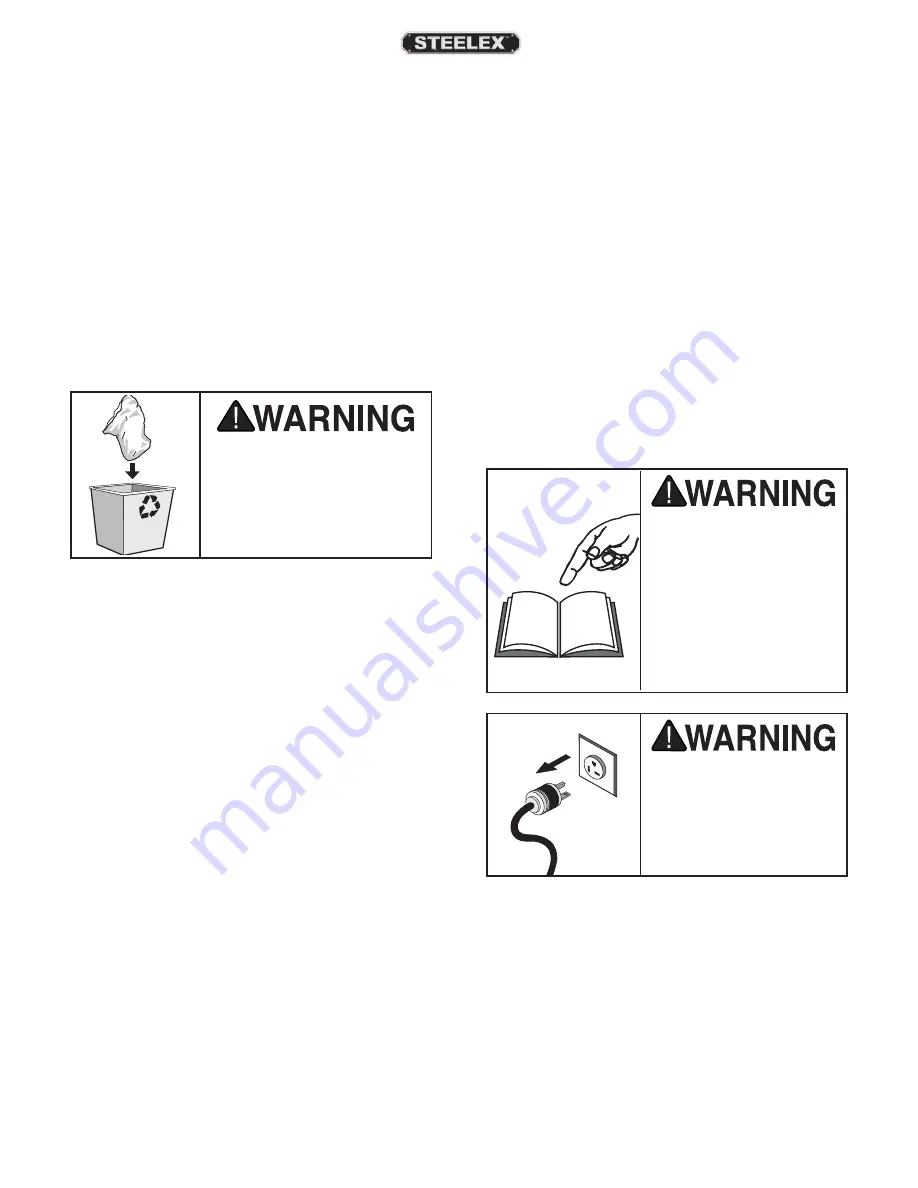
-14-
ST1006/ST1011 8" Jointer (Mfd. Since 3/16)
Unpacking
SETUP
The following items are needed to complete the set
up process, but are not included with your machine:
DESCRIPTION Qty
• Straightedges ............................................................... 1
•
Additional People ....................................................... 4
Phillips Screwdriver #2 .............................................. 1
•
Wrench or Socket 17mm ......................................... 1
•
Wrench or Socket 14mm ......................................... 1
•
Wrench or Socket 13mm ......................................... 1
•
Dust Collection System ............................................ 1
•
Dust Hose 4" ................................................................. 1
Items Needed for
Setup
READ and understand this
entire instruction manual
before using this machine.
Serious personal injury
may occur if safety and
operational information
is not understood and fol-
lowed. DO NOT risk your
safety by not reading!
UNPLUG power cord
before you do any assem-
bly or adjustment tasks!
Otherwise, serious per-
sonal injury to you or oth-
ers may occur!
SUFFOCATION HAZARD!
Immediately discard all plas-
tic bags and packing materi-
als to eliminate choking/suf-
focation hazards for children
and animals.
The Model ST1006/ST1011 was carefully packed
when it left our warehouse. If you discover your
machine is damaged
immediately call your dealer.
Save the containers and all packing materials for pos-
sible inspection by the carrier or its agent.
Otherwise,
filing a freight claim can be difficult.
When you are completely satisfied with the condition
of your shipment, you should inventory the contents.