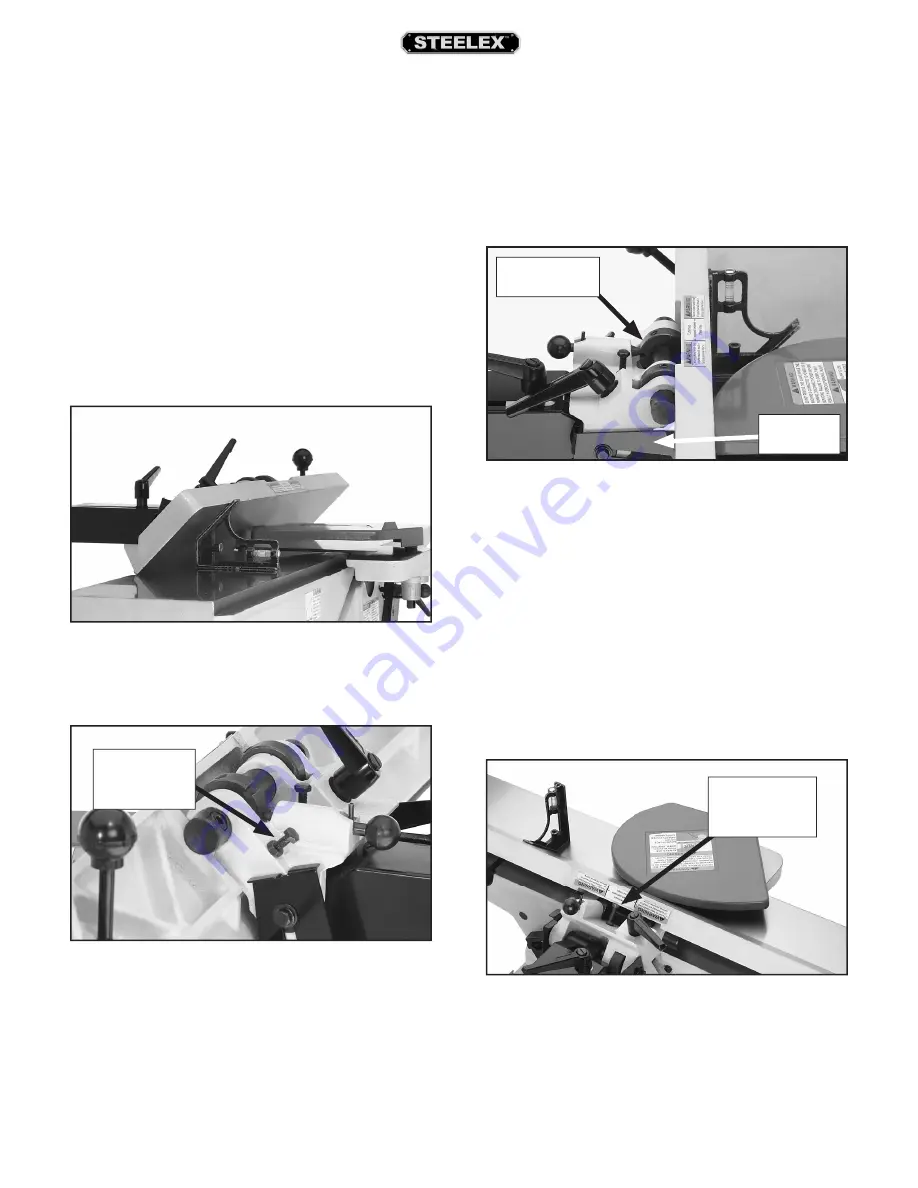
-30-
ST1001 6" Jointer
To set the 90˚ fence stop:
1.
Loosen the set screw in the plunger lock collar,
shown in
Figure 47
, and loosen the fence tilt
lock.
2.
Using a 90° square, adjust the fence to the 90°
position, as shown in
Figure 47
.
3.
Adjust the 45˚ outward positive stop bolt until
the fence is exactly 45° outward while resting
on the bolt.
4.
Retighten the jam nut loosened in
Step 2
.
3.
Tighten the set screw in the plunger lock collar.
4.
Adjust the indicator (if necessary) to 0° to cali-
brate the fence tilt scale.
To set the 45° outward fence stop:
1.
Loosen the fence tilt lock, and position the fence
against the 45° outward positive stop bolt.
2.
Loosen the jam nut on the 45˚ outward fence
positive stop bolt (
Figure 48
).
Figure 47.
Adjusting fence to 90˚.
Plunger Lock
Collar
Fence Tilt
Scale
Figure 48.
Adjusting fence 45˚ outward.
45° Outward
Positive Stop
Bolt
Setting Fence Stops
The fence stops simplify the task of adjusting the
fence to 45˚ inward, 90˚, and 45˚ outward (135˚).
Tools Needed
Qty
45° Square ............................................................................... 1
90° Square ............................................................................... 1
Sliding Bevel ........................................................................... 1
Wrench 10mm ....................................................................... 1
Hex Wrench 4mm ................................................................. 1
To set the 45˚ inward fence stop:
1.
Tilt the fence approximately 45° inward (
Figure
45
) onto the positive stop bolt.
3.
Adjust the positive stop bolt until the fence is
exactly 45° inward while resting on the bolt
(verify the angle with a 45° square).
4.
Retighten the jam nut loosened in
Step 2
.
Figure 45.
Fence adjusted 45˚ inward.
2.
Loosen the jam nut on the 45° inward positive
stop bolt shown in
Figure 46
.
45° Inward
Positive Stop
Bolt
Figure 46.
45° inward positive stop bolt.
Summary of Contents for ST1001
Page 2: ......
Page 36: ...34 ST1001 6 Jointer ST1001 Wiring Diagram...
Page 37: ...ST1001 6 Jointer 35 Jointer Breakdown...
Page 39: ...ST1001 6 Jointer 37 Fence Breakdown...
Page 44: ......
Page 47: ......
Page 48: ......