the proper settings based upon
sanding grits.
Fig. 11
A
REAR DRUM SETTING GAUGE
Front Drum Grit / Rear Drum Grit
Setting (mm)
80/100, 120/150, 120/180, 150/220
.15
80/120, 100/150, 100/180
.30
60/100, 36/38
.40
36/120
.56
36/60
.76
36/80
.93
PRESSURE ROLLERS
The pressure rollers maintain tension upon the work-
piece as it passes through the machine. The spring
tension of the pressure rollers has been factory set.
If a board refuses to pass through the machine, or the
finished surface of a board is uneven, the spring ten-
sion of the pressure rollers may need adjusting.
1.
Turn the Phillips head screws (A), clockwise to
increase the roller pressure on the workpiece; or
counterclockwise to decrease the pressure.
SEE FIG. 12.
Fig. 12
A
2.
Repeat this same adjustment at the opposite end of
the roller to maintain parallel.
3.
Repeat procedure for the other pressure roller.
Do not overtighten the adjusting screw, as excess
roller pressure will prevent the workpiece from
passing through the machine, and may cause the
conveyor belt to stop.
CAUTION
!
Summary of Contents for 55220
Page 28: ......